Measuring the winding resistance of transformers, motors, and other inductive devices plays a pivotal role in ensuring the optimal performance and longevity of electrical equipment. This technical process, often overlooked, carries more significance than it might first appear, powering not only machinery but by extension, entire industries and infrastructure.
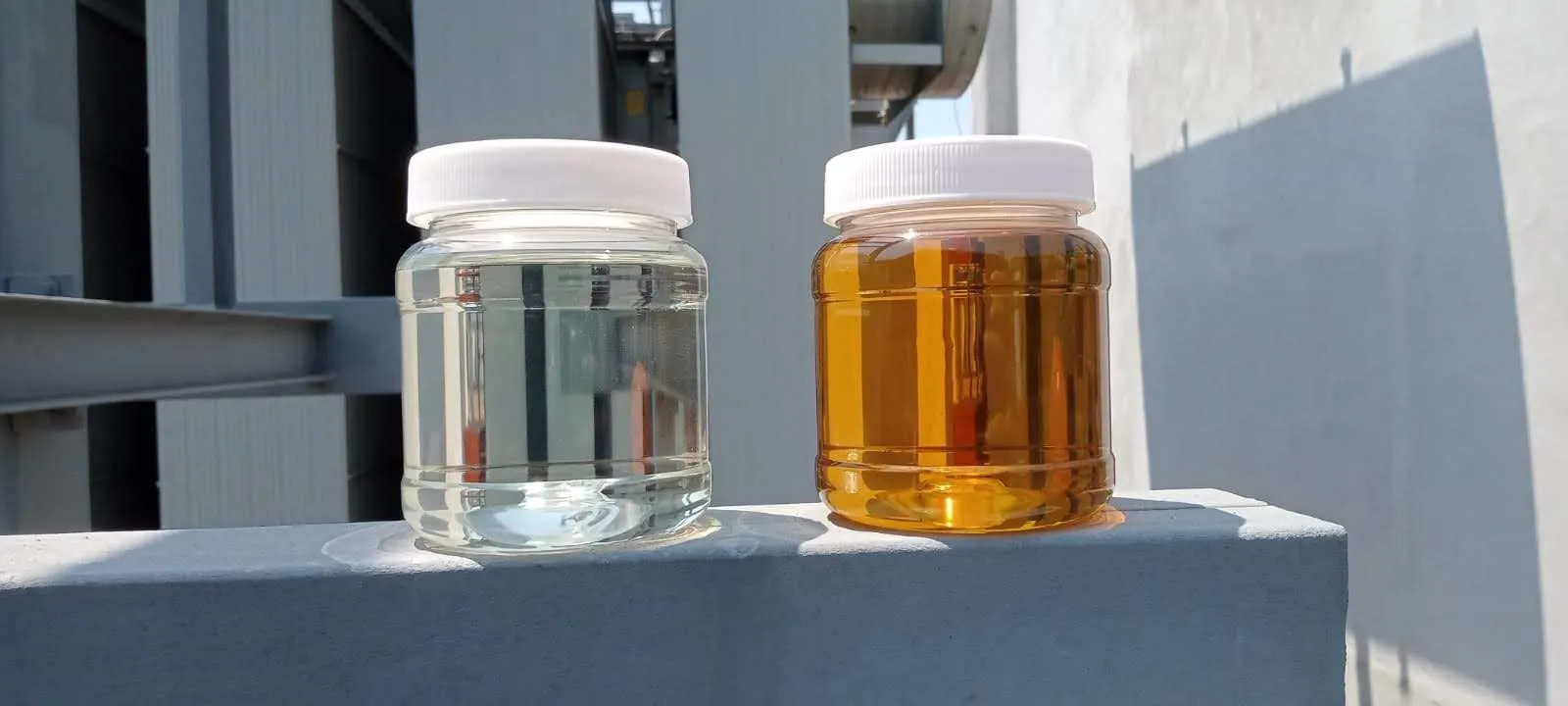
Winding resistance measurement is a critical diagnostic tool used primarily in maintenance programs for transformers and electric motors. When performed accurately, these measurements can reveal the health status of the winding and predict potential issues before they become catastrophic failures. This simple yet powerful procedure is intertwined with the broader realm of electrical diagnostics and predictive maintenance strategies.
Firstly,
understanding the intricacies of winding resistance involves a clear grasp of both the theory and practical application. At the heart of this measurement process lies the objective to detect variations in the resistance, which may indicate changes in the winding's condition. Such changes can result from a variety of factors including temperature shifts, mechanical damage, or insulation failures. An increase in winding resistance typically suggests poor electrical contact, corrosion, or the onset of winding damage.
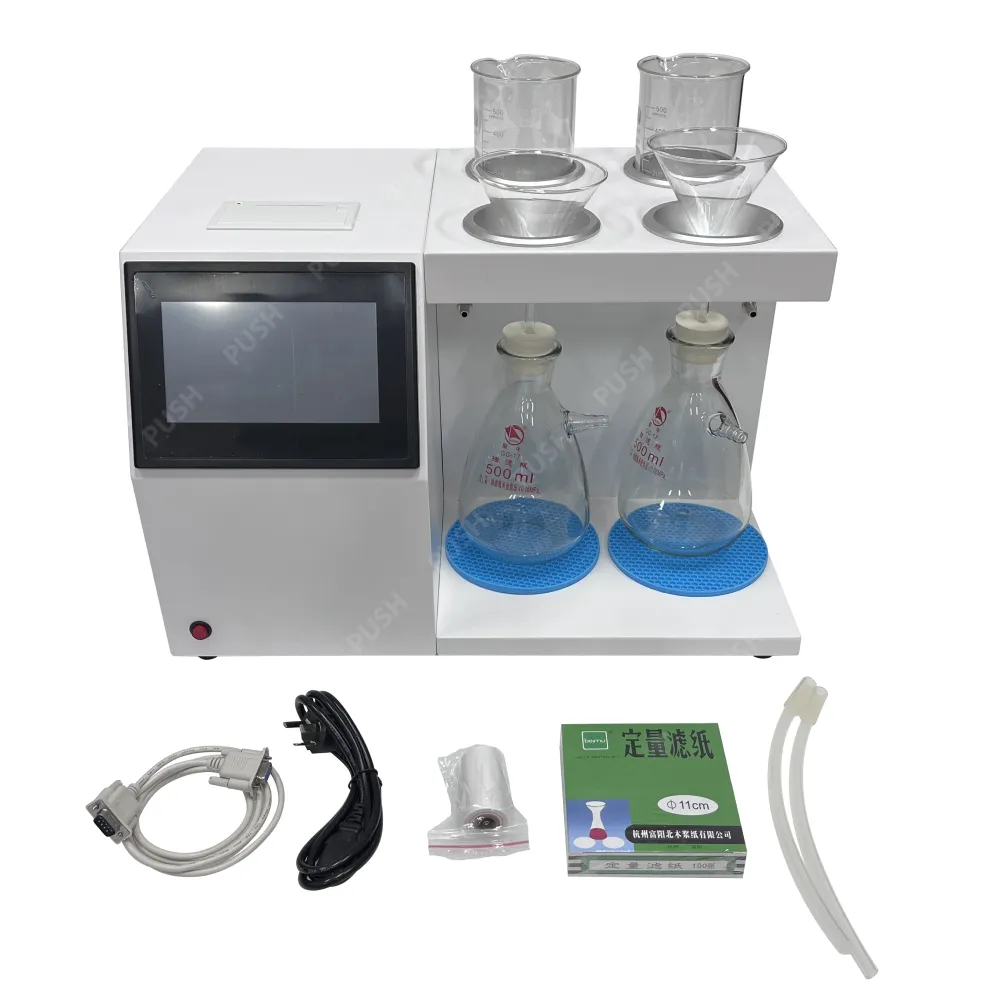
Professionals use specifically designed equipment capable of delivering highly accurate resistance measurements. Instruments like micro-ohmmeters are employed due to their ability to provide precise low-resistance readings. By sending a known direct current through the winding and measuring the voltage drop across the winding, technicians can calculate the resistance using Ohm's Law. Precision in this process ensures reliability and validity of the results, which are critical for decision-making concerning equipment maintenance and operation.
Moreover, expertise in interpreting these results is indispensable. While raw numbers might indicate high resistance, skilled technicians possess the expertise to understand the nuances of these readings. They can differentiate between resistance changes caused by temperature variations versus those caused by more concerning mechanical or electrical issues. This level of expertise ensures that only statistically significant deviations prompt further action, thus avoiding unnecessary maintenance while ensuring equipment reliability.
measurement of winding resistance
Beyond the measurable numbers, the authority of winding resistance measurement rests in its integration as a routine maintenance practice within the electrical engineering field. It is a recognized standard across industries for condition assessment. Institutions and professionals advocating for this diagnostic tool as a pivotal part of maintenance routines have established its authority over decades of empirical evidence and success stories.
Trustworthiness in winding resistance measurement is founded on standardized protocols and equipment used worldwide. International standards such as those set by IEEE and IEC ensure uniformity across practices, enabling cross-industry trust in the results of these measurements. Calibration of instruments and adherence to procedural standards are non-negotiable aspects that guarantee the reliability of the resistance values obtained.
Emphasizing an experience-built narrative further cements trust. Organizations sharing case studies where winding resistance measurements accurately predicted and averted potential downtimes due to transformer failures offer tangible proof of its practical benefits. These stories do more than just validate the process; they inspire confidence among stakeholders and motivate the adoption of such practices across various sectors.
Ultimately, the details in winding resistance measurements — captured through precision, interpreted with expertise, standardized through authoritative practices, and seen in the light of real-world applicability — anchor its critical role in maintaining the health, efficiency, and reliability of key electrical systems. As technology advances and the demand for uninterrupted power supply grows, mastering this measurement and integrating it seamlessly into preventive maintenance regimes will continue to uphold its indispensability.