Ensuring the seamless operation of transformers before they are fully integrated into electrical systems is crucial. Transformers, being pivotal in voltage regulation and distribution, must undergo rigorous testing before commissioning. This ensures not only optimal performance but also reinforces safety and economic efficiency. Here, we delve into the comprehensive process of testing transformers before commissioning, offering insights derived from extensive expertise and experience in the field.
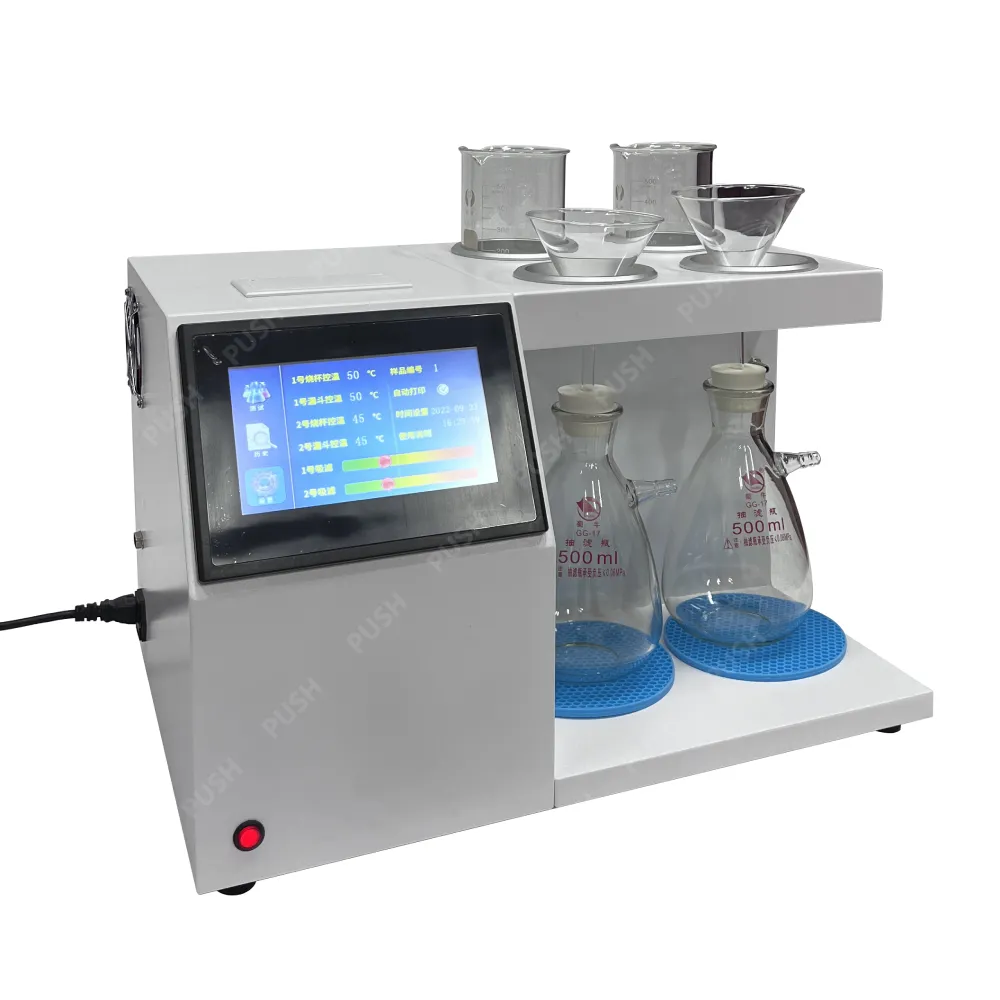
Transformers, the heart of electrical distribution systems, must be meticulously scrutinized before they are powered up. This comprehensive testing process ensures that transformers are ready to meet operational requirements, minimizing the risk of failures and outages. Each transformer is subjected to a series of tests that validate its design, construction, and functionality.
1. Insulation Resistance Testing One of the first steps is to verify the condition of the insulation system within the transformer. Insulation resistance tests are conducted to ensure that the insulation between the windings and the transformer's core is intact. This test prevents future insulation failure, which could lead to catastrophic breakdowns. Experts recommend performing this test under various environmental conditions to gauge the insulation's adaptability and resilience.
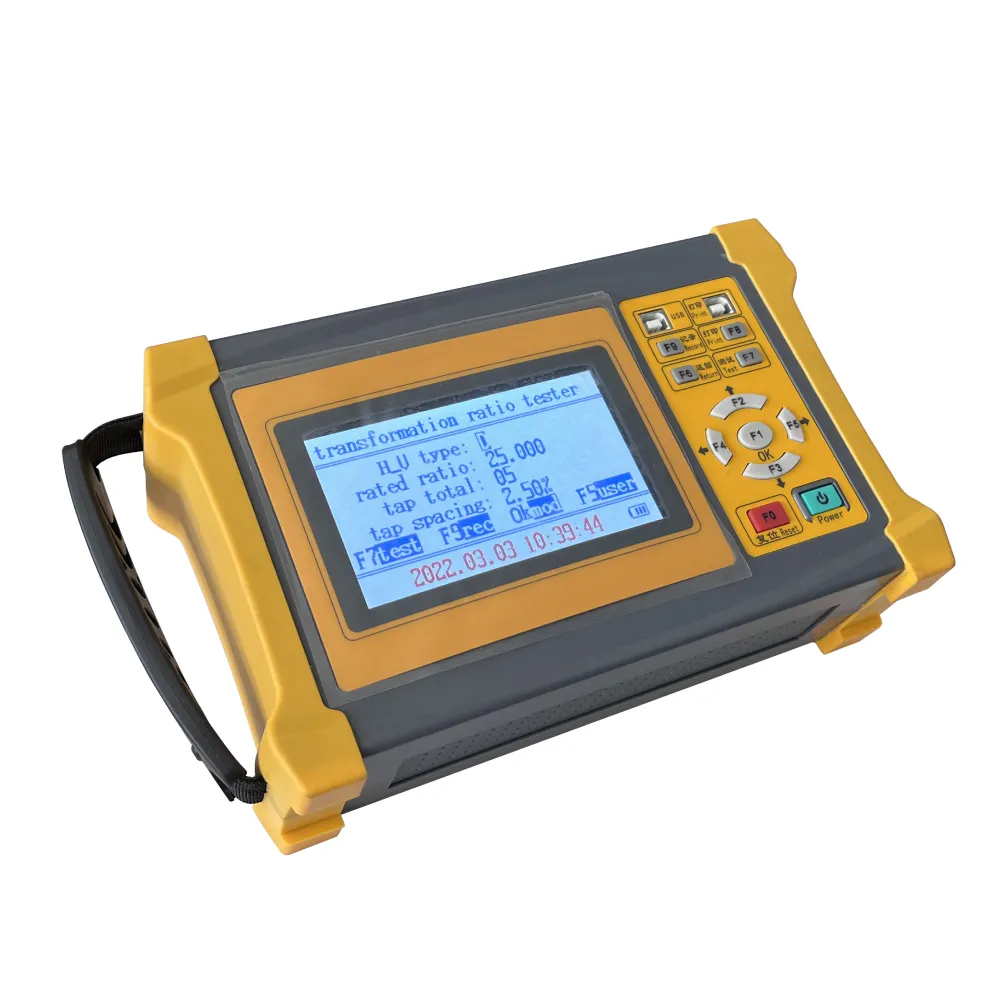
2. Ratio Tests Another critical test performed is the transformer turn ratio (TTR) test. This procedure checks the voltage transformation from the primary to the secondary winding and ensures the transformer is producing the correct voltage output. A deviation from the expected results could indicate winding issues or connectivity problems, which must be resolved prior to commissioning.
3. Winding Resistance Measurement Essential for detecting potential issues with the winding, such as loose connections, winding resistance measurement helps identify imbalances or irregularities. Skilled professionals interpret the data, ensuring that there are no discrepancies that could impact transformer performance.
4. Dielectric Tests These tests assess the transformer’s ability to withstand high voltage stresses, validating the insulation between the electrical windings. During dielectric tests, transformers are subjected to voltage levels above their operational limits to ensure that they can handle surges or peak conditions safely.
This gives operators confidence in the transformer’s robustness.
5. Leakage and Pressure Tests These assessments are vital for transformers filled with cooling oil. Checking the system for leaks ensures that the transformer will operate efficiently, as oil serves as both a coolant and insulation medium. Pressure tests complement this by confirming the containment integrity of the transformer tank.
test before commissioning of transformer
6. Functional Tests of Protective Devices Ensuring all protective devices, such as overload relays and pressure relief valves, are functioning is imperative. By testing these devices, professionals confirm that the transformer can protect itself automatically against faults or overload conditions.
7. Power Factor Testing The power factor test is critical for determining the efficiency of the transformer. A high power factor indicates that the transformer is efficient at converting input power to output power, a sign of optimal performance.
8. Temperature Rise Tests Conducted to ensure that the transformer can handle temperature stresses during operation, these tests simulate load conditions to measure the temperature rise. This ensures that transformers operate safely under expected load conditions without overheating, which could lead to performance degradation.
Implementing these rigorous tests requires deep technical expertise and industry know-how. Professionals conducting these tests rely on a combination of advanced technology and hands-on experience to interpret results accurately. The testing phase is critical, saving operators from costly downtime and repairs and extending the operational life of the transformer.
Failures and inefficiencies in transformers not only lead to expensive repairs but also pose safety risks. Therefore, the pre-commissioning testing of transformers is not just an operational requirement but a value-driven approach towards reliability and safety in electrical systems.
In conclusion, conducting comprehensive tests before commissioning transformers is a non-negotiable aspect of electrical system management. It embodies a synthesis of expertise, authoritative methodologies, and trustworthiness, ensuring that transformers will function under their designed parameters efficiently. By investing in robust pre-commissioning tests, industries safeguard their infrastructure, optimize performance, and uphold safety standards, reinforcing their commitment to operational excellence and sustainability.