The DC resistance test of transformers plays a critical role in their maintenance and operational efficiency. This test, while seemingly straightforward, involves a nuanced understanding that combines technical expertise with practical experience. For professionals in the field, the ability to precisely measure and analyze the DC resistance of transformer windings is essential, not merely for ensuring compliance with industry standards but also for improving transformer performance and lifetime.
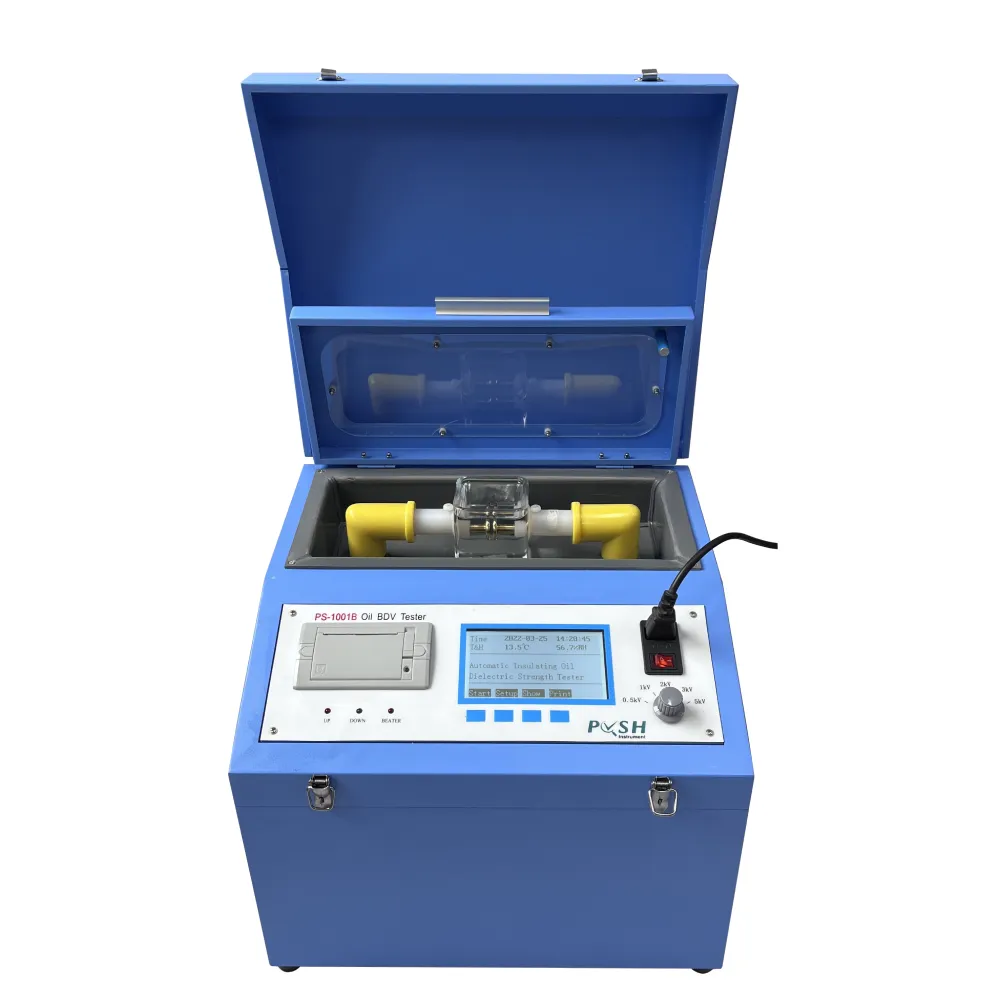
Transformers, the backbone of electrical grids, are subject to various stresses, both electrical and mechanical. The DC resistance test serves as an early indicator of potential problems, such as broken strands in windings, poor electrical connections, and other faults that might compromise the transformer's functionality. When preparing for a DC resistance test, it is imperative to have a comprehensive understanding of the transformer's specifications and history. This involves analyzing the type of transformer, its configuration (whether it’s a single-phase or three-phase unit), and the manufacturer's guidelines for testing procedures.
In practice, conducting a DC resistance test requires specialized equipment and tools. A high-precision micro-ohmmeter is generally recommended, as it can provide accurate readings that are crucial for determining the condition of the transformer windings. The testing process starts with ensuring the transformer is properly de-energized and grounded. Safety is paramount, so utilizing lockout and tagout procedures is non-negotiable. It’s also important to consider environmental conditions, as temperature variations can affect resistance readings, necessitating temperature correction algorithms to interpret the data accurately.
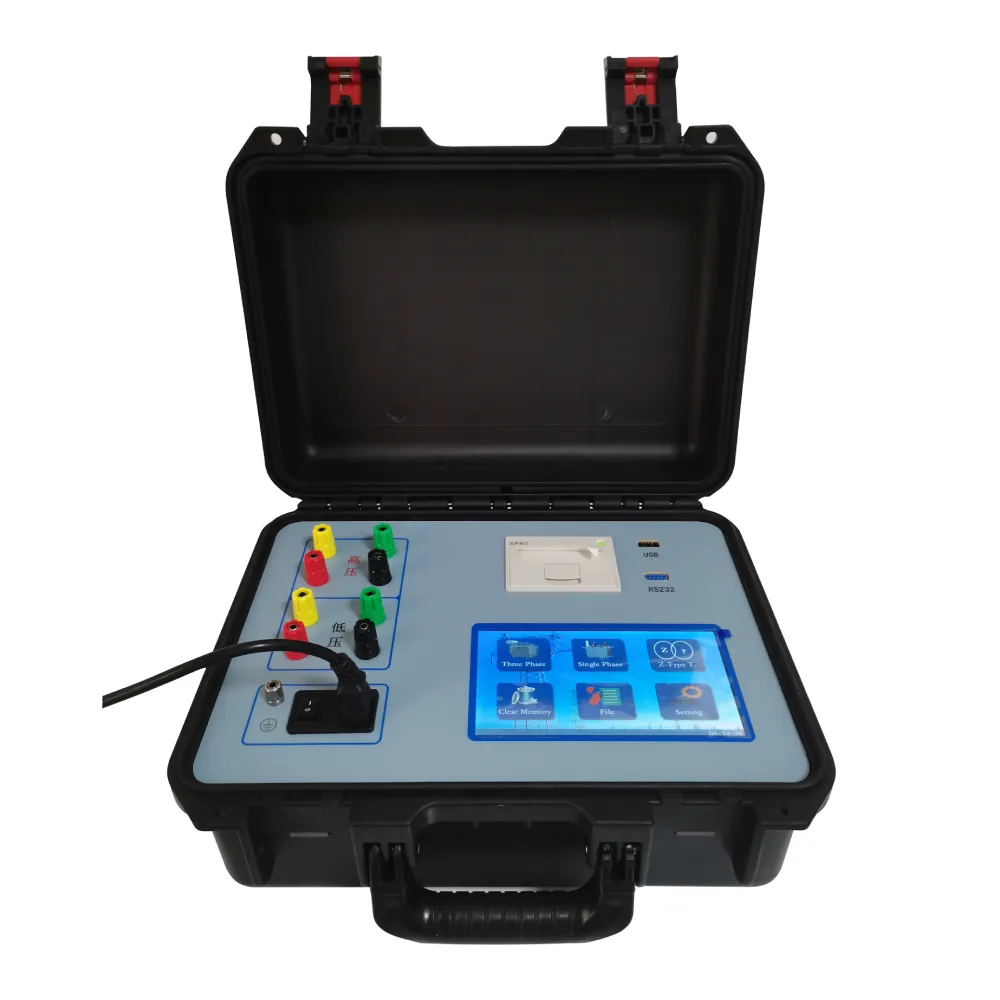
One must also consider the expertise required in interpreting DC resistance test results. Results showing low winding resistance indicate a healthy state, whereas higher resistance readings may suggest potential issues like loose connections or corrosion. Consistency across phases is crucial; any significant disparity warrants further investigation. An expert tester will not only look at the absolute values but also analyze trends over time, which can provide invaluable insights into the aging process of the transformer components.
Should discrepancies arise in the readings, a seasoned engineer will go beyond the numbers, delving into the possible causes, which might include thermal issues, mechanical vibrations, or even manufacturing defects that have only manifested over time. Troubleshooting these issues requires a methodical approach, often involving additional tests or inspections, such as thermographic analysis or visual inspections of intervals and connections.
dc resistance test of transformer
Maintaining authority and trustworthiness in DC resistance testing comes from continuous education and adherence to the latest industry standards and best practices. Professional organizations like the IEEE provide guidelines and updates that are critical for staying informed about new advancements and techniques in transformer testing. Additionally, leveraging data analytics and digital monitoring systems can enhance the diagnostic capabilities, allowing engineers to predict failures before they occur, thereby optimizing maintenance schedules and reducing unexpected downtimes.
Record-keeping is another essential aspect that underscores the trustworthiness of DC resistance testing. Detailed documentation of test results, environmental conditions, equipment calibration records, and even tester qualifications can establish a comprehensive profile for each transformer. This data, stored and analyzed over time, is invaluable for predictive maintenance programs, contributing to the transformer’s long-term reliability and performance.
Finally, stakeholder communication is a vital component of DC resistance testing. Providing clear, concise reports that outline test results, interpretations, and recommendations to the plant management or clients fosters transparency and confidence. A skilled engineer should be able to translate technical data into actionable insights, helping decision-makers weigh the risks and benefits of maintenance actions. Building this line of communication aids in establishing trust and demonstrates the engineer's authority and professionalism in the field.
In conclusion, the DC resistance test of transformers is not merely a procedural task but a complex process that relies on expertise, attention to detail, and a commitment to safety and accuracy. By following industry best practices and continuously updating skill sets, professionals can assure the stakeholders of the reliability and efficiency of their transformer assets.