As a cornerstone tool in the electrical industry, an insulation tester is indispensable for ensuring the safety and efficiency of electrical installations. From seasoned electricians to DIY enthusiasts, understanding the proper use of an insulation tester is crucial for maintaining high standards of electrical wellness. This article delves deep into the practical experiences, professional insights, authoritative advice, and the fundamental trustworthiness associated with the use of insulation testers.
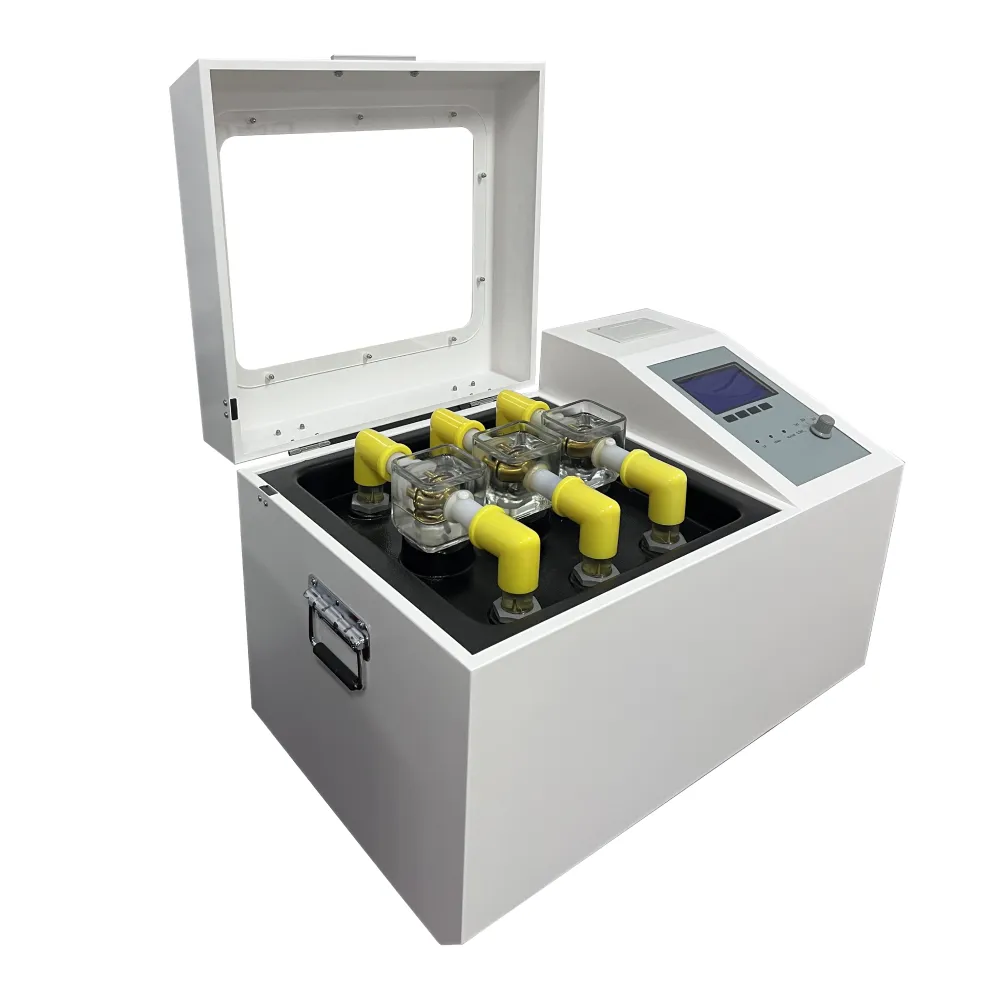
Electricians often tout the insulation tester as the 'superhero' of their toolkit. Imagine embarking on a task without one; the risks far outweigh any potential time saved. An insulation tester's primary function is to measure the resistance of electrical insulation, providing irreplaceable insights into its condition. Experience has shown that compromised insulation can lead to unscheduled outages, equipment failure, or even catastrophic fires. Therefore, using an insulation tester is a non-negotiable method for identifying deterioration in insulation before it leads to disaster.
In terms of expertise, operating an insulation tester demands a solid understanding of its settings and functionalities. Professionals recommend starting with the device's manual because, like all sophisticated electronics, each model can differ markedly. Set the tester to the appropriate voltage level for the system being tested, typically 250V, 500V, or 1000V, unless specified otherwise by local regulations or equipment guidelines. To perform a test, connect the tester's leads to the conductor whose insulation you're measuring. A high resistance value, generally above one mega-ohm, indicates good insulation, whereas lower readings can signal potential issues.

From an authoritative standpoint, regular insulation resistance testing aligns with international standards such as the IEEE Std 43-2013 and IEC/EN 61557-2, underlining its importance in preventive maintenance schedules. Organizations like the Institute of Electrical and Electronics Engineers advocate periodic insulation testing as part of best operational practices. While it's easy to overlook these tests in a busy schedule, adherence to such standards not only complies with industry regulations but also reduces long-term maintenance costs by preventing unexpected equipment failures.
The trustworthiness of insulation testers hinges significantly on their calibration and maintenance. A frequent mistake is to neglect the recalibration of these devices. Precision instruments can drift over time, leading to inaccurate readings. Regular recalibration ensures that the device remains reliable, sustaining its reputation as a trustworthy piece of equipment. Users should keep service records and calibration certificates up-to-date—an often understated practice that speaks to professionalism and diligence.
insulation tester use
Visiting the realm of product features, modern insulation testers often come equipped with digital displays, automated test sequences, and memory storage capabilities for results logging. These features enhance the user experience by reducing human error and allowing for data analysis over time, which can be invaluable for identifying trends and predicting potential failures. Innovative models also offer Bluetooth connectivity, enabling integration with software platforms for advanced data management.
A practical tip for users seeking trust in their test measurements is to perform tests under consistent environmental conditions. Temperature and humidity can affect insulation values, and accounting for these variables can help in obtaining consistent, reliable data. Conducting tests in environments that mirror normal operating conditions yields the most useful results.
Ultimately, an insulation tester is not just a diagnostic tool but an investment in safety and efficiency. Its use demonstrates a commitment to electrical integrity, preserving equipment life, and ensuring the well-being of individuals relying on safe and functional electrical systems. With conscientious handling and regular usage, an insulation tester stands as a testament to quality maintenance and forethought in the electrical industry.
Embrace this tool as an emblem of expertise and reliability—qualities that resonate well in an industry that leaves no room for compromise on safety and efficiency.