The Efficiency and Applications of Double Distillation Units
In the realm of chemical engineering and refining processes, the double distillation unit stands as a pivotal piece of equipment. This advanced distillation system is designed to purify liquid mixtures by separating components based on their different boiling points through two successive distillation processes.
The operation of a double distillation unit begins with the initial separation process in the primary column. Here, the mixture is heated, and vapor rises, enriching the more volatile components at the top while leaving behind the less volatile ones at the bottom. This first step achieves a significant degree of separation but often fails to produce fractions that meet the stringent purity requirements for certain applications. Hence, the second distillation column comes into play.
The partially purified vapor from the first column is then introduced into the secondary column, where it undergoes further distillation. This secondary process allows for an even finer degree of separation, resulting in highly purified end products. Such a meticulous two-step distillation process is particularly crucial in industries such as petrochemicals, pharmaceuticals, and specialty chemicals, where product purity can make all the difference.
One of the notable advantages of a double distillation unit is its ability to handle thermosensitive materials. By carefully controlling temperatures and pressures within the columns, thermal degradation of sensitive compounds can be minimized. Furthermore, this setup allows for the recovery of intermediate boiling components that might otherwise be lost in a single-column process Furthermore, this setup allows for the recovery of intermediate boiling components that might otherwise be lost in a single-column process
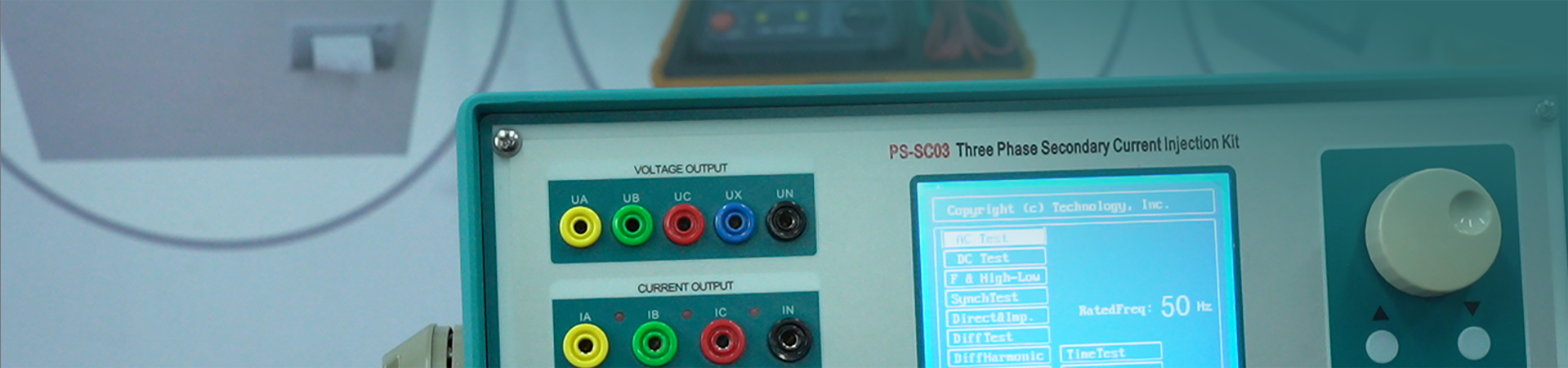
Furthermore, this setup allows for the recovery of intermediate boiling components that might otherwise be lost in a single-column process Furthermore, this setup allows for the recovery of intermediate boiling components that might otherwise be lost in a single-column process
double distillation unit.
The efficiency of a double distillation unit is also enhanced by its energy-integrated design. Heat exchange between the two columns can be optimized, where the condensing vapor from the second column provides the necessary heat for the first column to operate. This not only saves energy but also reduces operating costs significantly.
In terms of applications, double distillation units are indispensable in producing high-quality fuels, solvents, and polymers. They are also essential in the production of alcoholic beverages, where precise control over the composition and quality of the final product is paramount. In the electronics industry, these units help purify solvents used in cleaning processes, ensuring no contaminants that could compromise the integrity of microchips.
In conclusion, the double distillation unit is a testament to the innovation and precision required in modern industrial processes. Its capability to yield high-purity substances efficiently and economically makes it a cornerstone of many manufacturing sectors. As technology continues to evolve, it is likely that advancements in double distillation will further enhance its efficacy and broaden its application spectrum, solidifying its status as an indispensable tool in the pursuit of pure substances.