The Critical Role of CT Winding Resistance Test in Electrical Equipment Maintenance
Introduction
The winding resistance test is an essential diagnostic tool for assessing the health of electrical equipment, particularly transformers. It helps detect issues such as loose connections, insulation degradation, and overheating, which can lead to catastrophic failures if left unaddressed. This article delves into the significance of the CT (Current Transformer) winding resistance test and its application in maintaining electrical systems.
CT Winding Resistance Test An Overview
A CT is a type of transformer that is used to measure high currents in power systems. It consists of a primary winding, which carries the high current, and a secondary winding, which provides a scaled-down current that can be measured by instruments. The accuracy of the CT's measurement depends on its winding resistance, which must be within specified limits to ensure reliable operation.
Why Conduct a CT Winding Resistance Test?
There are several reasons why conducting a CT winding resistance test is crucial
1. Early Detection of Issues By regularly testing the winding resistance, technicians can identify potential problems before they escalate into major failures. This allows for timely maintenance and prevents unscheduled downtime.
2. Safety A faulty CT can pose a serious safety risk by providing inaccurate current readings. A winding resistance test helps ensure that the CT is functioning correctly and providing accurate measurements, thereby enhancing safety in electrical systems.
3. Compliance with Regulations Many electrical codes and standards require periodic testing of CTs to ensure their reliability. Failing to comply with these regulations can result in fines or even suspension of electrical service.
4. Improved System Performance Regularly testing CT winding resistance helps maintain the overall performance of electrical systems by ensuring that all components are functioning optimally Improved System Performance Regularly testing CT winding resistance helps maintain the overall performance of electrical systems by ensuring that all components are functioning optimally
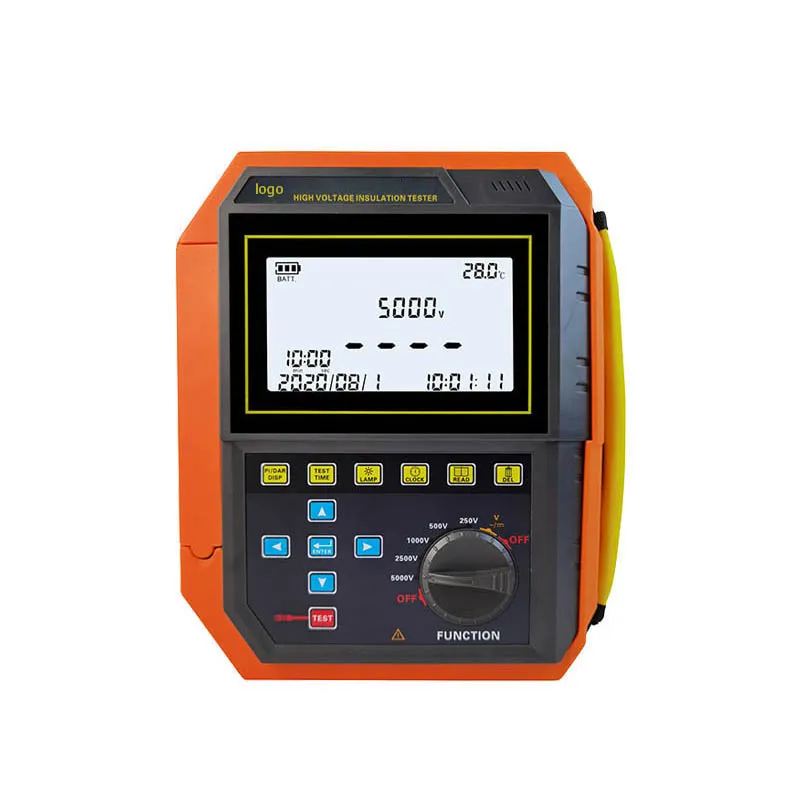
Improved System Performance Regularly testing CT winding resistance helps maintain the overall performance of electrical systems by ensuring that all components are functioning optimally Improved System Performance Regularly testing CT winding resistance helps maintain the overall performance of electrical systems by ensuring that all components are functioning optimally
ct winding resistance test. This leads to increased efficiency, reduced energy consumption, and longer equipment lifespan.
How to Conduct a CT Winding Resistance Test
The process of conducting a CT winding resistance test involves the following steps
1. Disconnect the CT from the electrical system to ensure safety during the test.
2. Use a low-voltage source to apply a known current to the CT's primary winding.
3. Measure the voltage across the secondary winding using a multimeter or other appropriate instrument.
4. Calculate the winding resistance using Ohm's Law (R = V/I), where R is the resistance, V is the voltage, and I is the current.
5. Compare the calculated resistance with the manufacturer's specifications to determine if it falls within acceptable limits.
Conclusion
In conclusion, the CT winding resistance test is a critical diagnostic tool for maintaining electrical systems and ensuring the safe and reliable operation of transformers. By regularly conducting this test, technicians can identify and address potential issues early on, preventing major failures and reducing downtime. As such, it is essential to incorporate CT winding resistance testing into regular maintenance schedules and comply with relevant regulations to ensure the longevity and optimal performance of electrical systems.