Pre-commissioning tests of power transformers are critical to ensuring the reliable operation and long-term safety of electrical systems. Based on my extensive experience in the field, the following insights will provide a comprehensive guide on this essential phase of transformer deployment.
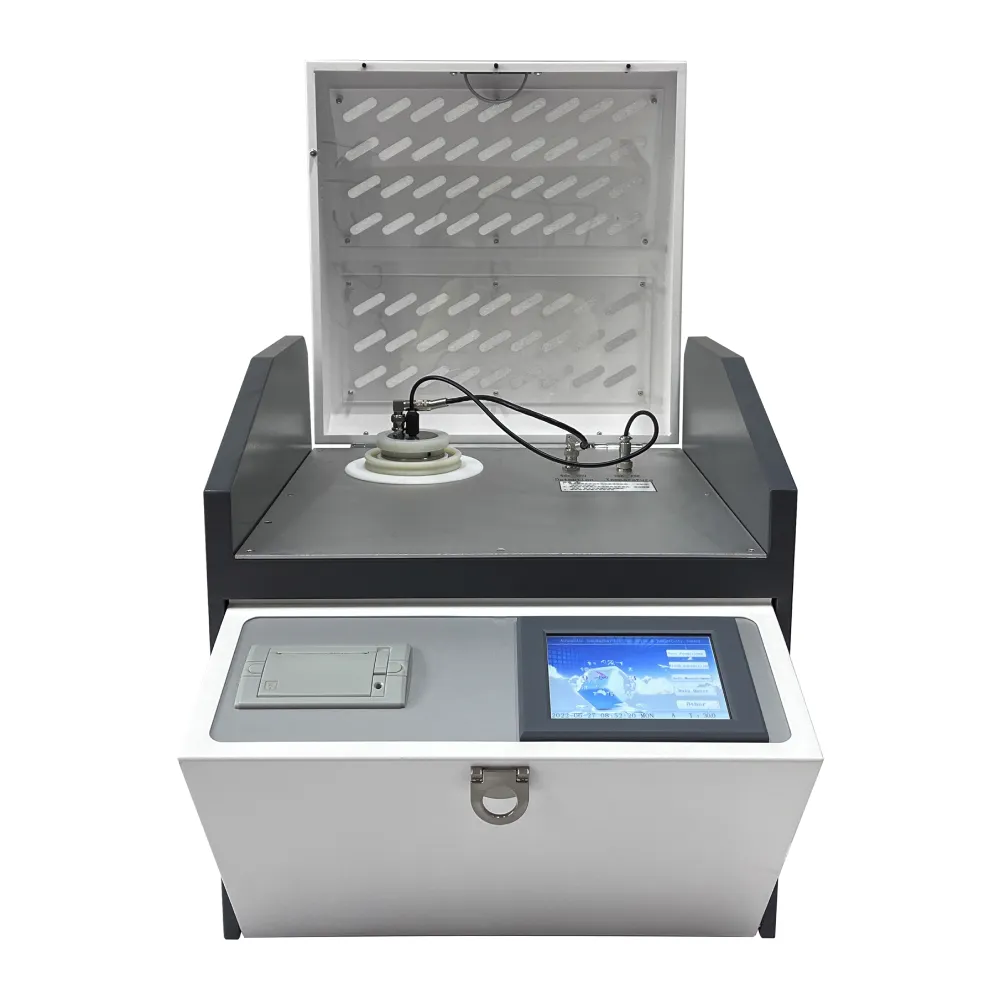
One of the foremost tests conducted during pre-commissioning is the insulation resistance test. This test assesses the insulation quality of the transformer windings and the overall health of its insulation system. An insulation resistance test can predict potential failures, thus averting catastrophic breakdowns in the future. For optimal results, it is advisable to perform this test both before and after vacuum processing to ensure the insulating oil has properly processed the residual moisture.
Next, the turns ratio test is vital for verifying that the transformer's turn ratios meet the designed parameters, ensuring proper voltage regulation and system stability. This test involves measuring the primary and secondary winding ratios, comparing them against the nameplate values. Deviations here can indicate manufacturing defects or winding damage, which should be addressed immediately to prevent system inefficiencies or failures.
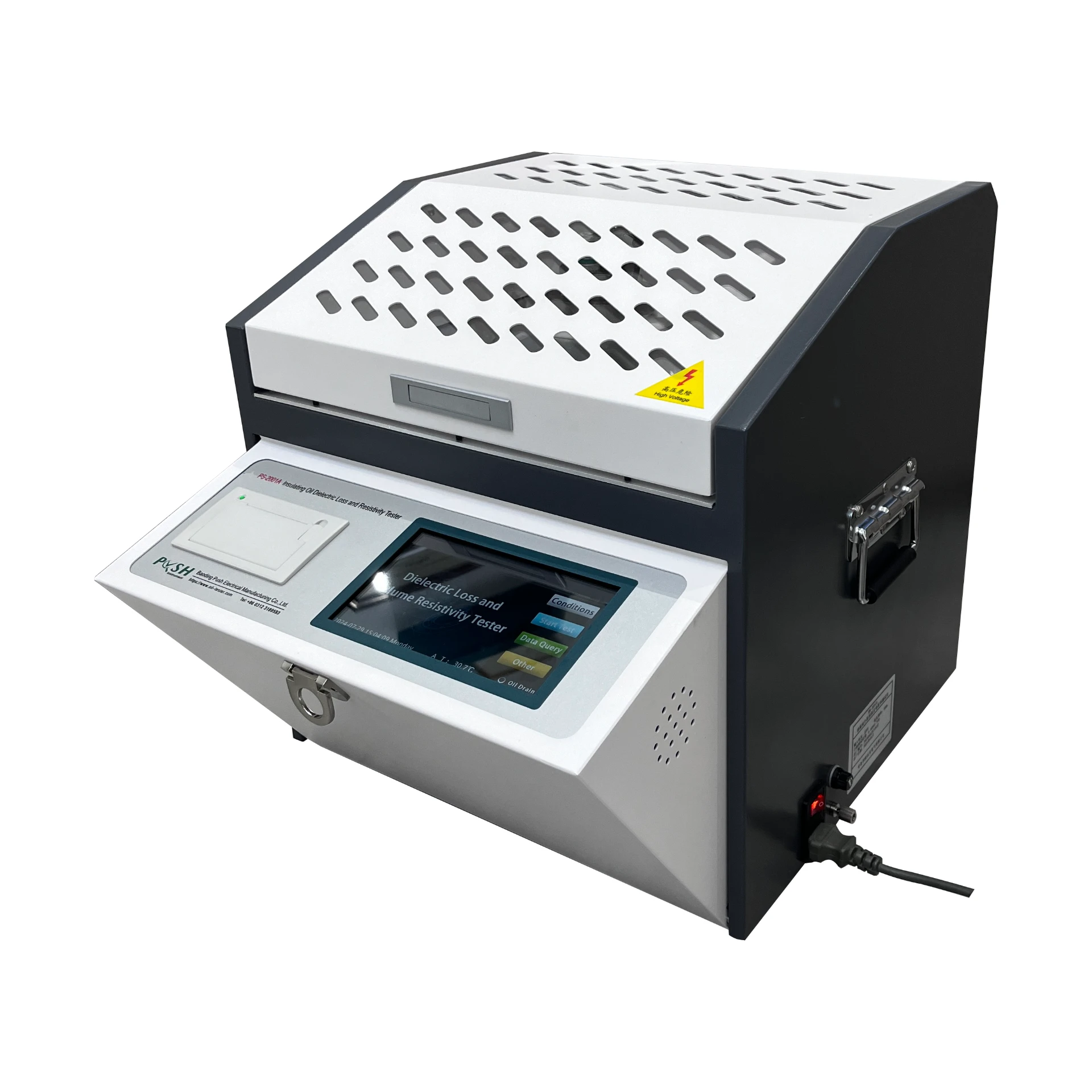
The sweep frequency response analysis (SFRA) is another critical test, offering detailed insights into the mechanical and electrical integrity of the transformer. By examining the frequency response, any mechanical displacements or electrical issues within the windings can be identified and rectified before energizing the transformer. SFRA is particularly invaluable in detecting core movements and winding deformations, often unseen through conventional testing methods.
Dissolved gas analysis (DGA) is yet another crucial test every expert will agree upon its necessity before commissioning. DGA analyzes the types and quantities of gases dissolved in the transformer's oil. This allows for early detection of potential issues, such as arcing, overheating, or insulation breakdown, by identifying gas patterns that indicate different types of faults. Regular DGA monitoring ensures ongoing operation remains safe and efficient, mitigating the risk of fault conditions that may lead to service interruption or equipment failure.
pre commissioning test of power transformer
The power factor test is essential to ascertain the dielectric losses within the insulation system of the transformer, determining the efficiency of the system. A higher power factor indicates higher losses, which could result from deteriorating insulation. Identifying these issues before commissioning can lead to corrective measures that enhance the transformer's operational lifespan and efficiency.
Furthermore, the polarity and vector group tests ensure that the transformer's connections align with the intended configuration, which is crucial for parallel operations and system balance. Ensuring correct polarity prevents severe operational faults, including phase failure or transformer unbalancing, which can affect the wider network's reliability.
To uphold the highest standards of trustworthiness and authority in the practice of pre-commissioning power transformers, it is imperative to partner with certified professionals equipped with cutting-edge testing instruments. Adhering to industry standards such as IEEE or IEC guidelines ensures that all pre-commissioning activities mirror the best practices, safeguarding not only the transformers but the entire electrical system into which they are integrated.
In conclusion,
the pre-commissioning phase for power transformers is indispensable. Through a detailed and thorough testing regime—comprising insulation resistance, turns ratio, SFRA, DGA, power factor, and polarity and vector group tests—transformers can be reliably integrated into electrical systems, ensuring their functional integrity and longevity. Prioritizing these expert-recommended procedures contributes vastly to the sustainable and efficient operation of power transmission infrastructure, underscoring the importance of quality assurance in every installation.