Flash point testing machines play a crucial role in ensuring safety, quality, and compliance across various industries, particularly where flammable materials are involved. Understanding their operation, significance, and selection can extensively benefit laboratories and industrial applications.
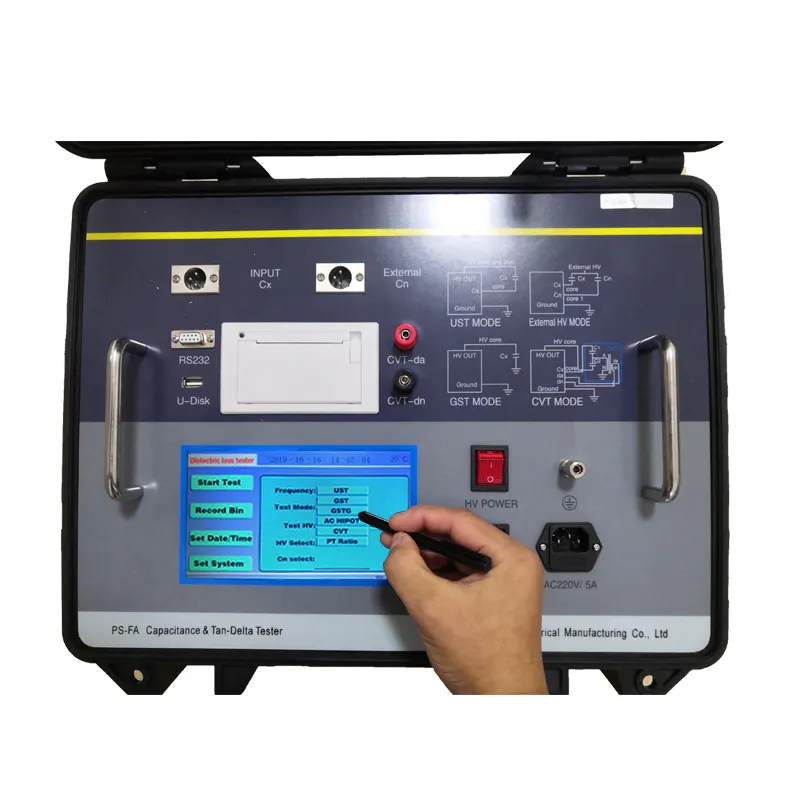
A flash point testing machine determines the lowest temperature at which a liquid's vapors ignite when exposed to an ignition source. This measurement is essential for handling, storing, and transporting flammable liquids safely. It indicates the temperature threshold at which materials become hazardous, helping industries comply with safety regulations and standards like ASTM and ISO.
Industries such as petrochemicals, pharmaceuticals, paints, and coatings heavily rely on flash point testing to classify materials and assess risk. For instance, in petrochemical companies, understanding the flash point of crude oil helps prevent fires or explosions during processing and transportation. Similarly, in the paint industry, it aids in formulating safer products and determining storage and handling protocols.
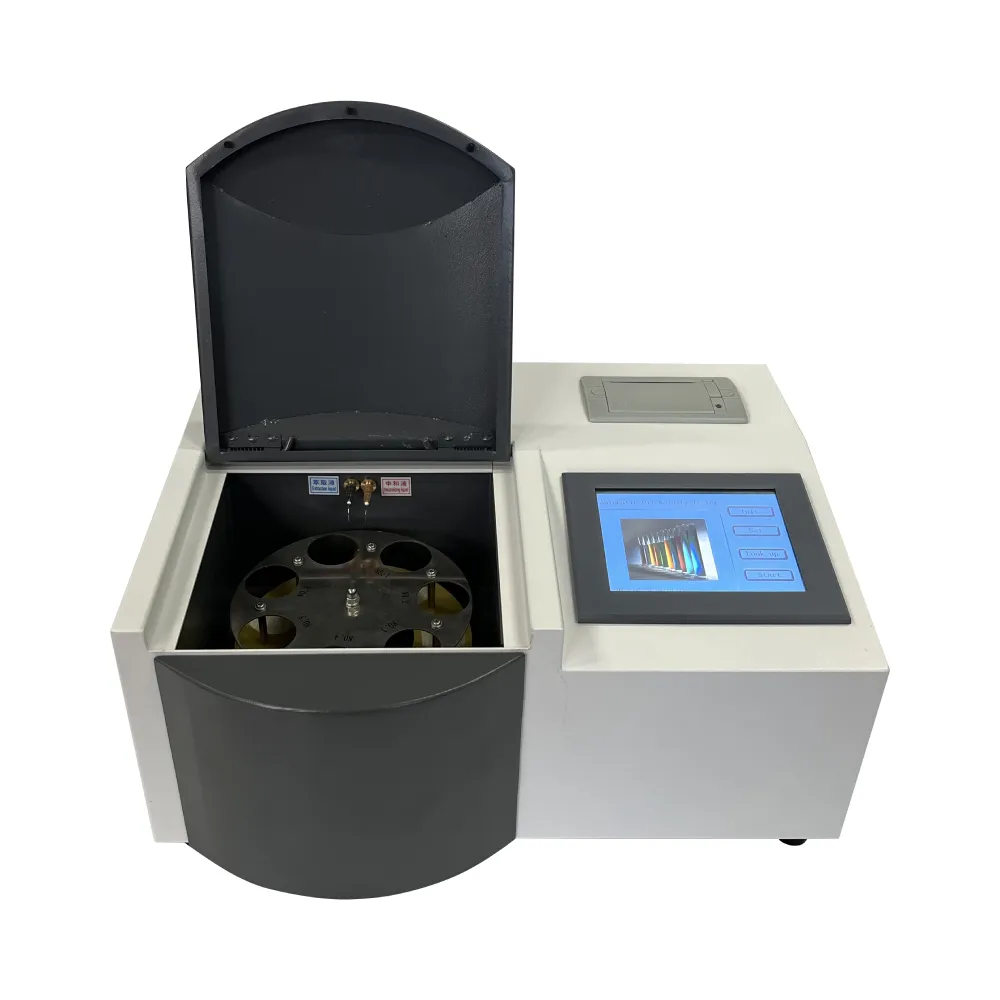
Choosing the right flash point testing machine involves considering various factors to ensure precision and reliability. The key aspects include the range of temperature requirements, sample size, regulatory compliance, and ease of operation. Machines can generally be categorized into open-cup and closed-cup testers, each suited to specific application needs.
Open-cup testers, like the Cleveland Open Cup, measure the flash point under atmospheric pressure, exposing the liquid to air. They are widely used for materials with high flash points,
such as lubricating oils. Closed-cup testers, including Pensky-Martens and Tag Closed Cup, offer a more controlled environment by sealing the sample, thus providing lower flash point measurements suitable for volatile substances.
Investing in a flash point testing machine demands attention to technological advancements and features that enhance accuracy and efficiency. Modern devices are equipped with digital controls, automation, and data logging facilities, enabling precise readings and seamless integration into quality control systems. Additionally, some models offer multi-sample testing capabilities, optimizing throughput in high-volume laboratories.
flash point testing machine
Industry professionals emphasize hands-on training and comprehensive understanding of the equipment. Proficiency in using flash point testers not only ensures accurate results but also minimizes risks associated with flammable materials. Many manufacturers offer training workshops and practical demonstrations to familiarize operators with the equipment's nuances and maintenance requirements.
Regular calibration and maintenance are vital to sustain the machine's performance and reliability. Users should adhere to the manufacturer’s guidelines and establish a routine for cleaning, part replacement, and performance verification. This practice significantly reduces downtime and extends the equipment's lifespan, ensuring uninterrupted testing operations.
Accurate flash point testing reinforces trust in safety protocols and product quality, which is crucial for building customer confidence and maintaining a competitive edge. Compliance with international safety standards underscores a company's dedication to excellence and responsibility, particularly in sectors sensitive to hazardous material risks.
When selecting a flash point testing machine, consulting with industry experts and peers can provide valuable insights. Independent reviews, case studies, and product comparisons often highlight user experiences, revealing practical advantages and potential limitations of different models. Engaging with professional networks and attending industry conferences can further enrich knowledge and decision-making.
In conclusion, a flash point testing machine is indispensable for industries managing flammable liquids. It enables compliance with safety standards, optimizes material handling, and helps prevent accidents. By selecting the appropriate machinery and fostering expertise in its use, organizations enhance their operational safety, product quality, and regulatory adherence, reinforcing their reputation as industry leaders.