Exploring the Essential Role of the Oil Tester Machine in Modern Applications
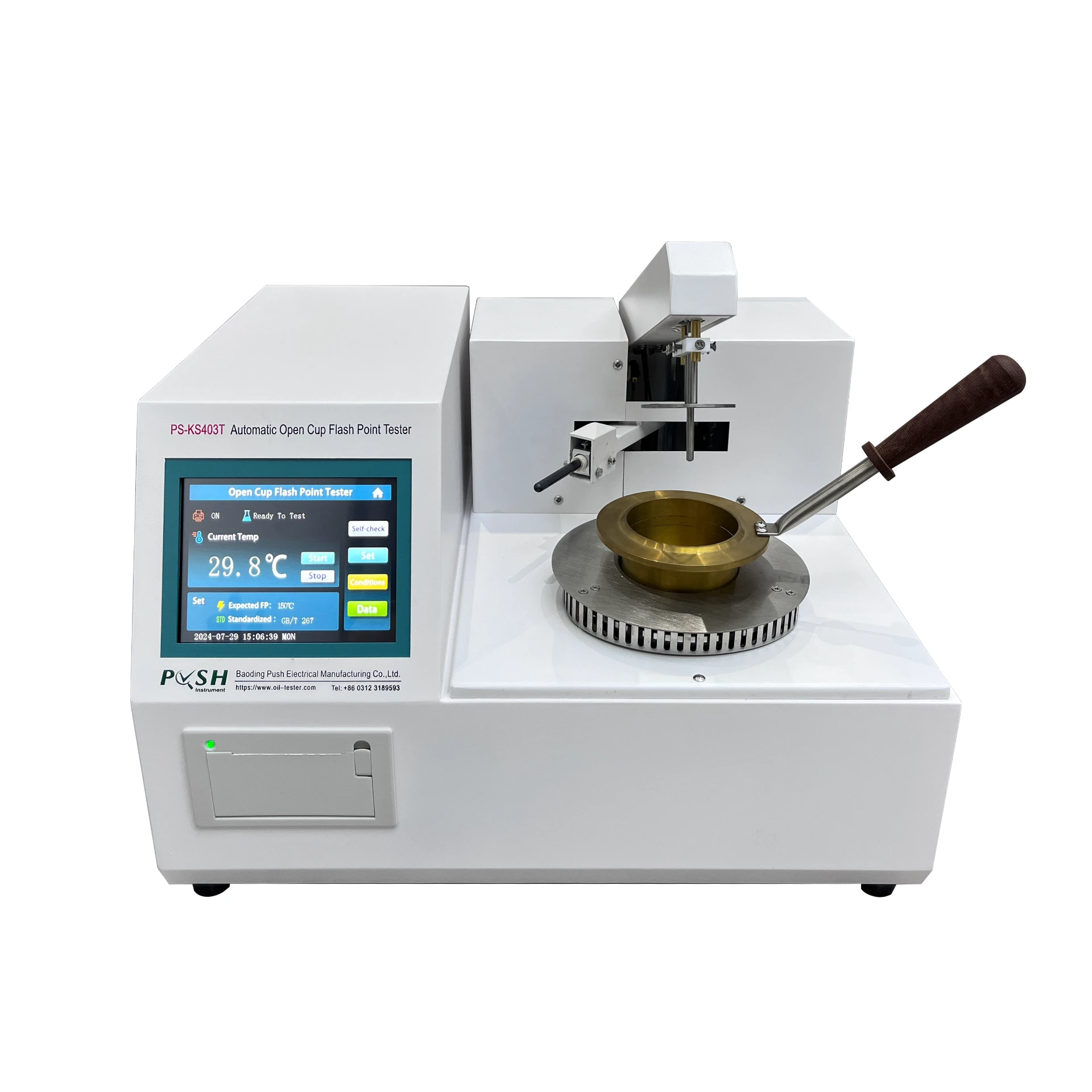
In numerous industries today, the reliability and performance of equipment are non-negotiable factors that play a crucial role in safety and operational efficiency. Amidst these needs, the oil tester machine has emerged as an indispensable tool. Its unparalleled ability to offer accurate, timely insights into oil conditions ensures machinery operates smoothly and effectively, preventing costly downtime and extending equipment lifespan.
The cornerstone of the oil tester machine's value lies in its capacity for real-time analysis. Unlike traditional oil testing methods, which are often time-consuming and labor-intensive, these modern devices seamlessly integrate into maintenance workflows, providing instant data that allow for swift decision-making. The immediacy with which they operate means that potential issues like contamination, wear particles, or degrading oil quality are detected early, allowing technicians to implement corrective actions without delay.
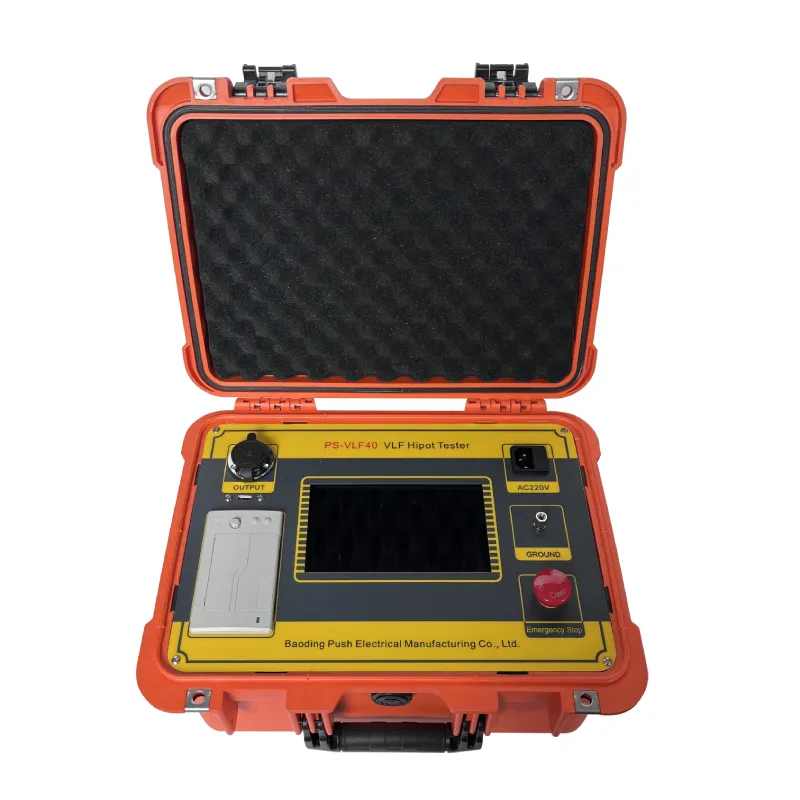
The oil tester machine's precision and accuracy are underpinned by advanced technological features. From automated viscosity measurement to moisture and particulates detection, these machines harness a multitude of sensors and analytical algorithms. This level of expertise in design ensures that the results garnered are not only precise but also repeatable, fostering an environment of trust in the data collected. Technicians and engineers alike rely on this data to devise strategies that reduce repair costs and improve equipment uptime.
Authority in oil testing also stems from the machines' adaptability across various sectors. They are employed extensively in automotive, aerospace, manufacturing, and energy sectors—essentially anywhere oil is a critical component of machinery. A testament to their versatility is the inclusion of customizable testing protocols that cater to the specific needs of different industries, ensuring that the output is not only relevant but highly actionable.
oil tester machine
Additionally, the trustworthiness of oil tester machines is bolstered by rigorous industry certifications and compliance with international standards. Quality assurance is a key concern, and these machines typically undergo extensive testing to meet ISO and ASTM standards, providing clients with the confidence that the oil analysis is accurate and reliable. This compliance helps businesses meet regulatory requirements, demonstrating a commitment to operational excellence and safety.
Experiential learning is also a significant part of what makes oil tester machines an excellent investment. Many manufacturers offer comprehensive training programs to ensure that personnel can effectively use the machines and interpret the results. This training not only enhances the capabilities of the workforce but also optimizes the integration of oil tester machines into the existing maintenance regimes, enhancing the overall efficiency.
The relationship between oil tester machines and Predictive Maintenance (PdM) strategies further underscores their importance. By leveraging data analytics, these machines aid in forecasting potential machine failures before they happen. This predictive approach—fueled by historical and real-time data—enables maintenance teams to schedule interventions just in time, thus saving on unnecessary labor and parts replacement costs. In this context, oil tester machines are not just tools but pivotal elements in strategic maintenance planning.
Ultimately, the investment in an oil tester machine extends far beyond the immediate benefits of improved maintenance practices. It represents a proactive approach towards sustaining operational excellence and competitive advantage. By providing a lens into the unseen workings of machinery, these machines allow businesses to operate with heightened confidence and reduced risk.
In conclusion, the oil tester machine is more than a tool—it's a critical ally in achieving optimal machinery performance. With unparalleled expertise, trustworthiness, and adaptability, it supports various industries in maintaining their machinery's integrity and safety, ensuring that operations continue without interruption and with the highest level of precision.