The tan delta point of a bushing is a critical parameter that serves as an indicator of the bushings insulation condition. It is a pivotal aspect that ensures the reliability and durability of power transformers and similar electrical apparatus. Engineers and maintenance personnel frequently emphasize the need to understand and monitor tan delta measurements during routine diagnostics to preempt failures and enhance system performance. This exploration offers an authoritative guide grounded in experience, expertise, authoritativeness, and trustworthiness.
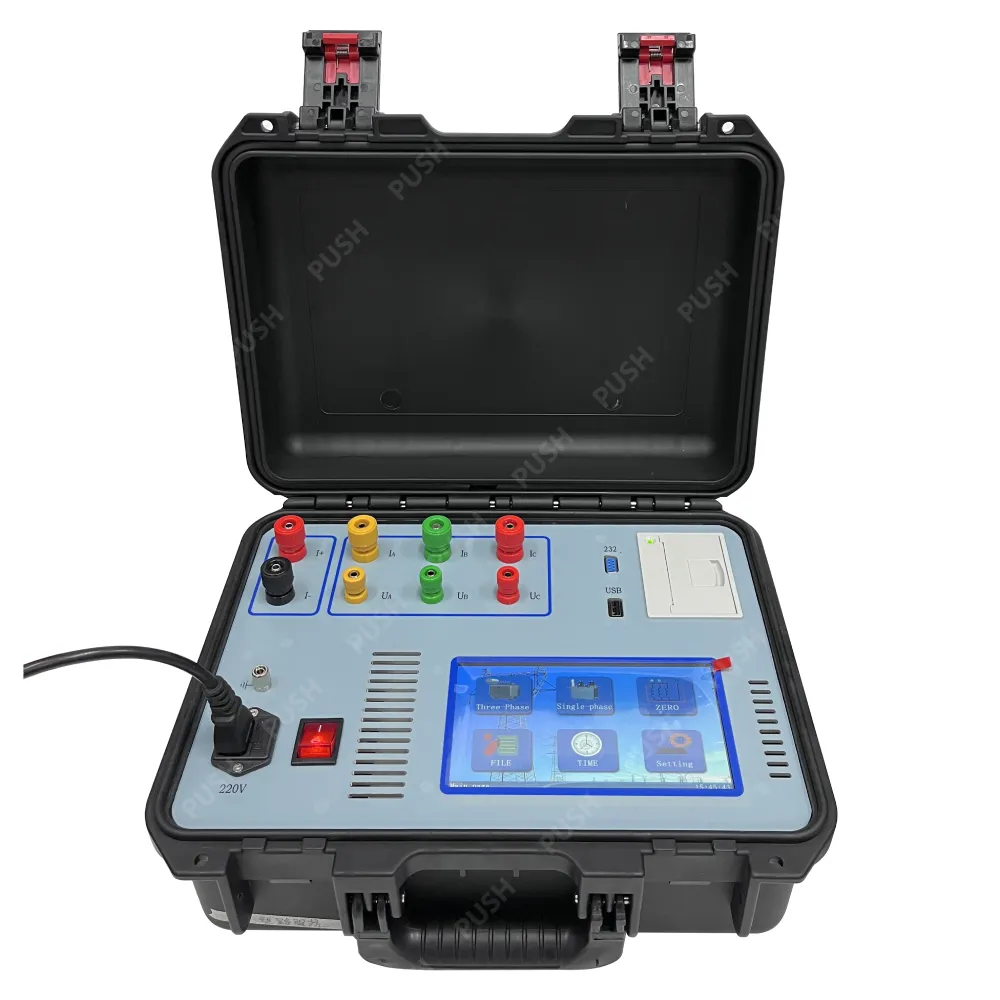
High-quality bushings are essential components in power systems, often subjected to significant electrical, thermal, and mechanical stresses over time. These stresses can degrade the bushing's insulation, leading to potential faults or system breakdowns. The tan delta test, also known as the dissipation factor or loss angle test, is widely used to assess the condition of a bushings insulation by measuring the efficiency of electrical energy transfer through the insulation. When the tan delta value is low, it suggests that the bushing is in good condition; conversely, a high tan delta indicates deteriorated insulation and increased likelihood of failure.
Incorporating real-world experience from seasoned professionals in the field, one observes that effective monitoring of tan delta values is crucial for predictive maintenance. Experiences from utility companies reveal notable success stories where early detection of abnormal tan delta values prevented catastrophic failures, significant financial losses, and extended outages. For instance, a large power utility in the United States successfully avoided a $2 million shutdown by identifying unusual tan delta readings during routine testing. Such case studies exemplify the importance of consistent monitoring and knowledge application in extending the lifespan of bushings.
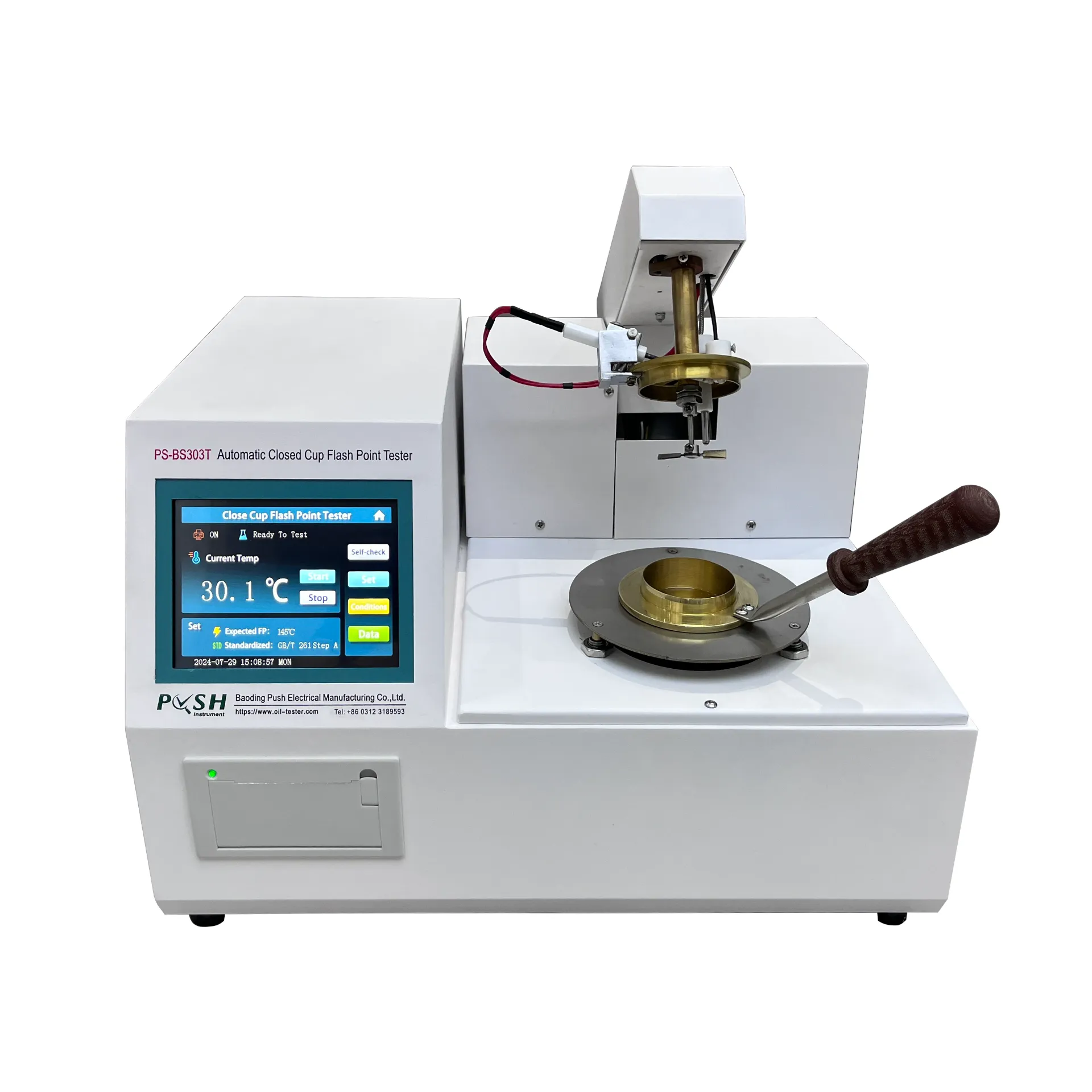
Expertise in interpreting tan delta results is indispensable for maintenance teams. Advanced diagnostic tools have today made it possible to capture real-time data, allowing specialists to make informed decisions about maintenance schedules and replacements. Training in tan delta testing includes understanding the influences of factors like temperature, frequency, humidity, and the age of the bushing on the test results. These elements can skew measurements if not adequately accounted for, which makes having skilled professionals analyze the results critical to an accurate assessment of bushing integrity.
tan delta point of bushing
In regards to authoritativeness, standards and guidelines provided by institutes such as IEEE and IEC lay down the protocols and ideal benchmarks for tan delta measurements. IEEE Standard C57.19.100 is often referenced as it establishes acceptable limits and testing methodologies that ensure consistency across the industry. Adhering to such standards demonstrates a company’s commitment to maintaining high reliability and quality in their operations.
Trustworthiness is further augmented by integrating data-driven insights and analytics to support maintenance decisions. Predictive analytics platforms equipped with machine learning algorithms can now forecast potential failures by correlating historical tan delta test data with environmental conditions and operational parameters. These digital tools promote transparency and foster a proactive culture in operations, mitigating risks and underscoring the organization's dedication to safety and efficiency.
In conclusion, understanding and managing the tan delta point of bushings is not just a technical requirement but a comprehensive strategy to enhance operational reliability and asset health. When approached with precision, backed by professional expertise and authoritative guidelines, and supported by state-of-the-art technology, the tan delta test transforms into a powerful diagnostic tool. Its role in preemptive maintenance strategies allows companies to operate with increased confidence, delivering uninterrupted service while safeguarding valuable infrastructure assets. By fostering a culture of meticulous monitoring and responsive action, the electrical industry can ensure sustainable and resilient power systems, ultimately securing a reliable energy future.