Insulation continuity tests are an integral part of maintaining electrical systems, ensuring safety and reliability in residential, commercial, and industrial settings. These tests are crucial for preventing potential electrical hazards and ensuring that the insulation material maintains its integrity over time, which is why understanding and performing these tests effectively is vital for electricians and engineers alike.
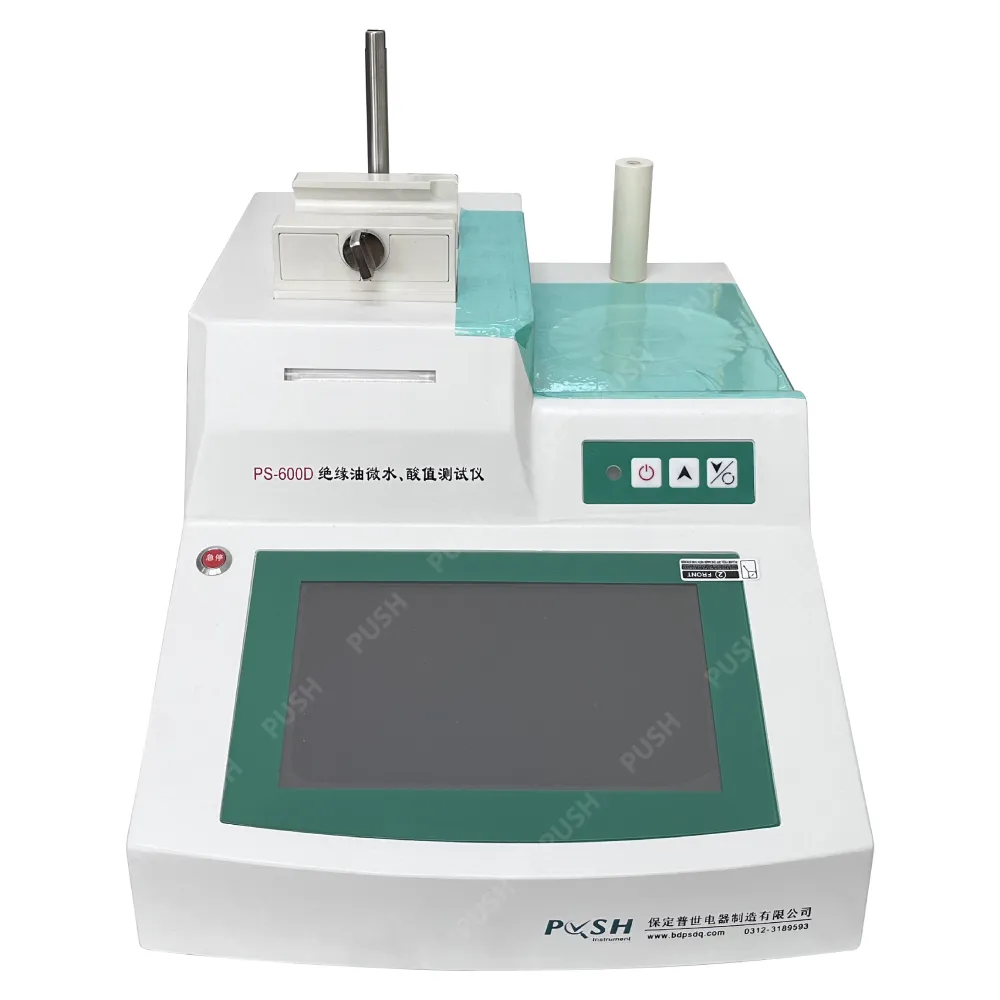
Experience shows that insulation failures can lead to severe consequences such as electrical shocks, fires,
or even equipment failure. Conducting regular insulation continuity tests is an effective way to mitigate these risks. The process typically involves measuring the resistance offered by insulating material to the flow of electrical current. This measurement is crucial as it indicates how well the insulation can prevent the undesired flow of electricity, thereby ensuring that all electrical systems are running safely.
Expertise in conducting these tests involves using specific instruments, such as a megohmmeter, which helps in accurately measuring insulation resistance. A professional's ability to interpret these measurements is essential, as they must determine if the insulation meets safety standards or if any repairs are needed. Moreover, understanding the environmental factors that can affect insulation, such as temperature and humidity, is crucial in obtaining accurate results. For instance, high humidity levels can reduce insulation resistance readings, leading to false conclusions about its integrity.

Authoritativeness is established through adherence to industry standards and regulations, such as those outlined by the International Electrotechnical Commission (IEC) and the Institute of Electrical and Electronics Engineers (IEEE). Following these standards not only ensures compliance but also enhances the reliability and trustworthiness of the test results.
insulation continuity test
Trustworthiness in insulation continuity testing is further enhanced by the use of certified, calibrated testing equipment, and by ensuring that the personnel conducting the tests are well-trained and experienced. Documenting test procedures and results systematically is also necessary to maintain transparency and accountability. This includes recording baseline values, date and time of testing, environmental conditions, and identification of the tested equipment.
Insulation continuity tests are not just about compliance; they’re fundamental in extending the lifespan of electrical installations and reducing maintenance costs. By proactively identifying potential issues, these tests can help avoid costly downtime and repairs. For those responsible for maintaining electrical systems, implementing a routine testing schedule can significantly enhance both safety and performance.
New advancements in testing technology have introduced more sophisticated instruments that provide quicker and more precise readings. This innovation has led to greater accuracy in diagnosing insulation health, thereby providing more reliable data to base maintenance decisions on. Digital platforms now offer enhanced data management, allowing for better tracking of test results over the lifecycle of equipment, leading to improved decision-making processes in asset management.
In conclusion, insulation continuity tests play an indispensable role in the safety and efficiency of electrical systems. By leveraging experience, expertise, and a commitment to industry standards, professionals can conduct these tests with authority and trustworthiness, ensuring the highest levels of safety and operational efficiency. Continuous learning and adaptation to new technologies further aid in enhancing the effectiveness of these essential tests, ultimately contributing to more secure and reliable electrical infrastructure.