In the realm of electrical engineering, the cable resistance test stands out as a critical procedure for evaluating the integrity and performance of electrical cables. This test is a vital component in ensuring safety and efficiency in electrical systems. Understanding its significance and methodology not only underscores good engineering practices but also aligns with industry standards, reinforcing the need for trust and authority in handling electrical components.
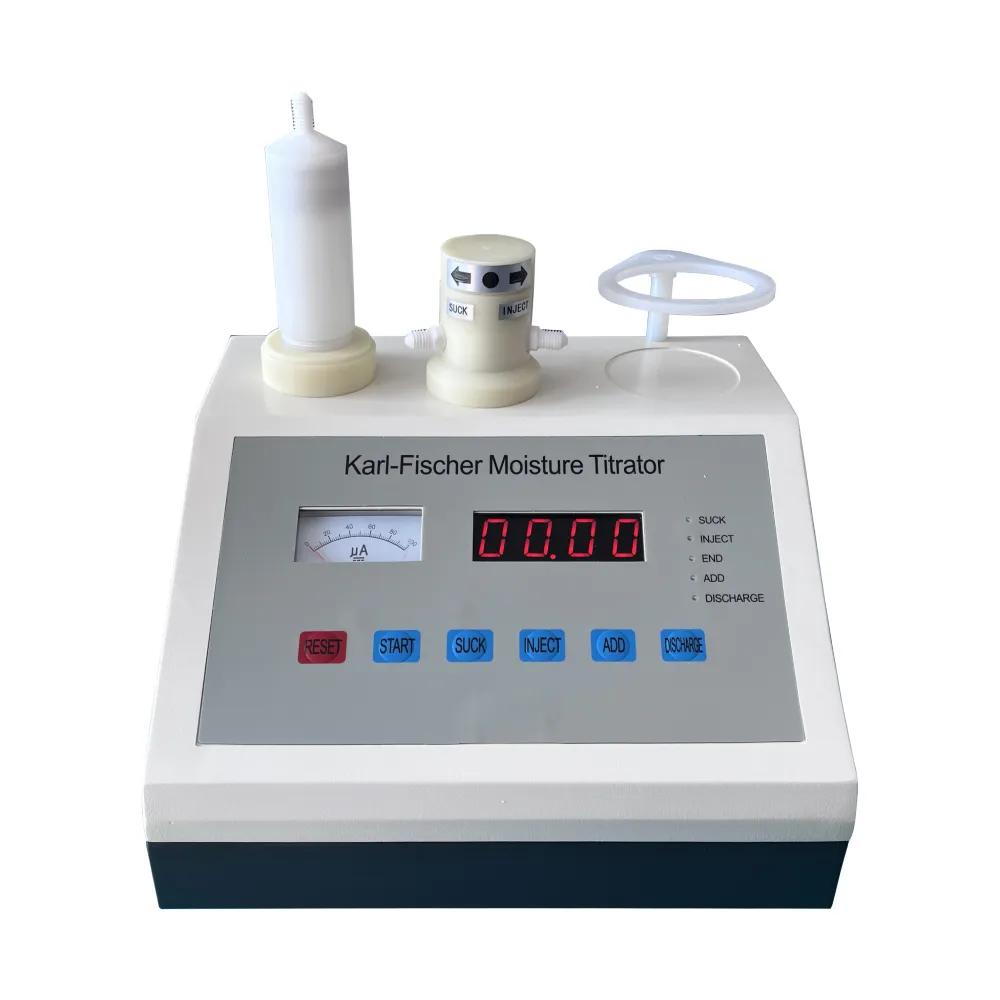
Cable resistance testing involves measuring the opposition to current flow within a cable. This measurement is paramount because excessive resistance can lead to overheating, power loss, and even catastrophic failures in electrical systems. Expertise in this area is crucial, as accurate measurement and interpretation of resistance values are indispensable for diagnosing potential issues.
Conducting a cable resistance test begins with selecting the appropriate equipment. A micro-ohmmeter or a digital multimeter with high precision is typically used. These instruments are designed to measure low resistance values, making them ideal for this test. The process involves connecting the leads of the meter to the ends of the cable with secure connections to ensure accuracy. By applying a known current through the cable and measuring the voltage drop, the resistance can be calculated using Ohm’s Law (R = V/I).
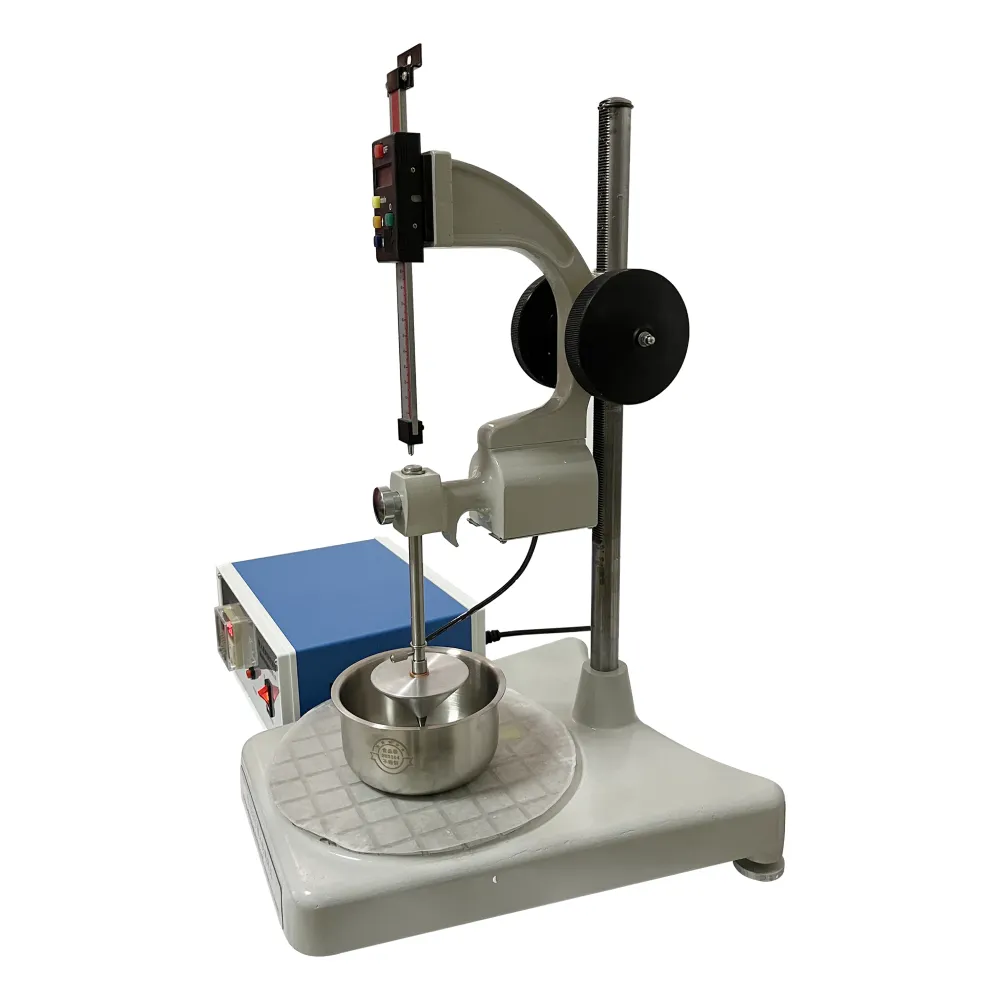
The expertise involved in the cable resistance test doesn’t stop at just taking measurements. It requires a thorough understanding of the cable specifications and the environment in which the cable operates. Cables in high-temperature environments or those that carry high currents are more susceptible to changes in resistance. Therefore, an authoritative understanding of how different conditions affect resistance readings is necessary to make informed assessments about cable health.
cable resistance test
Trustworthiness in the results is achieved through rigorous testing protocols and adherence to standards such as the International Electrotechnical Commission (IEC) and the American National Standards Institute (ANSI). These standards define the acceptable resistance ranges for different types of cables, ensuring that professionals have a reliable benchmark against which they can evaluate their test results. Furthermore, implementing consistent testing intervals as part of regular maintenance schedules helps in the early detection of potential issues. This proactive approach establishes a reliable track record that stakeholders can trust.
Experience plays a crucial role in the testing process. Experienced technicians are adept at identifying subtle discrepancies in resistance values that may indicate underlying issues such as corrosion, insulation degradation, or manufacturing defects. Such insight requires years of hands-on experience and comprehensive training.
An additional element enhancing the expertise of the cable resistance test is the application of advanced diagnostic techniques, such as time-domain reflectometry (TDR). TDR can help pinpoint the exact location of resistance anomalies along the length of a cable, providing a more detailed analysis than standard resistance measurements alone. This advanced method is invaluable in complex systems where cable routing might obscure visual inspections.
Ultimately, the cable resistance test is not just a measurement. It is an essential procedure backed by technical expertise, adherence to standards, and a commitment to ensuring the longevity and safety of electrical systems. This test acts as a preventive measure, safeguarding infrastructure by anticipating potential failures before they manifest, thus affirming its standing as a cornerstone of electrical maintenance and quality assurance. Professionals involved in these tests not only contribute to the immediate safety of electrical systems but also uphold the broader standards of engineering excellence.