Testing procedures prior to commissioning transformers, induction motors, and alternators are crucial steps in ensuring optimal function and longevity of these electrical components. As these components are integral to numerous industrial and commercial applications, their pre-commissioning tests must be executed with precision, underlining the principles of Experience, Expertise, Authoritativeness, and Trustworthiness (EEAT).
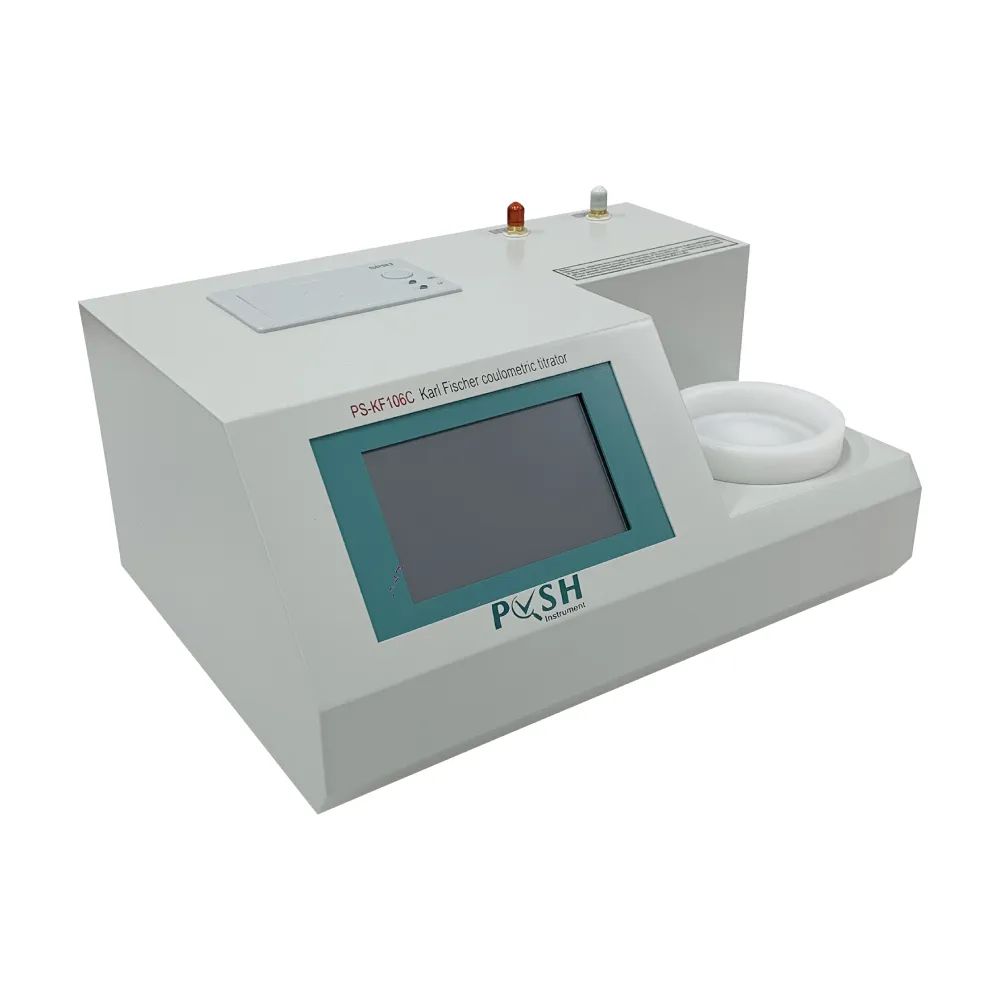
Experience Undertaking pre-commissioning tests demands a thorough understanding developed through years of hands-on experience. Experienced engineers know that each component behaves uniquely under different conditions. For transformers, one must conduct insulation resistance tests and turns ratio tests to confirm insulation health and winding accuracy. Experience dictates that an insulation resistance test exceeding 1,000 megaohms typically indicates good insulation. Similarly, for induction motors, running a no-load test helps identify any paralleled winding issues, a problem experienced engineers are well-versed in resolving. Alternators require particular attention to excitation systems, therefore open-circuit and short-circuit tests are deployed to ensure they are set to operate under varied load conditions without faltering.
Expertise Pre-commissioning tests demand a high level of expertise for precise execution and interpretation of results. Transformer testing includes dielectric withstand and sweep frequency response analysis (SFRA) tests, which require expert knowledge to assess insulation system condition and mechanical integrity. For induction motors, examining the rotor bar health through current signature analysis needs expert insights to interpret anomalies unsusceptible to superficial scrutiny. Alternators benefit from an expertise-driven approach to load tests, simulating real operational conditions to check the voltage regulation and overall dynamic performance of the alternator in practice.
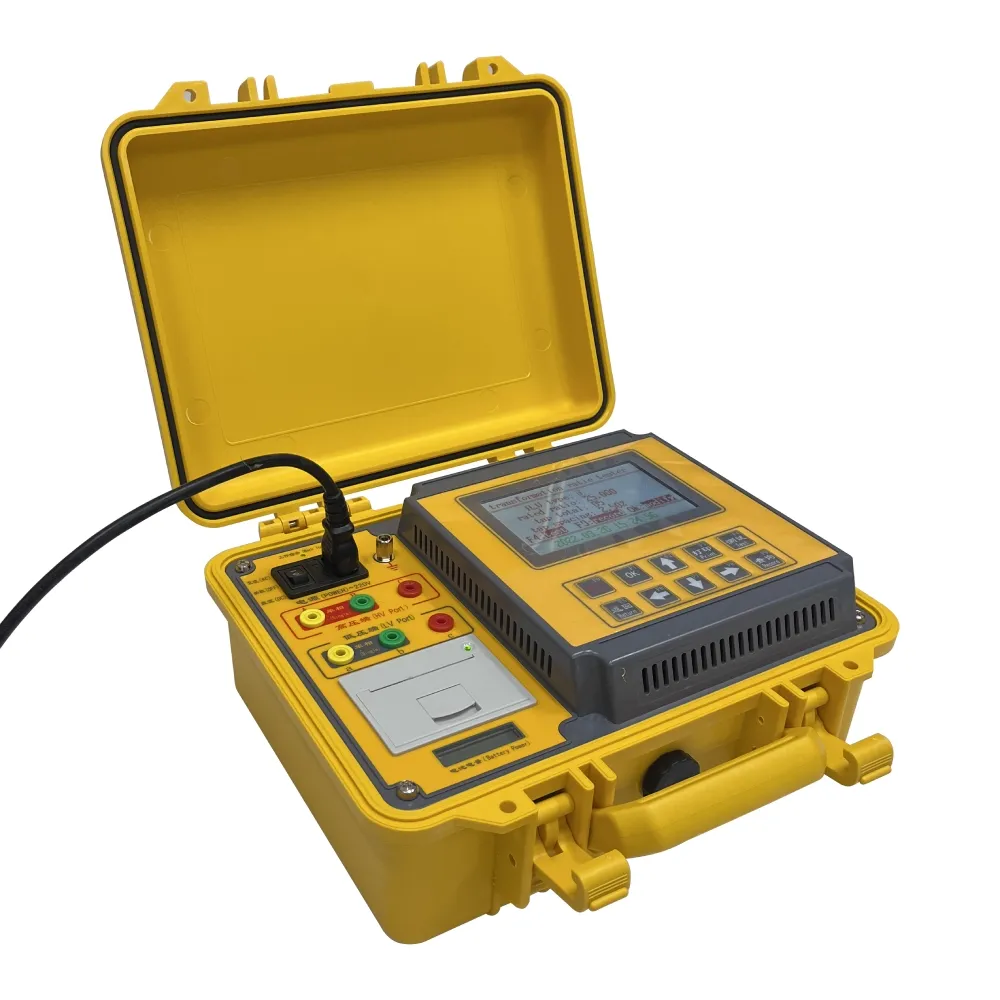
tests before commissioning of transformer induction motor and alternator
Authoritativeness Guidance from authoritative industry standards like the IEEE and IEC is indispensable. Compliance ensures that the pre-commissioning tests are universally recognized in quality and safety. The IEEE Std C57.12.90 provides detailed testing procedures for transformers, crucial in maintaining quality assurance. For induction motors and alternators, IEC 60034 standards dictate the mechanical and electrical testing frameworks, reinforcing a framework of authority and reliability. Those performing these tests gain authority by aligning strictly with such globally acknowledged standards, providing assurance to all stakeholders involved.
Trustworthiness Trust in pre-commissioning outcomes is non-negotiable, demanding transparent and reproducible methods. Adopting advanced testing technologies like partial discharge testing for transformers builds trust as it detects faults that traditional methods might miss. For induction motors, thermal imaging inspections offer a trustworthy means of identifying overheating issues, preventing potential failures. Similarly, alternators’ trustworthiness is bolstered through infrared thermography, detecting potential hotspots that traditional methods might overlook. Data collected through these tests should be documented meticulously and stored for future audits, ensuring that all stakeholders have access to transparent and reliable evidence of performance.
In conclusion, pre-commissioning tests of transformers, induction motors, and alternators not only require hands-on experience and specialized expertise but must be carried out adhering to the authoritative guidelines that build trust among stakeholders. As industries grow increasingly reliant on such components to maintain productivity and efficiency, executing thorough pre-commissioning tests stands central to ensuring uninterrupted, reliable performance. By anchoring testing processes on the principles of Experience, Expertise, Authoritativeness, and Trustworthiness, enterprises can confidently commission their electrical components, anticipating long-term operational reliability and efficiency.