Load testing transformers represents a critical phase in ensuring the reliability and efficiency of these complex devices. Transformers, often referred to as the backbone of electrical systems, play a vital role in energy distribution. For companies producing transformers, understanding the load test process can significantly enhance product trustworthiness and authority in the market.
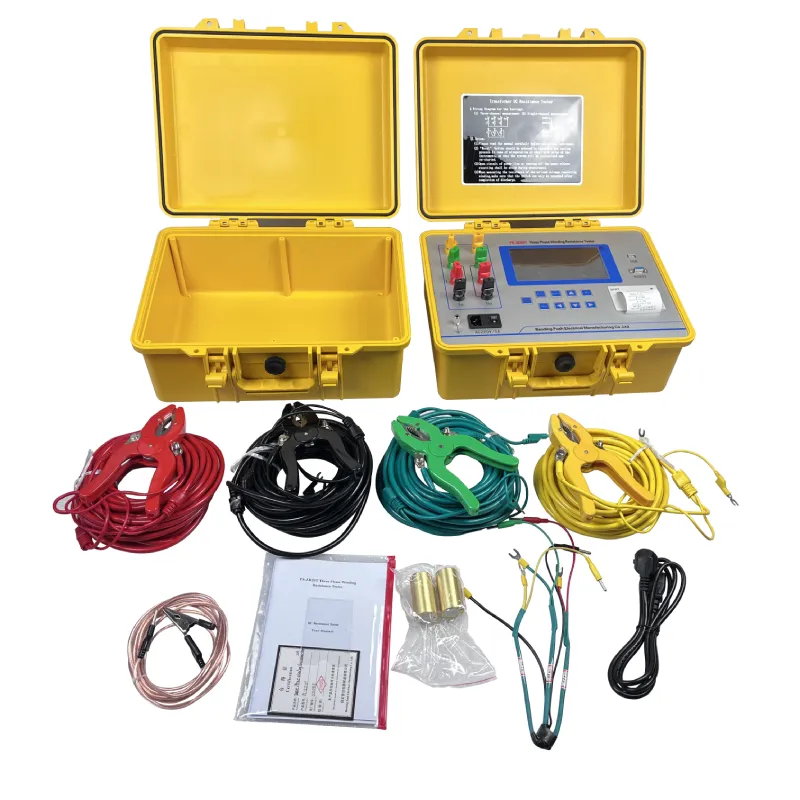
Experience reveals that load tests are indispensable for evaluating a transformer's performance under specific conditions. Industry professionals consistently emphasize the necessity of a methodical approach to conducting these tests. A seasoned engineer might recount the first time they took part in a load test, highlighting the elaborate setup, the myriad of measurements involved, and the invaluable insights gained about the transformer's operational integrity. This hands-on experience demonstrates the essence of Experience (the first of the E-E-A-T criteria), rooting theoretical knowledge in practical application.
From a professional standpoint, transformers undergo rigorous load testing to establish their capacity to handle expected and occasionally unexpected electrical demands. These evaluations ascertain whether a transformer can sustain peak loads without compromising efficiency or safety. The methodology behind these tests involves applying a rated or sometimes higher current while monitoring how the transformer behaves under load. Observations include checking the temperature rise, noise levels, vibration, and electrical characteristics. Expertise, in this realm, demands that engineers are not just familiar with the testing protocol but also understand the nuances that might affect a transformer's performance such as ambient temperature and cooling effectiveness.
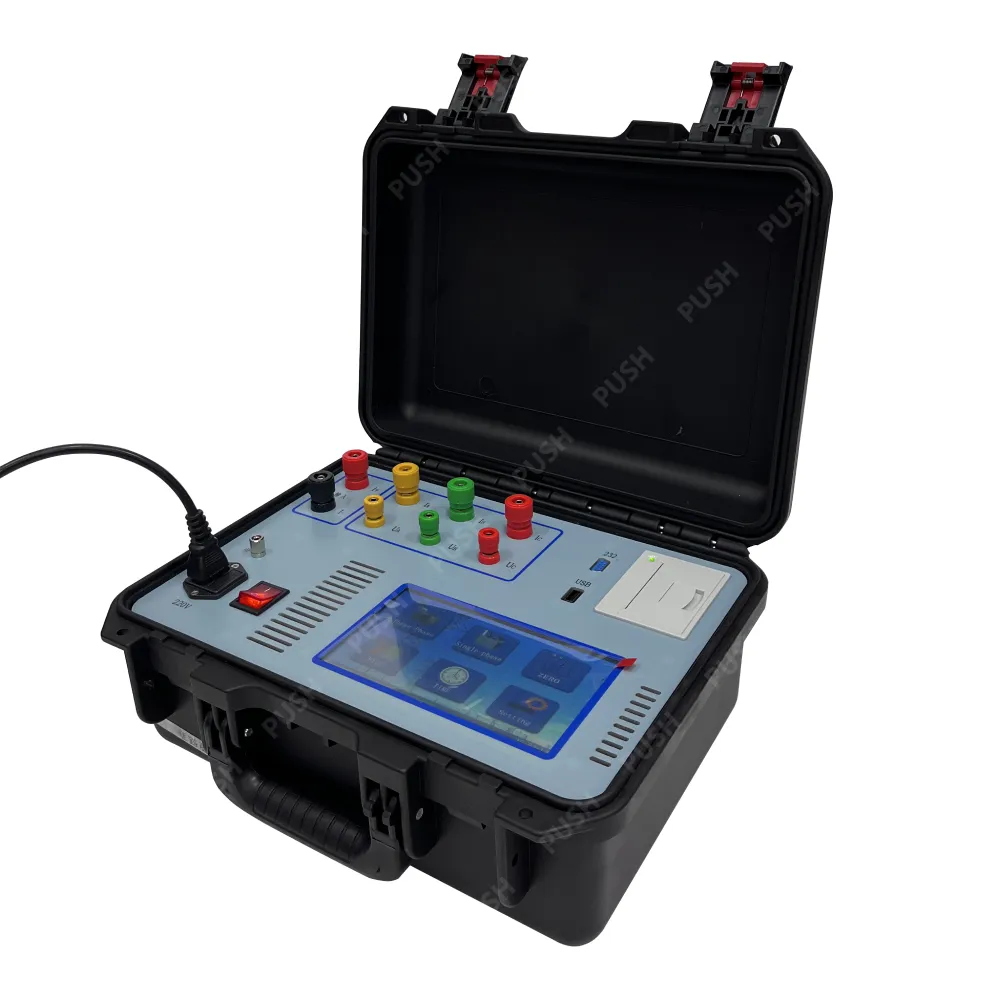
Experts advise utilizing a mix of static and dynamic tests to gather comprehensive data. Static tests provide a snapshot of the transformer's capability under stable conditions, while dynamic tests simulate real-world fluctuations. This approach ensures the transformer is robust enough to handle variable loads over time. The acquisition of detailed performance metrics broadens a firm's Authoritativeness, establishing it as a knowledgeable entity in transformer technology.
load test in transformer
Trustworthiness is enhanced when manufacturers are transparent about their load testing processes and outcomes. Customers and stakeholders need assurance that the transformers will perform flawlessly in their operational life. Companies that produce and publish test results, preferably vetted by third-party testers for impartiality, bolster their credibility significantly. Compliance with international standards such as IEC 60076 (for power transformers) further attests to a product's reliability and safety, cementing trust within the industry.
Transformers form a core part of infrastructural energy solutions, and their failure can lead to significant downtime and resource loss. Therefore, having a proven, documented practice for load testing elevates a company's profile. Market leaders in transformer manufacturing continuously invest in cutting-edge testing facilities and highly skilled personnel. This investment reflects a commitment not only to product excellence but also to customer safety and satisfaction, linking back to all elements of the E-E-A-T framework.
Load testing, invariably, stands as a testament to a company's dedication to delivering robust and dependable products. It involves not just technical expertise but also a strategic commitment to transparency and quality assurance. As transformers continue to evolve in complexity, the load test remains a fundamental aspect, ensuring these devices meet the exacting demands of modern energy networks. The firms that excel in this domain will inevitably command greater respect and trust from their clientele, securing their position as authoritative leaders in the electrical industry.