Calculating the cost of setting up an oil distillation plant can be a complex venture. However, understanding the influencing factors can offer clarity to prospective investors and project managers, ensuring that strategic decisions are made with a full awareness of the financial implications.

The first component to consider is the initial capital expenditure, which involves the acquisition of land and construction of facilities. The geographical location determines the land cost significantly, making this an area where due diligence is paramount. Licenses and permits are essential, with varying costs depending on the local, state, and federal regulations. These administrative expenses must be accounted for early in the budgeting process.
Machinery and equipment constitute the core of the expenditure. This ranges from the distillation columns, heat exchangers, pumps, to control systems. Seeking high-quality, reliable machinery helps in minimizing downtime and maintenance costs which, although not part of the initial investment, play a critical role in the long-term operational budget. It's advisable to partner with reputable manufacturers or suppliers that offer comprehensive after-sales support.
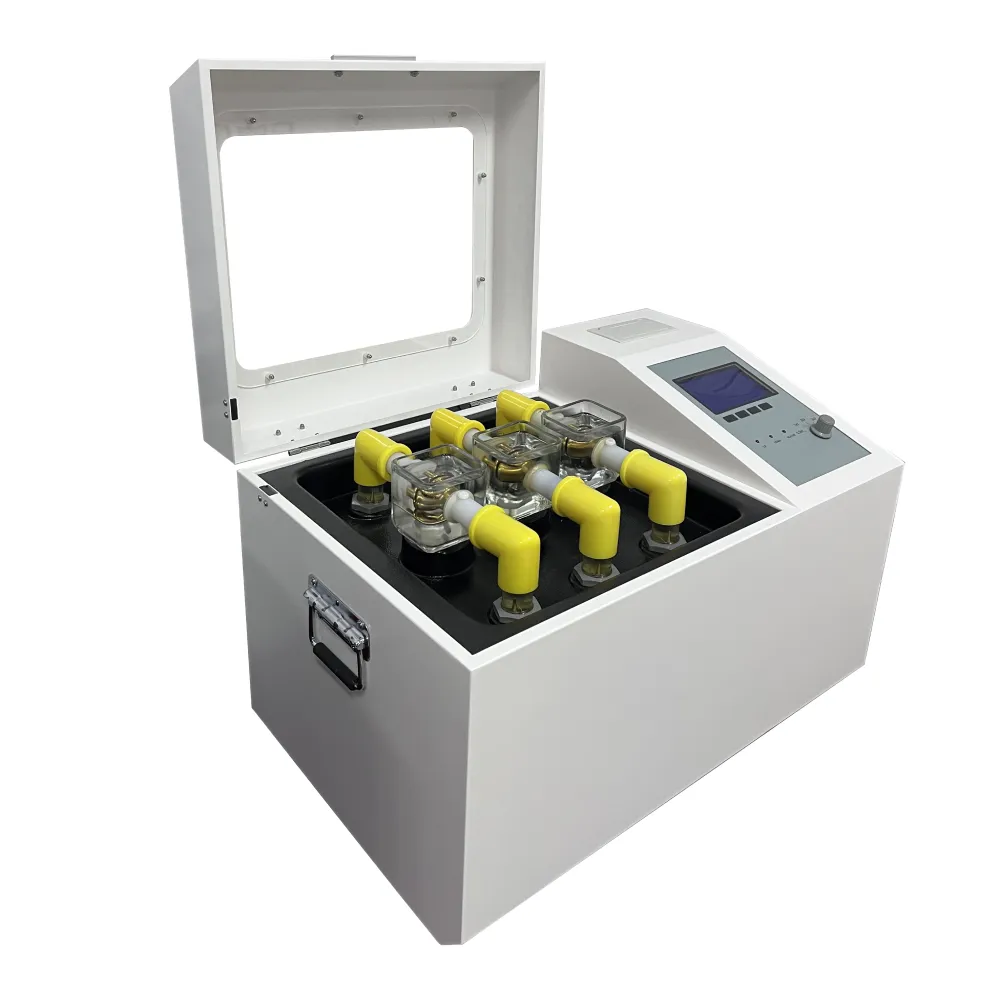
The installation costs, including civil works, electrical fittings, and piping, can be significant and vary based on the complexity and scale of the project. Importantly, these expenses should be itemized and incorporated into the financial plan to prevent budget overruns.
On the human resource front, hiring skilled labor, from engineers to plant operators, is essential. Salaries and benefits over the plant's lifecycle represent ongoing costs that should be considered part of the plant's operational expenditure. Training programs are also a wise investment, ensuring that employees are up-to-date with the latest technologies and safety protocols.
Utility costs, such as water, electricity, and natural gas, form an integral component of the operational expenses. Establishing agreements with utility providers early can lock in favorable rates, which will help in cost forecasting and management.
oil distillation plant cost
Environmental compliance is another critical area. Adhering to environmental regulations might necessitate the installation of emissions control systems or waste treatment facilities, adding to both the initial and operational costs. The burgeoning global emphasis on sustainability could also see governments offering financial incentives for incorporating green technologies, such as advanced biofuels production or carbon capture solutions, into the plant design.
Insurance coverage must not be overlooked. Protecting the plant from potential risks such as natural disasters, equipment failures, or industrial accidents is a prudent decision, ensuring financial stability in the face of unforeseen events.
The importance of a well-structured financial strategy cannot be understated. Engaging experienced financial analysts and project managers during the planning phase will ensure an accurate estimate of both initial and long-term costs, facilitating a more realistic assessment of the project's profitability timeline.
Lastly, strategic investment in research and development can provide a competitive edge by increasing efficiency and reducing costs over time. Innovation can lead to the development of superior processes or equipment that enhance the plant's overall profitability and sustainability.
In sum, the cost of building an oil distillation plant is multi-faceted, requiring thorough planning and execution across different dimensions. By focusing on both current and future financial health, stakeholders can create a robust operational framework that promotes long-term growth and profitability in this capital-intensive industry.