Navigating the world of industrial testing equipment can be daunting, but for those working with fuels and lubricants, the pour point tester is an indispensable tool. Understanding its importance, functionality, and application is crucial for industry professionals looking to ensure optimal performance and reliability in their products.
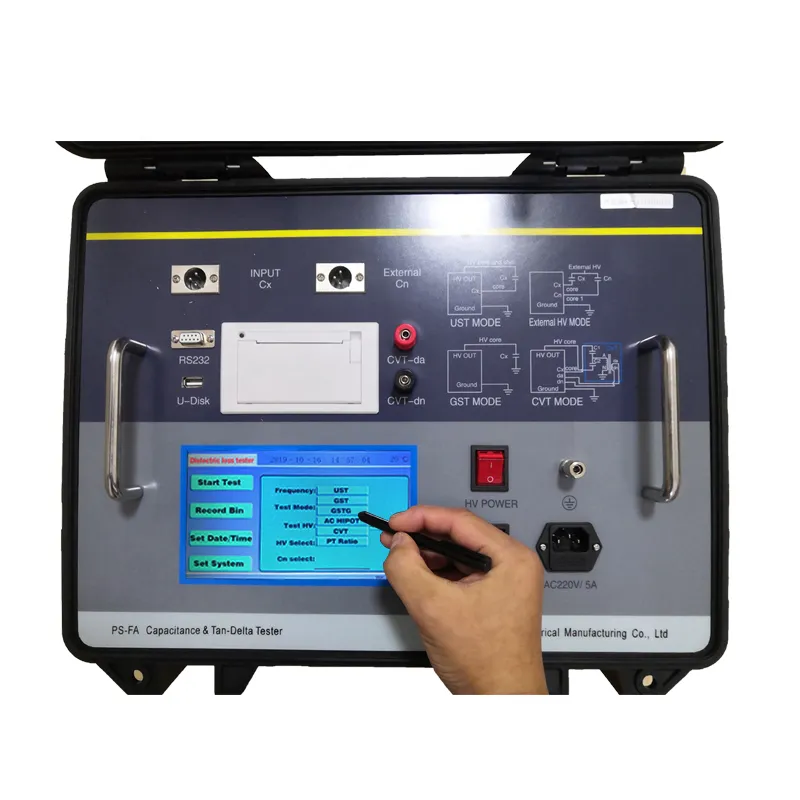
A pour point tester is specifically designed to measure the lowest temperature at which a fluid can flow. This critical measurement helps determine the cold weather operability of fuels and oils, thereby influencing formulation and specification decisions in industries such as automotive, aeronautical, and manufacturing. The testing process involves chilling the substance under controlled conditions and noting the temperature at which movement ceases, providing valuable data on fluid behavior under low temperatures.
The reliability of a pour point tester directly correlates with that of the products being tested. In extreme cold climates, lubricants must remain fluid to maintain engine performance and fuel must flow to sustain combustion processes. Recognizing the pour point of these substances ensures that engines and equipment can operate efficiently, preventing costly downtimes or mechanical failures.

For industry practitioners looking to invest in a pour point tester, understanding the nuances of different models is essential. Many testers now incorporate advanced technologies such as programmable temperature regulation and digital readouts. Automatic pour point testers, for instance, offer enhanced precision and repeatability over their manual counterparts, minimizing human error and improving data accuracy.
Expertise in handling pour point testers grows from both practical experience and a firm grasp of the testing environment. Operators must be adept at sample preparation, which involves ensuring contaminants do not skew results. This level of competence allows for consistent reproduction of test conditions, a key factor in maintaining product standardization across batches.
pour point tester
Moreover, maintaining the integrity of pour point testers also necessitates regular calibration and servicing. An authoritative understanding of equipment care not only extends the lifespan of the tester but also sustains its accuracy and efficiency. Manufacturers typically prescribe maintenance schedules and offer technical support, helping users address troubleshooting promptly.
Building trustworthiness in the competitive landscape of pour point testing equipment suppliers calls for transparency and the provision of empirical data. When manufacturers detail their testing methodologies and validate performance claims with certifications from recognized bodies, they reinforce their credibility. This openness, paired with positive user reviews and case studies exhibiting successful applications, strengthens market trust.
The industrial sector faces increasing demands for both sustainability and efficiency, and pour point testers play a pivotal role in meeting these expectations. High-quality testing leads to the development of more resilient and environmentally friendly fuels and lubricants. By minimizing the risk of product failure under adverse weather conditions, manufacturers not only advance technological progress but contribute to global ecological sustainability.
In conclusion, the significance of pour point testers in evaluating the cold flow characteristics of fuels and lubricants cannot be overstated. From ensuring dependable performance in sub-zero conditions to aiding in the research and development of superior fluid products, pour point testers are integral to the future of industrial innovation. Users must therefore approach their selection and utilization with an informed perspective, aligning with best practices and staying ahead of technological advancements to ensure their investments yield maximum value.