The realm of fluid mechanics is essential in industries where fluids play a critical role in operational processes. At the heart of understanding these fluid dynamics lies the kinematic viscosity tester, a fundamental instrument that ensures precision, efficiency, and reliability. This device is crucial for industries ranging from automotive to oil and gas, where it measures the fluid's resistance to flow and shear under gravitational force.
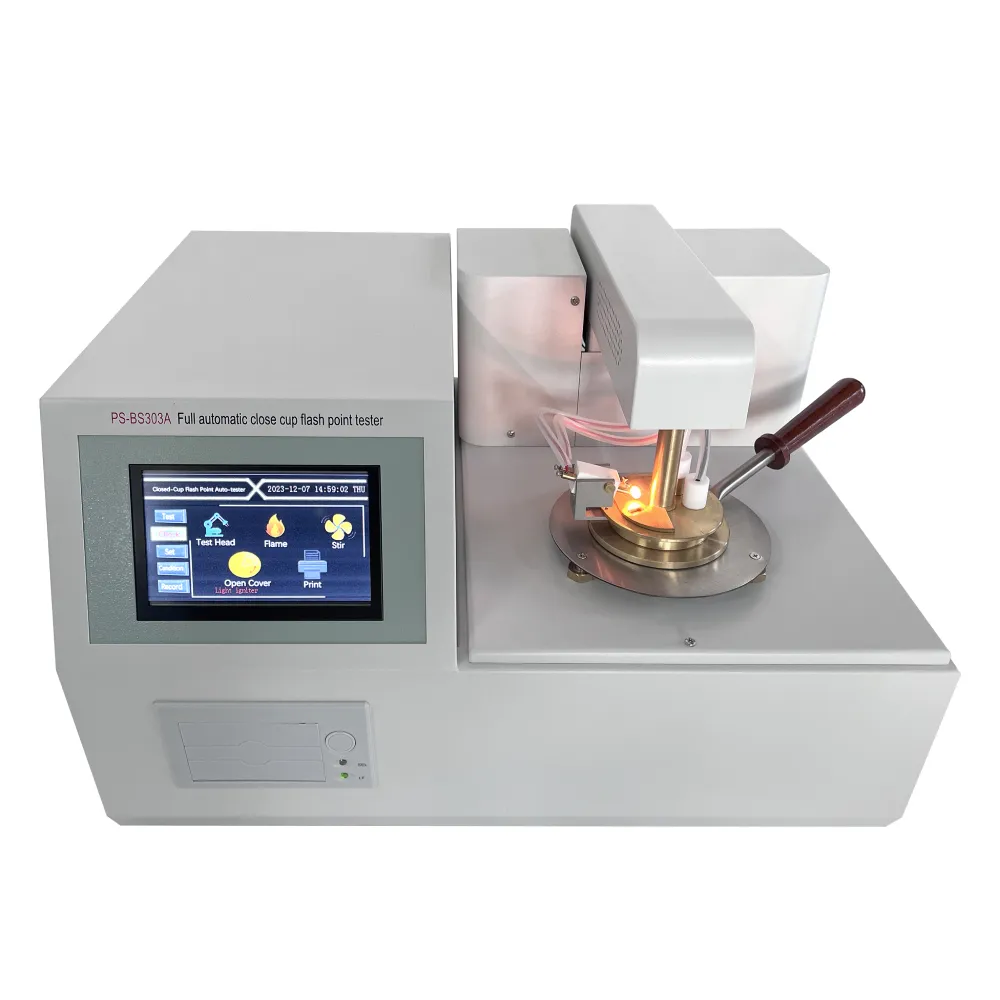
A kinematic viscosity tester provides invaluable insights into fluid properties, which are fundamental to optimizing machinery function and longevity. Industrial experts who rely on these devices understand that fluid viscosity impacts energy consumption, wear and tear of mechanical parts, and ultimately, the overall efficiency of a system. Therefore,
ensuring the accurate measurement of kinematic viscosity is paramount.
Utilizing a kinematic viscosity tester involves precision and expertise. The instrument works by analyzing the time it takes for a fluid sample to flow through a capillary tube under the influence of gravity. The measurement process is influenced by temperature, requiring precise control and calibration to obtain accurate results. Experts in the field emphasize the importance of preparing a clean and debris-free environment for taking measurements, as impurities can significantly alter the results.
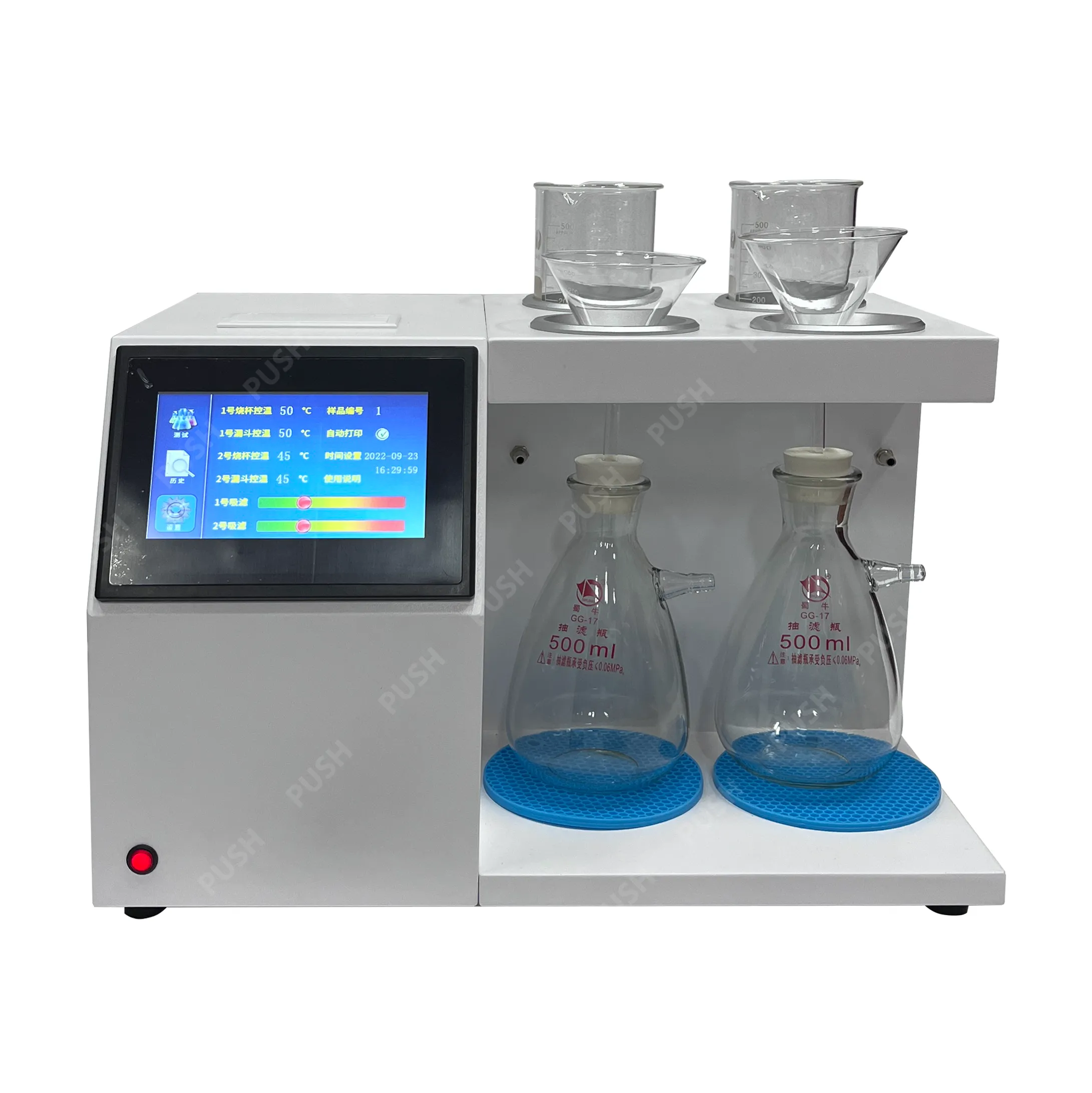
Industrial-grade kinematic viscosity testers are designed to withstand the demands of rigorous usage while providing results that meet and exceed industry standards. These devices are trusted by engineers and technicians alike for their durability and the reliability of their measurements. Recognized brands in the industry manufacture testers that incorporate advanced technology, such as digital interfaces that enhance precision and user-friendliness, making them essential in settings that demand accuracy and efficiency.
kinematic viscosity tester
Authoritative sources within the industry argue that investing in a high-quality kinematic viscosity tester substantially reduces mechanical failures. By ensuring that fluids maintain the correct viscosity, machine operators can prevent excessive wear and reduce energy consumption, leading to more sustainable operations. Moreover, accurate viscosity measurements assist in maintaining compliance with regulatory standards, avoiding costly fines and potential operational shutdowns.
As technology advances, kinematic viscosity testers are becoming increasingly sophisticated. Modern testers are often equipped with automation features, allowing for seamless integration into larger industrial systems. These advancements reduce the potential for human error, streamline operations, and enable continuous monitoring, which is particularly beneficial in industries where fluid dynamics can change rapidly due to external conditions or operational demands.
The innovative designs and features of contemporary kinematic viscosity testers reflect their critical role in maintaining operational excellence. Development teams continuously update these instruments to improve accuracy and facilitate easier user interfaces, which in turn fosters trust among users. A robust support system provided by manufacturers, including regular updates and customer service, further enhances the trustworthiness of these devices.
In conclusion, the kinematic viscosity tester is not just a tool but an investment in the future of efficient and reliable industrial operations. Experts and industry leaders reiterate its importance, as accurate fluid dynamics measurements can significantly impact energy usage, machinery lifespan, and overall system efficiency. As industries continue to evolve, the role of precise instruments like the kinematic viscosity tester becomes even more essential, ensuring that operations run smoothly and sustainably.