Insulation testers, commonly used by electricians and engineers, are essential tools for assessing the integrity of electrical insulation. These devices not only prevent potential system failures but also ensure safety in environments where electrical reliability is critical. Selecting the right insulation tester involves understanding their functional capacities, applications, and how they contribute to the overall safety and efficiency of electrical systems.
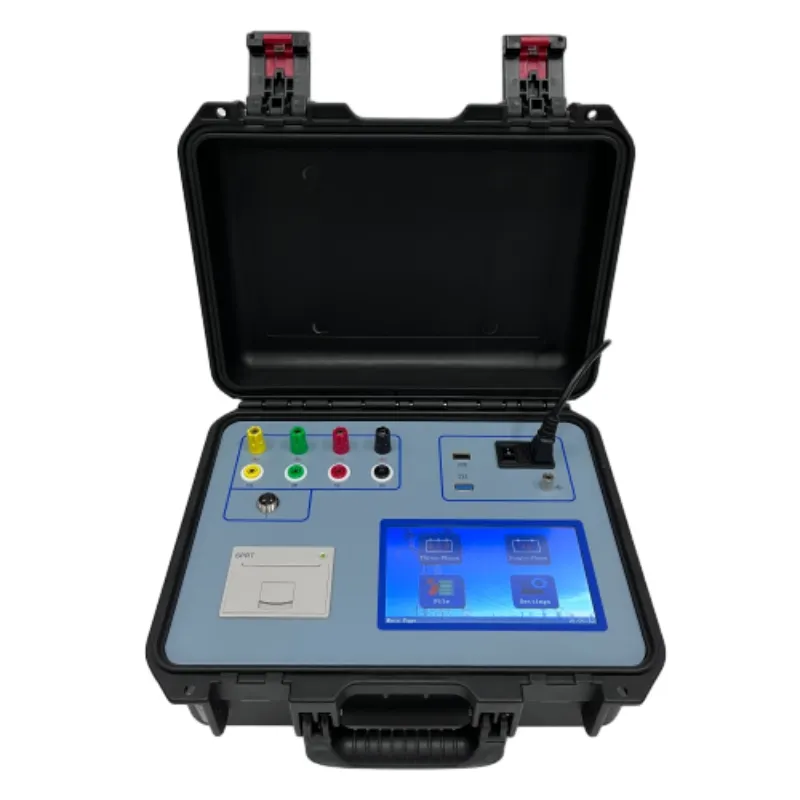
An insulation tester's primary function is to apply a voltage to a device under test and measure how well the insulation resists the current flow, thus determining the quality and reliability of the insulation material. This measurement helps in identifying potential points of failure that could lead to hazardous conditions, especially in high-voltage environments. Understanding this core functionality is vital for anyone responsible for maintaining electrical systems, as it directly influences operational safety and equipment longevity.
In industries such as manufacturing, aerospace, and telecommunications, insulation testers play a crucial role in routine maintenance schedules. Their use spans from testing domestic wiring systems to complex industrial machines, ensuring that all electrical components perform optimally without risk of short circuits or other malfunctions. Expert technicians stress that the regular use of insulation testers can significantly reduce downtime caused by unexpected equipment failures, directly impacting productivity and operational costs.
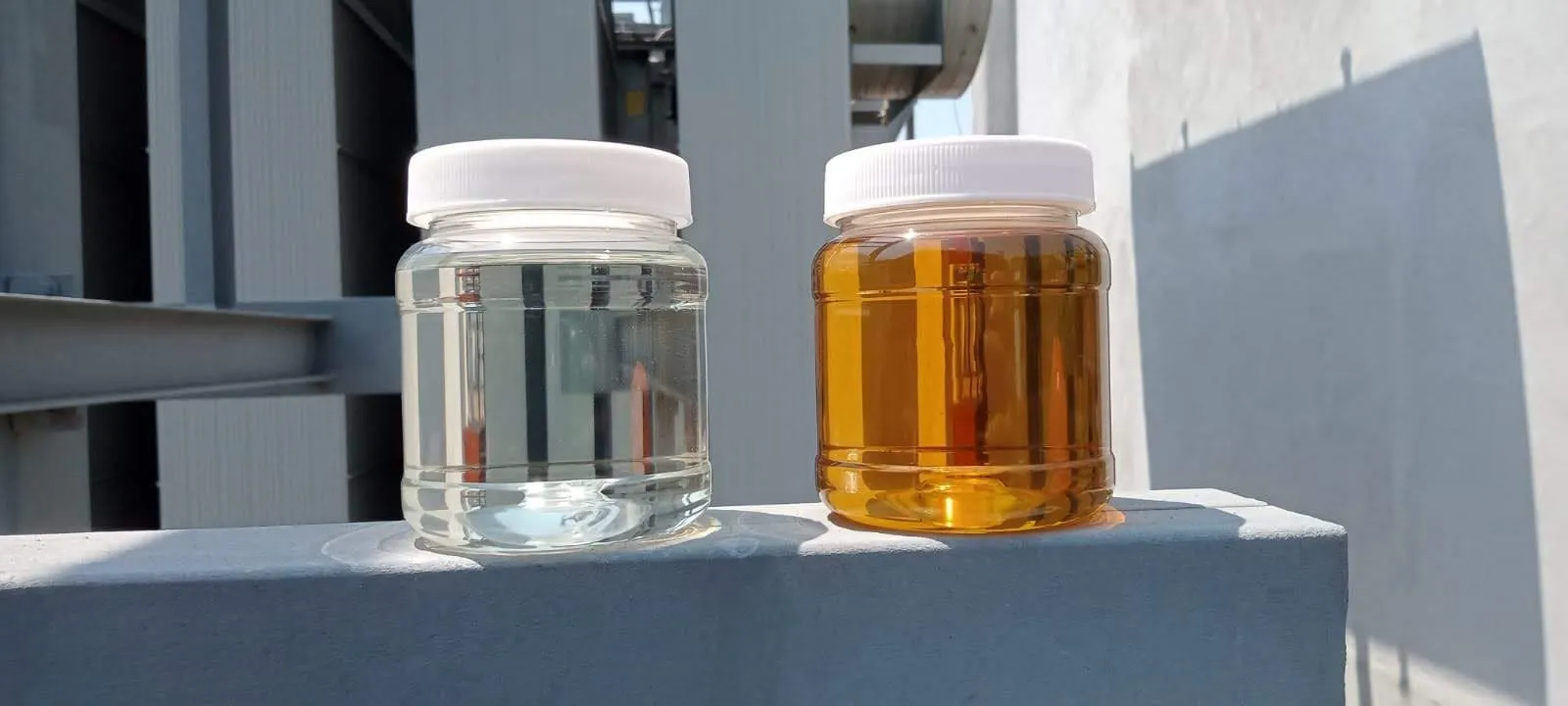
One must consider several features when selecting an insulation tester. Foremost is the voltage range—the tester must match the application’s requirements. A tester with a wide voltage range offers flexibility across different testing scenarios, making it suitable for both low-voltage residential applications and high-voltage industrial systems. Additionally, the durability and reliability of an insulation tester are factors that directly contribute to its trustworthiness as a testing instrument in critical environments.
insulation tester
Modern insulation testers often include features such as digital displays, rugged construction for fieldwork, and rechargeable batteries for sustained use. Advances in technology have also integrated data storage capabilities, allowing technicians to store test results for future reference and trend analysis. Such features elevate an insulation tester's usefulness from mere measurement to a comprehensive diagnostic tool, leveraging data-driven insights for better maintenance strategies.
Manufacturers stand behind their insulation testers with certifications that attest to their accuracy and safety compliance. Certifications from recognized international standards bodies, such as IEC or ASTM, enhance an insulation tester’s credibility. These endorsements serve as a testament to the product’s quality, adherence to safety standards, and its potential effectiveness in a professional setting.
When utilized correctly, insulation testers are instrumental in enforcing electrical safety protocols. They empower professionals with precise data essential for maintaining robust electrical systems. By mitigating risks associated with faulty insulation, businesses not only safeguard their personnel but also protect expensive equipment from damage, underscoring the importance of these devices in any comprehensive electrical maintenance toolkit.
For an experienced electrician or engineer, an insulation tester is a tool of expertise that upholds operational standards and communicates a commitment to safety and reliability. It acts as both an identifier of existing issues and a preventive measure against future electrical failures. The investment in a quality insulation tester thus extends beyond simple compliance; it becomes a cornerstone of professional practice that secures workplace safety and preserves system integrity.