Exploring DC Insulation Resistance Testing An In-Depth Guide for Professionals
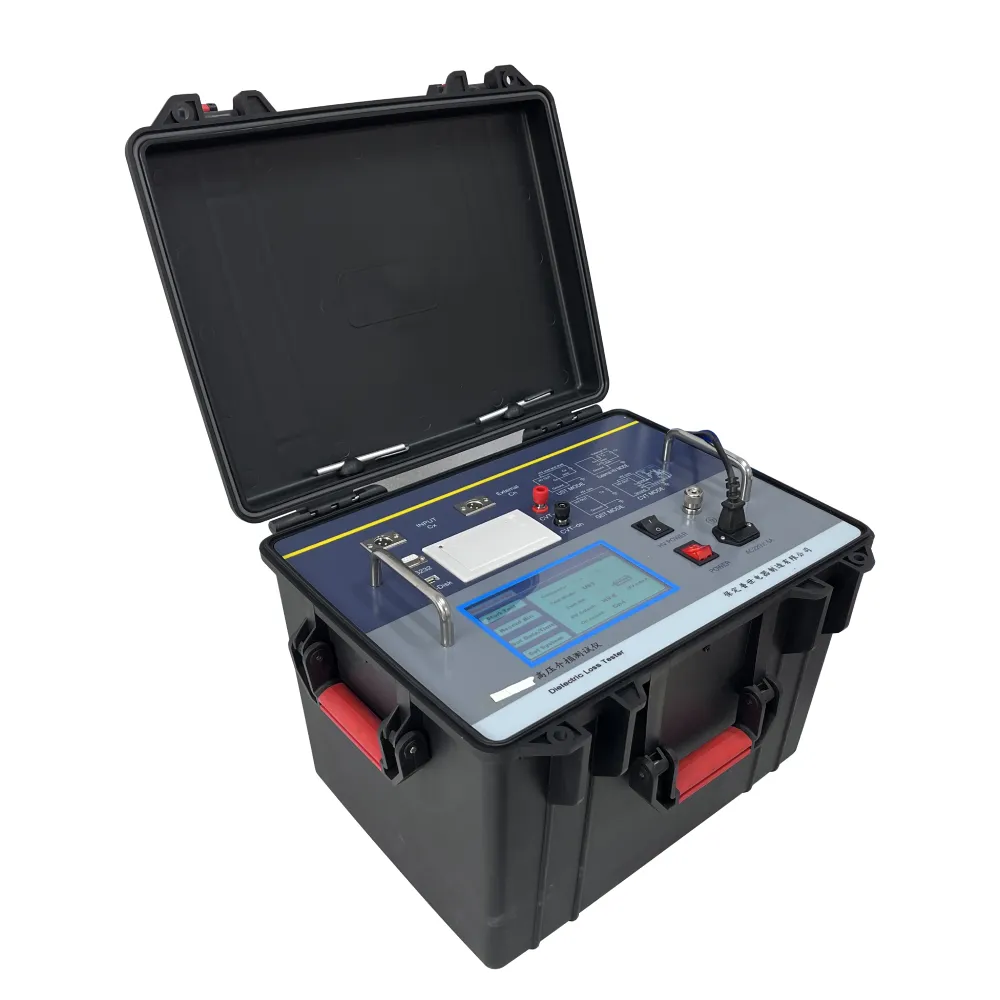
The longevity and reliability of electrical equipment are paramount in industries ranging from telecommunication to power distribution. At the heart of ensuring this reliability lies the practice of insulation resistance testing, a critical maintenance step that electrical engineers rely on significantly. This technique, specifically the DC insulation resistance test, serves as both a preventive maintenance measure and a diagnostic tool, identifying potential issues before they become major problems.
Understanding the Mechanism
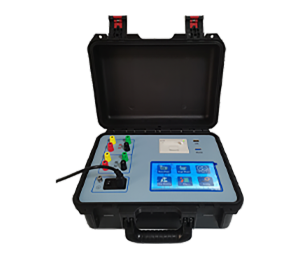
DC insulation resistance testing involves applying a direct current (DC) voltage across the insulation of electrical equipment and measuring the resistance. This test's primary goal is to assess the integrity of insulation materials used in various electrical devices, including transformers, motors, and cables.
Why is DC utilized? The nature of DC allows for more stable and consistent measurements, avoiding the capacitive effects that can skew results in AC testing. By utilizing a DC voltage, it's possible to obtain a true resistance value, which is crucial in evaluating insulation quality.
Real-World Applications and Advantages
DC insulation resistance tests are indispensable in scenarios where reliable long-term performance of electrical components is mandatory. Industries that operate under harsh environmental conditions, such as marine operations or those involving extreme temperatures, greatly benefit from regular resistance testing. In these contexts, insulation resistance testing provides critical data that informs maintenance schedules and helps prevent unforeseen downtimes.
One of the primary advantages of DC insulation resistance tests is their ability to identify gradual deterioration of insulation materials. Unlike more abrupt failures, progressive deterioration often goes unnoticed until it leads to complete insulation breakdown. Addressing these issues proactively can dramatically extend the lifespan of equipment and reduce costly emergency shutdowns.
Expert Insight Conducting Effective Tests
To ensure accurate test results, it is essential that the testing process follows standardized procedures, typically outlined by international standards such as IEEE or IEC. These guidelines cover aspects such as the voltage level to be used, the setup of the test, and the duration.
dc insulation resistance test
A critical step involves preparing the equipment under test. Before initiating, ensure all electrical apparatus is de-energized and properly discharged to prevent hazards. An important parameter is the test voltage, which should be selected based on the equipment’s rated operating voltage to avoid damage.
ADE Testing Services, a leader in electrical assessment, emphasizes the importance of temperature monitoring during the test. As temperature significantly affects resistance measurements, recording ambient conditions ensures results are contextualized accurately. For instance, resistance values typically decrease with rising temperatures; hence, understanding temperature influence allows for more precise analysis.
Expertise and equipment are key. Modern insulation resistance testers come equipped with advanced features such as time-resistance testing capabilities (i.e.,
polarization index test), which enhance fault diagnosis depth.
Cultivating Trusted Practices
Establishing a routine insulation resistance testing schedule fosters a robust maintenance culture that preemptively tackles potential issues. Organizations that prioritize such testing are often seen as proactive in safeguarding their operational integrity.
Documentation plays an invaluable role in this process. By meticulously recording each test and analyzing trends over time, engineers can detect degradation patterns, highlight persistent issues, and optimize future equipment purchases based on insulation performance history.
Investment in continuous training ensures that the latest techniques and technologies in insulation resistance testing are at the fingertips of professionals. This dedication to expertise not only builds trust with regulatory bodies but also with clients and stakeholders banking on quality assurance.
Compliant documentation and an unwavering commitment to technical excellence amplify the authority of organizations through demonstrable reliability achievements.
Conclusion
DC insulation resistance testing stands as a cornerstone practice in the maintenance and management of electrical systems. As industries evolve and equipment becomes more sophisticated, the demand for precise, expert, and authoritative testing methodologies will only increase. Embracing such tests not only extends the life and efficiency of equipment but fortifies an organization’s reputation as a trusted entity in the electrical maintenance landscape.