Electrical insulation resistance testing is a critical aspect of ensuring the safety and efficiency of electrical systems. As an experienced engineer who has spent years in the field testing a variety of electrical equipment, I can affirm that this process not only helps in preventing equipment failure but also in safeguarding personnel and property.

The importance of insulation resistance testing lies in its ability to detect deteriorations or faults in the insulating materials of electrical equipment. Over time, insulation can degrade due to environmental factors, mechanical stresses, and electrical stresses, leading to potential hazards such as short circuits or even electrical fires.
For those involved in the purchase or maintenance of electrical products, understanding the nuances of insulation resistance testing can provide a significant advantage. Here's a closer look at why this testing is essential and how it is expertly performed.
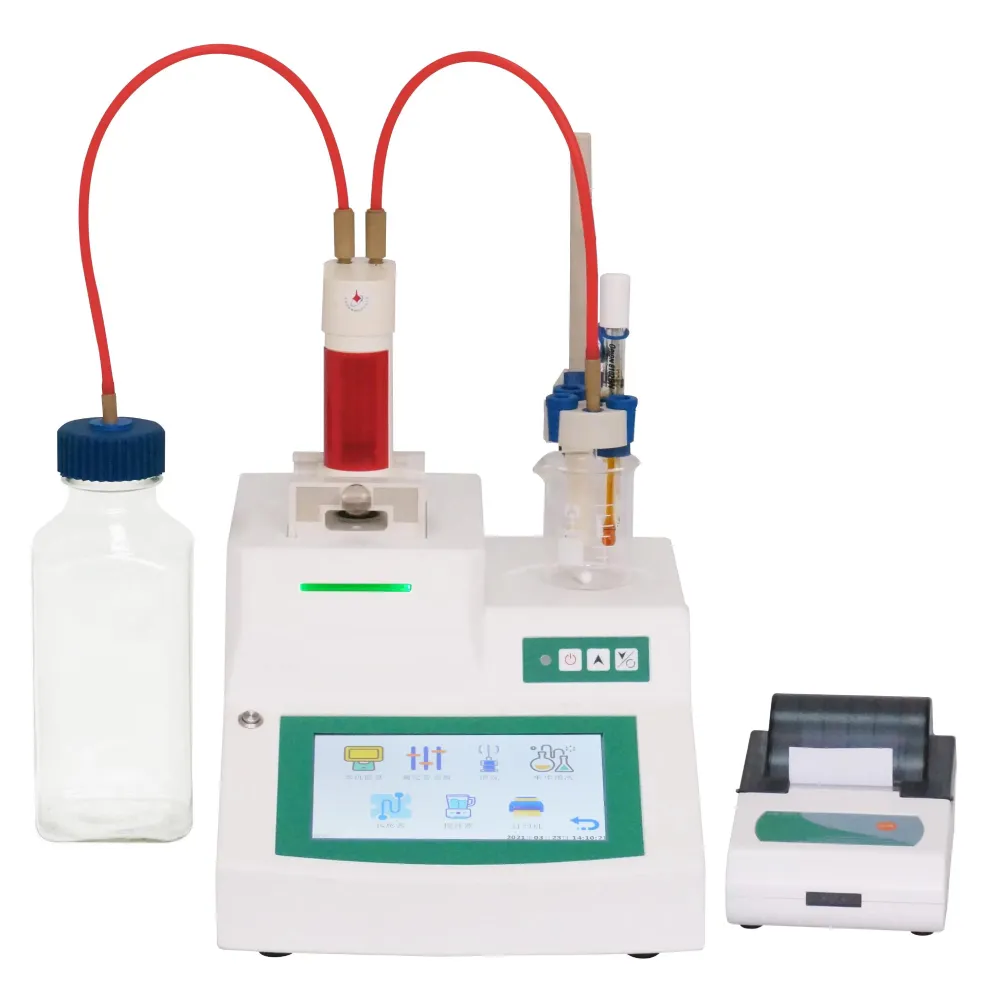
The integrity of an electrical system largely depends on the quality of its insulation. Testing helps in determining the insulation's ability to resist electrical leakage. Typically, these tests involve applying a controlled high voltage to the insulation and measuring how much current leaks through. This test is not only simple to perform with the right equipment but is also incredibly telling of the insulation's effectiveness.
When selecting products, look for ones that guarantee frequent testing as part of their quality control process. Manufacturers who adhere strictly to international standards for insulation resistance demonstrate a commitment to excellence and reliability. Knowing that a product has undergone rigorous testing can reassure users about its long-term performance and safety.
electrical insulation resistance testing
A profound realization from my extensive field experience is the significance of preemptive testing. Many organizations fail to conduct regular insulation resistance tests, resulting in unexpected and costly downtimes. Incorporating regular testing schedules into maintenance routines can help identify potential issues before they escalate into major failures.
It is crucial for industries such as manufacturing, transportation, and construction to invest in high-quality insulation resistance testers. These devices are designed not just for testing, but for providing precise, reliable readings that inform maintenance and safety decisions. With advancements in technology, modern insulation resistance testers offer features like data connectivity and analysis, providing more insight than ever before.
Consider purchasing testers from reputable brands that provide warranties and calibrations services. A reliable manufacturer will offer support, ensuring that the testers remain accurate and serviceable throughout their operational life. This level of service further enhances trust and confidence in the equipment you choose.
Moreover, expertise in interpreting test results is invaluable. A proper understanding of the resistance values and trends can more effectively indicate when an electrical component is due for replacement. This expertise can be developed through training and resources provided by manufacturers.
In conclusion, electrical insulation resistance testing is not merely a maintenance task but a critical strategy for ensuring the operational integrity and safety of electrical systems. By investing in quality products, committing to routine testing, and understanding test results, industries can significantly mitigate risks associated with electrical failures. Trustworthy manufacturers and service providers serve as essential partners in this pursuit, offering the necessary tools and expertise to master this aspect of electrical system management.