The flash point closed cup test holds a crucial place in the evaluation of chemical substances, particularly for industries involved in manufacturing, handling, and transporting flammable liquids. This test determines the lowest temperature at which a substance can vaporize to form an ignitable mixture in air. Recognized for its precision, the closed cup method is often preferred over the open cup test due to its enhanced safety and accuracy. Here, we delve into a comprehensive analysis of this method, offering insights, authentic expertise, and trustworthiness for those involved in quality control and safety assessments.
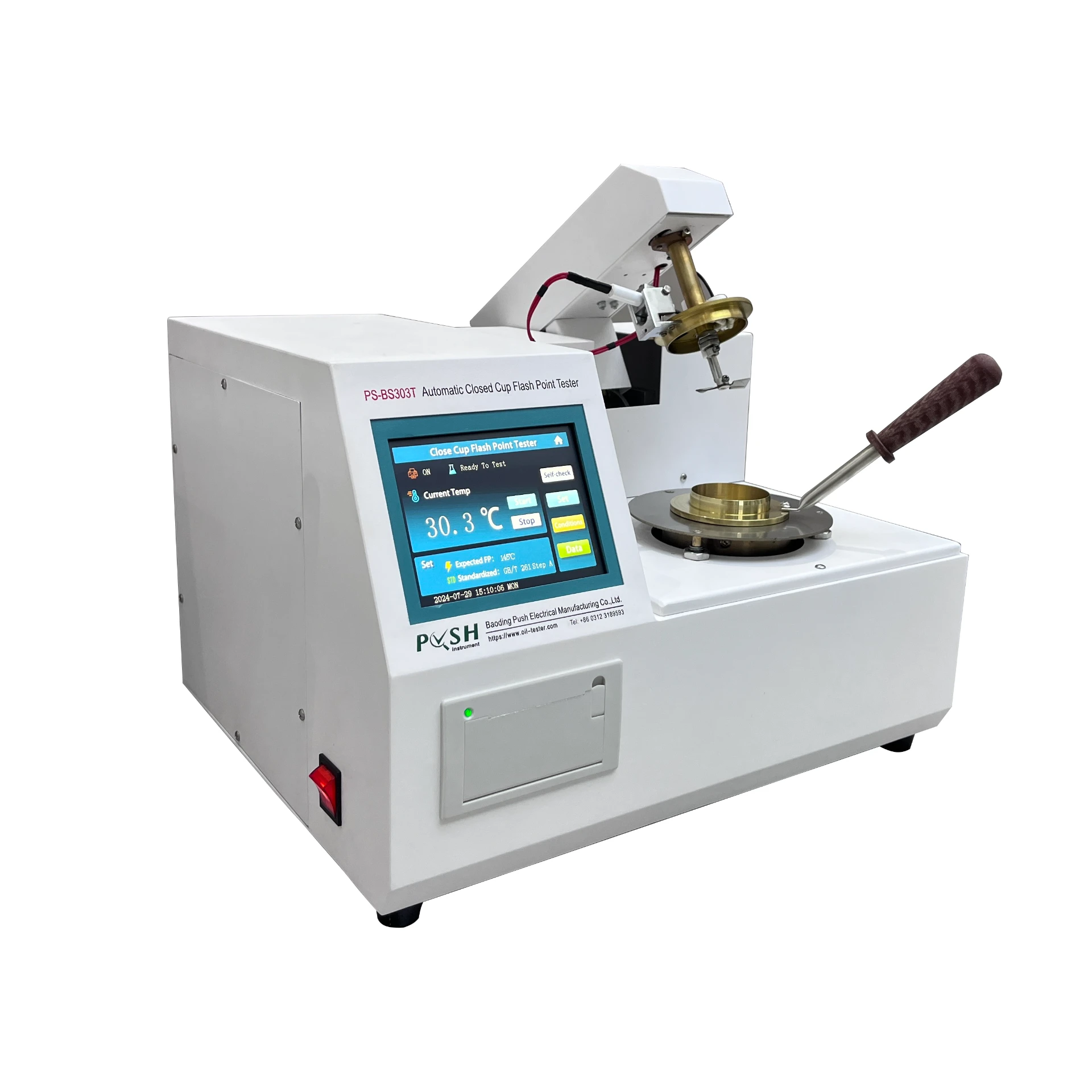
The importance of the flash point in industrial settings cannot be understated. It is an essential parameter for complying with regulatory requirements, assessing potential risks, and implementing safety measures. The closed cup method is employed across various industries, including petrochemicals, pharmaceuticals, and coatings. The method provides a controlled environment that reduces the risk of evaporation losses, ensuring that the test conditions mimic those encountered in real-life scenarios.
Professionals relying on the flash point closed cup test benefit from its authority in establishing consistent safety standards. The test is governed by established protocols, such as ASTM D93 and ISO 2719, which provide comprehensive guidelines to ensure accurate results. Expert technicians prioritize these standards to maintain compliance with safety regulations and prevent workplace hazards associated with flammable materials. Moreover, adherence to these standardized methods enhances the dependability of the data collected, bolstering the credibility of safety assessments.
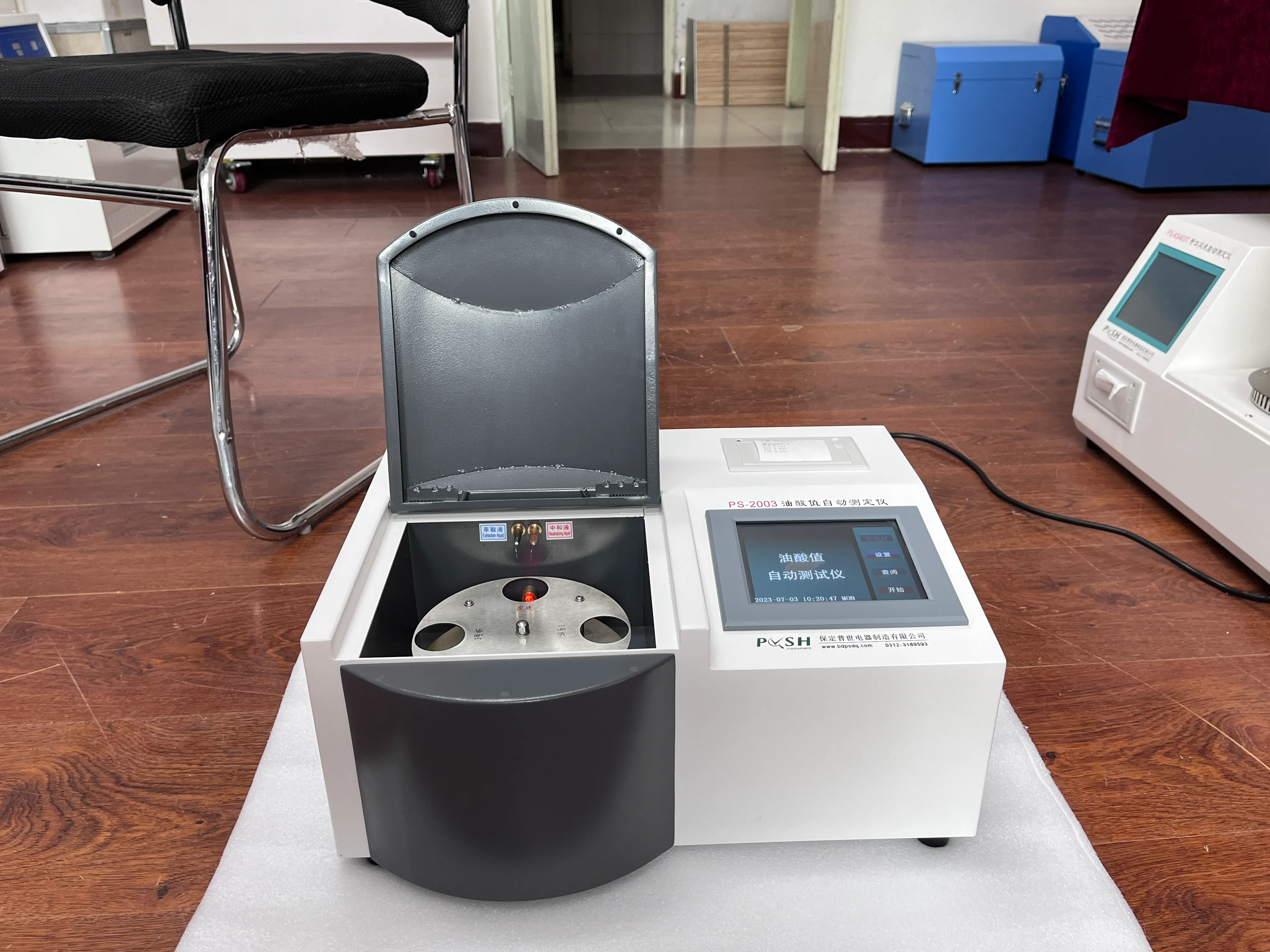
One of the major strengths of the closed cup test is its authenticity in real-world applications. The covered test environment reflects the conditions found within fuel tanks, storage containers, and delivery systems. This realism makes the data derived from the closed cup test highly relevant for predicting how substances behave under actual storage and usage conditions. By closely resembling the scenarios industries face daily, this test helps develop robust safety protocols to mitigate the risks of combustion and explosion.
flash point closed cup test
The closed cup method's expertise is further reinforced through the sophisticated technologies employed during testing. Advanced instruments used in modern laboratories facilitate more precise readings by mitigating external variables that could otherwise affect the outcome. These technological advancements have not only enhanced the accuracy of the results but also increased the speed at which they can be obtained. Consequently, companies can maintain a more responsive and proactive approach to safety management.
Trustworthiness in the results obtained through the flash point closed cup test is of utmost importance, especially when dealing with substances that pose significant hazards. Industries instill confidence in their processes and products by ensuring that all test procedures are conducted following stringent quality assurance protocols. Certified laboratories committed to maintaining these high standards provide industries the assurance needed to make informed decisions regarding handling and storage practices.
Real-world experiences further emphasize the value of the closed cup method. Industry reports have documented numerous instances where the information gleaned from this test was pivotal in redesigning packaging and implementing safer transportation methods. Such tangible applications underscore the test's impact in preventing industrial accidents and safeguarding human lives. Companies leveraging these insights enhance their reputation, showcasing their commitment to safety and innovation.
In conclusion, the flash point closed cup test plays an indispensable role in today's industrial landscape. Its focus on Experience, Expertise, Authoritativeness, and Trustworthiness makes it a vital resource for chemical safety management. Industries that proactively adopt this testing method benefit from enhanced compliance with safety standards, reduced risk of accidents, and improved overall safety protocols. As technology continues to evolve, so too will the precision and applicability of the closed cup test, ensuring its relevance for future safety challenges.