Understanding the intricacies of measuring the breakdown strength of oil is vital for industries relying heavily on transformer operations, lubrication systems, and other oil-dependent machinery. This critical parameter indicates how well a liquid can withstand electrical stress without failing. Increasingly, industries are keen to explore efficient methods to test the breakdown strength of oil, not just for maintenance purposes but to ensure operational safety and longevity.
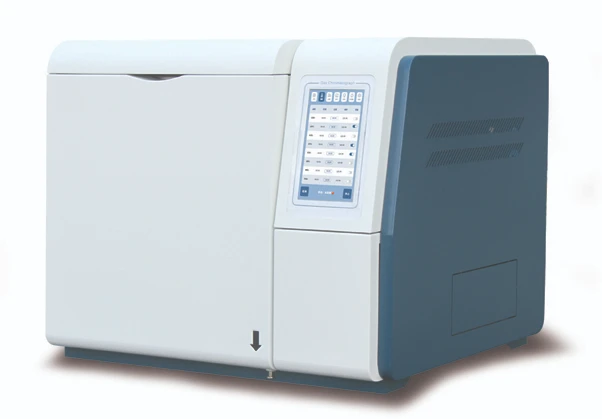
Breakdown strength is a measure of the maximum voltage that an insulating oil can withstand before it breaks down and begins to conduct electricity. This characteristic is pivotal to maintaining transformer health and preventing faults that may lead to costly downtime or, worse, catastrophic failures.
The process of measuring breakdown strength, though technical, is straightforward when following best practices.
The Procedure Real Experience and Best Practices
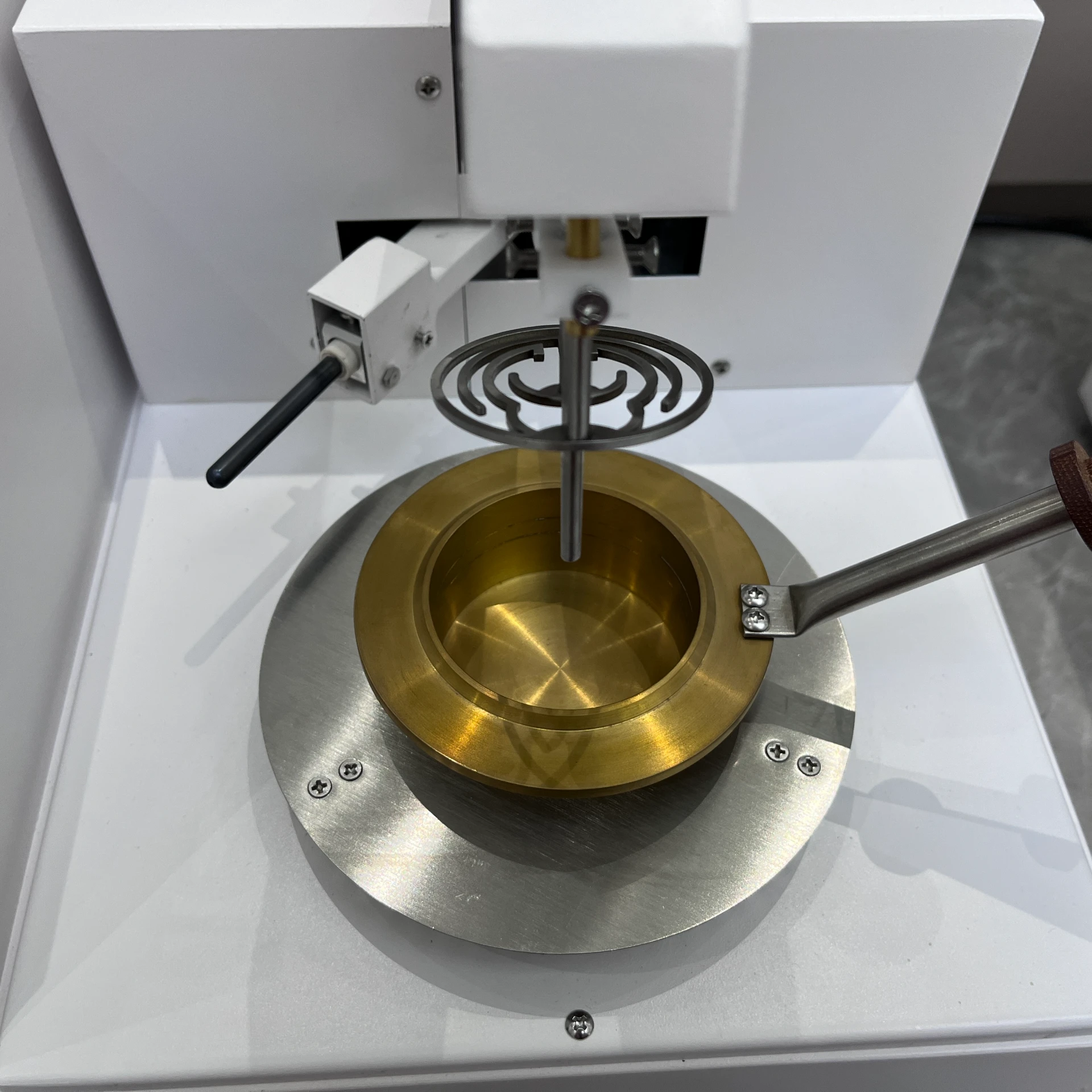
Testing the breakdown strength of oil involves several methodical steps. Firstly, sample collection is crucial and should be conducted with precision to avoid contamination, which could skew results. Use hermetically sealed jars for collecting samples directly from the operational point, ensuring minimal exposure to the atmospheric elements.
Once the sample is secured, it is placed in a standardized test cell. The test cell consists of two electrodes where the oil acts as a dielectric medium. Voltage is gradually applied to the oil, increasing steadily until the oil fails and allows current to pass between the electrodes. This voltage level is recorded as the breakdown voltage of the insulating oil.
Expertise in this field is demonstrated through a meticulous approach to controlling the environment in which the test is conducted. Ambient conditions such as temperature and humidity can influence results, and it’s recommended to maintain a stable environment, often 20°C with 50% relative humidity, to ensure consistency in testing. Moreover, the electrodes must be cleaned and maintained regularly. Contaminants or irregular surfaces on electrodes may result in misleading measurements, affecting the product’s reliability.
Professional Insights Importance of Repeated Testing
One significant piece of advice from industry leaders is the importance of repeated testing and cross-referencing outcomes. Initial testing provides a baseline; however, changes over time due to environmental exposure or operational stresses can impact oil quality. Performing periodic tests aids in monitoring these conditions, offering insights into maintenance needs or impending failures.
Authoritative Industry Standards and Recommendations
Adhering to and referencing industry standards such as ASTM D1816 or IEC 60156 builds a framework of trust around your testing process. These standards specify clear protocols for preparing samples, executing tests, and interpreting results, which not only enhance credibility but also compliance with global quality standards.
to measure breakdown strength of oil test can be done
The preferred apparatus in these standards often includes the VDE type testing vessel, noted for its reliability and consistency. These standards also underscore the importance of dielectric oil cleanliness. Minute particles, water content, and air bubbles are crucial factors affecting breakdown strength and must be carefully managed.
Building Trust Documentation and Transparency
Industries must document each test comprehensively. Keeping records of observational data, environmental conditions, equipment calibration, and maintenance ensures that the process is transparent. This documentation becomes invaluable, especially during audits or operational reviews, accentuating the trustworthiness of your testing regime.
Transparency extends to reporting and analyzing results. Sharing findings with stakeholders in a clear, concise manner facilitates informed decision-making. It can lead to proactive maintenance strategies, thereby extending equipment life and optimizing performance.
Innovative Techniques and Technologies
With technological advancements, new methods of measuring the breakdown strength of oil are emerging. Automation in testing facilities, for instance, reduces human errors and increases the efficiency of repetitive testing cycles. Furthermore, integrating AI-driven analytics allows for the effective prediction of breakdown events, facilitating preemptive interventions.
Experts are advocating the use of portable, field-operable devices that facilitate on-site testing. These devices are increasingly accurate, offering near-laboratory precision, and are immensely beneficial for remote locations where sending samples to centralized labs would cause unwanted delays.
Conclusion
Through a combination of real-world experience, authoritative practices, and innovative technology, industries can effectively measure and monitor the breakdown strength of oil. This not only improves the reliability of electric and lubrication systems but ensures enhanced safety and operational efficiency. By investing time and resources into improving testing methodologies and adhering to stringent standards, organizations underscore their commitment to excellence and reliability.