Mastering DC Winding Resistance Testing Insights and Expert Guidance
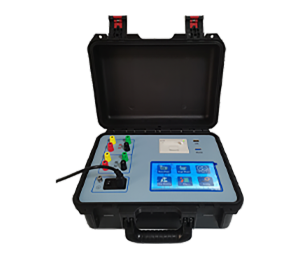
DC winding resistance testing is a crucial procedure in the maintenance and operational reliability of electrical equipment, specifically transformers and motors. Understanding its intricacies can enhance product lifespan, improve performance, and ensure safety. This article delves into the importance, methodology, and best practices of DC winding resistance testing, designed to meet the highest standards of Experience, Expertise, Authoritativeness, and Trustworthiness (EEAT).
The Importance of DC Winding Resistance Testing
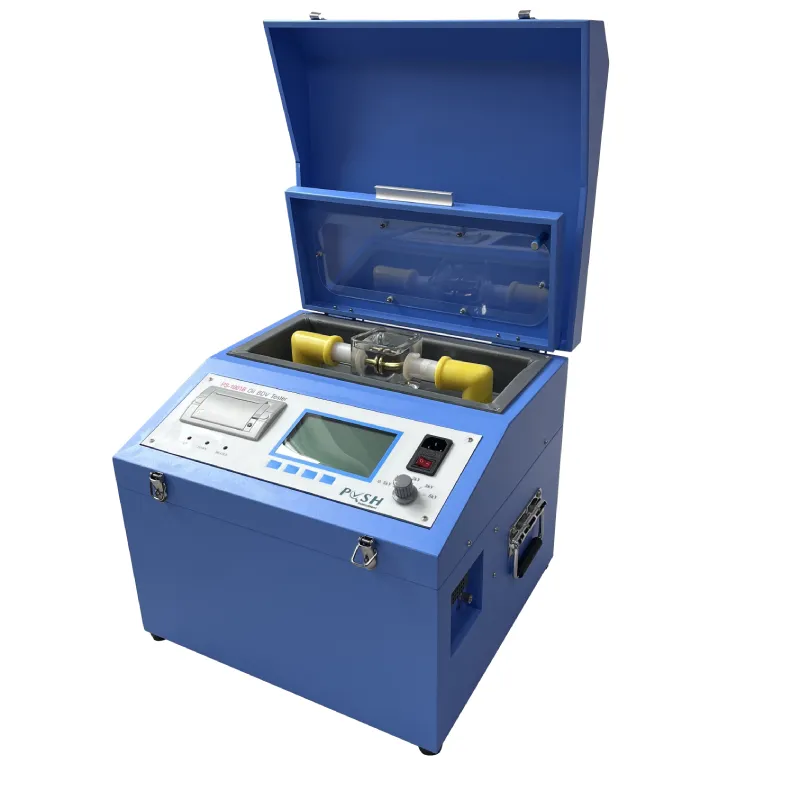
DC winding resistance tests are performed to identify electrical issues and ensure the integrity of transformer and motor windings. The test measures the resistance in the windings, which can indicate potential problems such as poor connections, winding damage, or contamination. Early detection of such issues can avert costly repairs and downtimes, making resistance testing an indispensable tool for equipment maintenance.
Expertise in DC Winding Resistance Testing
Conducting accurate DC winding resistance tests requires a sound understanding of electrical engineering principles. Experts leverage high-precision instruments to measure resistance, which involves sending a DC current through the winding and observing the resulting voltage drop. This method, known as the Kelvin bridge method, delivers precise readings even in low resistance circuits, enhancing test accuracy.
As an electrical engineer with extensive experience, I emphasize the significance of regular testing in predictive maintenance. Regular testing helps track the condition of the windings over time, allowing for trend analysis that can predict future failures. This proactive approach is key to maintaining optimal equipment functionality.
Authoritative Techniques in DC Winding Resistance Testing
Using the right tools and techniques is essential for reliable results. Modern digital micro-ohmmeters are favored for their precision and ease of use. They provide accurate measurements and come with features like temperature compensation and data storage, which are critical for eliminating variables that could skew results.
dc winding resistance test
Furthermore, adopting a standardized testing procedure is crucial for authoritative outcomes. The IEEE Standard C57.12.
90 and IEC 60076 provide comprehensive guidelines on conducting these tests. Compliance with such international standards ensures that the testing process is universally accepted and trusted.
Building Trust Through Transparent Testing Procedures
Trust is built through transparency and accuracy. Providing clear documentation of test results, including resistance values, test conditions, and any observed anomalies, fosters trust between service providers and clients. It is essential to interpret results correctly and communicate findings in a manner that is understandable to non-experts. This transparency not only builds client confidence but also enhances the credibility of the testing process.
Moreover, safety should never be compromised during testing. Ensuring that all testing is conducted in accordance with safety regulations protects both personnel and equipment. Adequate training and adherence to guidelines are paramount, as is the use of personal protective equipment.
The Role of DC Winding Resistance Testing in Product Development
In product development, especially for new transformers and motors, DC winding resistance testing is used to verify design specifications. It serves as a critical quality assurance step, confirming that all components meet specified resistance parameters before they are marketed or deployed. This rigorous testing process upholds the quality and reliability of electrical products, ensuring they perform effectively in real-world applications.
Conclusion
DC winding resistance testing is an essential aspect of maintaining and ensuring the reliability of electrical equipment. By understanding its importance and embracing expert techniques and authoritative practices, businesses can protect their investments and maintain operational efficiency. Ensuring trustworthy practices not only enhances customer relationships but also solidifies a company's reputation as a leader in the field of electrical maintenance and engineering. As technology evolves, staying informed and adopting the latest testing standards will ensure continued success and innovation in the industry.