Industrial Steam Distillation Equipment A Comprehensive Guide
Steam distillation is a crucial process in the chemical, pharmaceutical, and cosmetic industries. It involves the separation of compounds with different boiling points using steam as the heating medium. This method is widely used due to its efficiency, safety, and ability to handle a wide range of materials. In this article, we will discuss the various types of industrial steam distillation equipment and their applications.
1. Simple Steam Distillation
Simple steam distillation is the most basic form of distillation that uses a single vessel for both evaporation and condensation. It is suitable for small-scale operations and can handle liquids with low to moderate volatility. The setup consists of a flask containing the liquid feed, a condenser, and a receiving flask. Steam is introduced at the bottom of the flask, and the resulting vapor rises and passes through the condenser, where it condenses back into a liquid. The condensed liquid is then collected in the receiving flask.
2. fractional distillation
Fractional distillation is a more advanced technique that separates mixtures with multiple components with different boiling points. It is commonly used in the petroleum industry to separate crude oil into various fractions, each with a specific boiling point range. The setup consists of a fractionating column, which is a tall tower filled with packing material. The liquid feed is introduced at the top of the column, and steam is passed through the column from bottom to top. The different components in the liquid feed evaporate at different temperatures, and the vapor rises and condenses on the packing material The different components in the liquid feed evaporate at different temperatures, and the vapor rises and condenses on the packing material
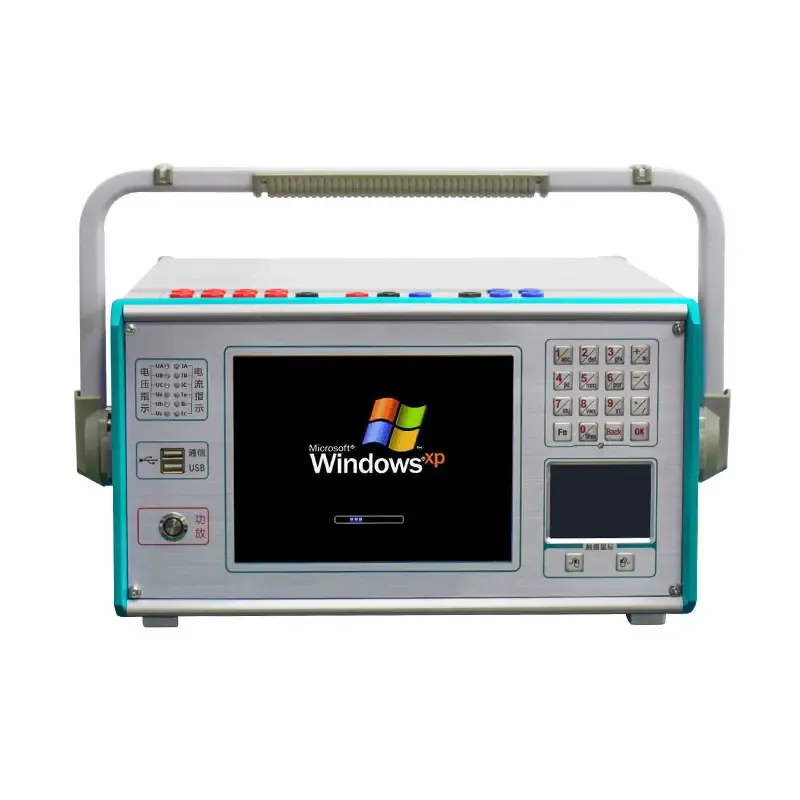
The different components in the liquid feed evaporate at different temperatures, and the vapor rises and condenses on the packing material The different components in the liquid feed evaporate at different temperatures, and the vapor rises and condenses on the packing material
industrial steam distillation equipment. The condensed liquid then flows down the column, and the different fractions are collected at different levels based on their boiling points.
3. vacuum distillation
Vacuum distillation is a variation of steam distillation that operates at reduced pressure. This allows for the separation of compounds with higher boiling points that would otherwise decompose or require too much energy to vaporize under atmospheric conditions. The setup consists of a distillation flask, a condenser, and a vacuum pump. The liquid feed is heated in the distillation flask, and the resulting vapor is drawn through the condenser by the vacuum pump. The condensed liquid is then collected in the receiving flask.
4. molecular distillation
Molecular distillation is a specialized form of distillation that operates at extremely low pressures and high temperatures. It is used to separate compounds with very similar boiling points, such as lipids and essential oils. The setup consists of a thin film evaporator, which is a heated surface onto which the liquid feed is spread as a thin film. The vaporized compounds then pass through a short path between two heated surfaces, where they condense and are collected.
In conclusion, industrial steam distillation equipment plays a vital role in various industries by providing efficient and reliable methods for separating compounds with different boiling points. From simple steam distillation to advanced techniques like fractional and vacuum distillation, these equipment options cater to different processing requirements and offer a wide range of benefits.