Impulse tests on transformers play a crucial role in the manufacturing process, ensuring that these devices meet the stringent standards required for safe and efficient operation. The primary objective of impulse testing is to simulate overvoltage conditions, such as lightning strikes or switching surges, that transformers may encounter during their lifetime. By doing so, manufacturers can verify the dielectric strength and reliability of the transformer insulation system.

Experience plays a significant role in conducting effective impulse tests. Engineers and technicians who perform these tests have extensive hands-on experience with high-voltage testing equipment and are adept at setting up test scenarios that mimic real-world conditions. This expertise is essential to accurately assess transformer performance and identify potential vulnerabilities. For instance, seasoned professionals can quickly identify anomalies in waveforms, such as overshoots or oscillations, that may indicate insulation issues.
Expertise in designing impulse tests is also critical for ensuring valid results. Professionals must be well-versed in international testing standards, such as IEEE C57.98 and IEC 60076-3, which dictate the specific procedures and parameters for conducting impulse tests. This knowledge ensures that tests are not only rigorous but also standardized, allowing manufacturers to confidently certify their products. Additionally, experts understand the nuances of different transformer types and can tailor tests to address the particular characteristics and potential weaknesses of each design, whether it be power transformers, distribution transformers, or specialty transformers for industrial applications.
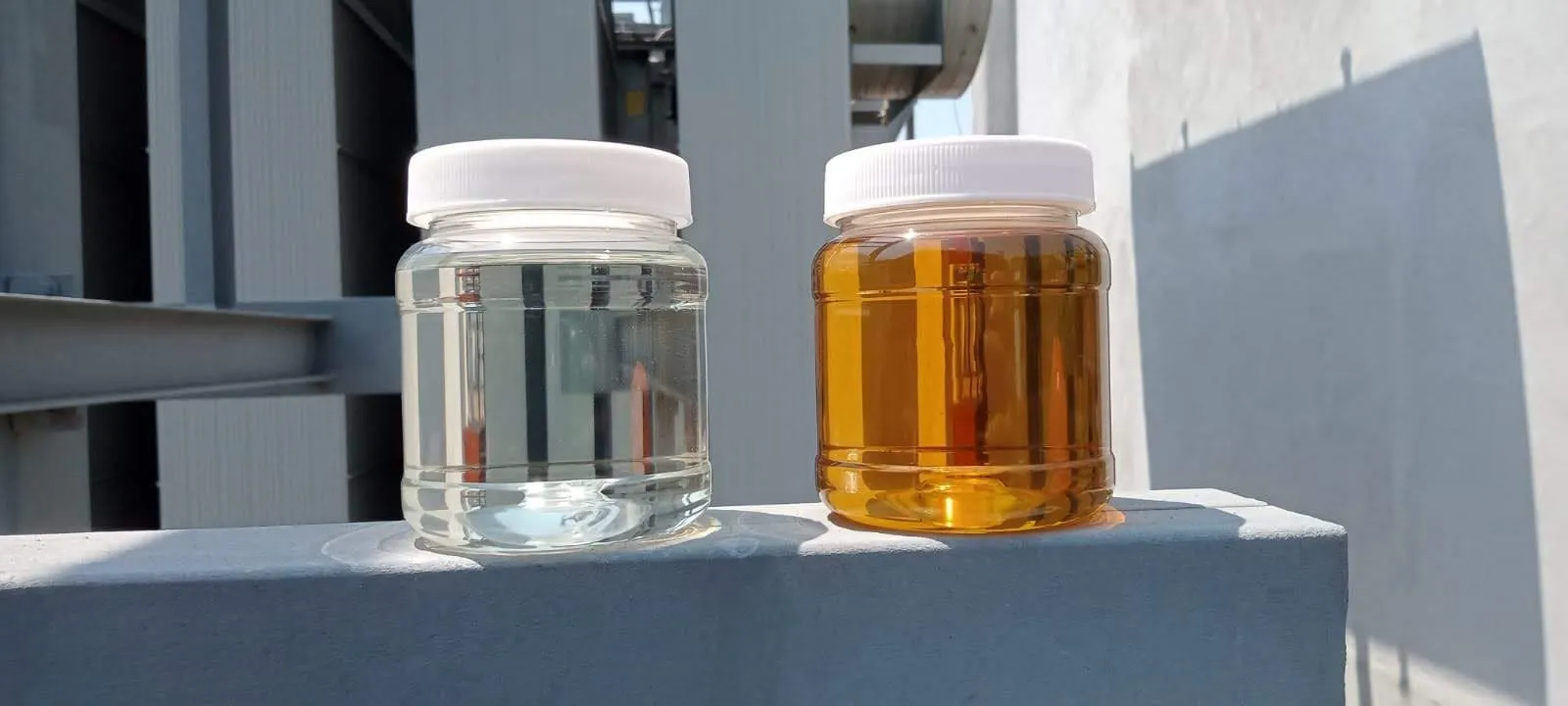
Authoritativeness is maintained through meticulous documentation and analysis of test results. Each impulse test generates a wealth of data, including voltage waveforms, time-to-peak measurements, and dielectric breakdown occurrences. Engineers must analyze this data with precision, drawing upon their deep understanding of physics and electrical engineering principles. Once the data is interpreted, comprehensive reports are generated, providing a detailed record of the test conditions, methodologies, and outcomes. This documentation is vital for traceability and serves as a testament to the product's quality assurance process, reinforcing the manufacturer's authority in the industry.
impulse tests are performed on transformers
Trustworthiness in impulse testing is established through both the rigorous execution of tests and the transparency of the entire process. Manufacturers often invite independent third-party testing agencies to validate their findings, offering an unbiased perspective on the results. This third-party validation adds a layer of credibility, assuring clients and stakeholders that the transformer has been thoroughly evaluated and meets all safety and performance standards. Furthermore, companies that adhere to a consistent schedule of impulse testing, including periodic re-evaluation of their products in the field, demonstrate a commitment to maintaining high standards throughout the transformer's operational life.
Impulse testing also acts as a predictive maintenance tool, helping manufacturers anticipate potential failure points before they manifest. By analyzing test data trends over time, engineers can refine transformer designs, materials, and manufacturing processes to enhance durability and reliability. This proactive approach not only mitigates the risk of future transformer failures but also optimizes the cost-efficiency of the entire power distribution network.
In summary,
impulse tests are indispensable for ensuring the reliability and longevity of transformers. The combination of expert knowledge, authoritative testing practices, and transparent, trustworthy processes ensures that transformers can withstand the challenges of real-world applications. Through experience and expertise, manufacturers can tailor impulse tests to meet the stringent standards of the industry, providing products that are both innovative and resilient. This holistic approach to transformer testing not only safeguards the equipment but also enhances the stability and safety of electrical systems globally.