A transformer functions as the heart of electrical power systems, and the oil that insulates and cools its core is crucial to its longevity and efficiency. Understanding how to accurately conduct transformer oil level checks is essential for electrical engineers and maintenance personnel who seek to prolong the lifespan of these vital machines.
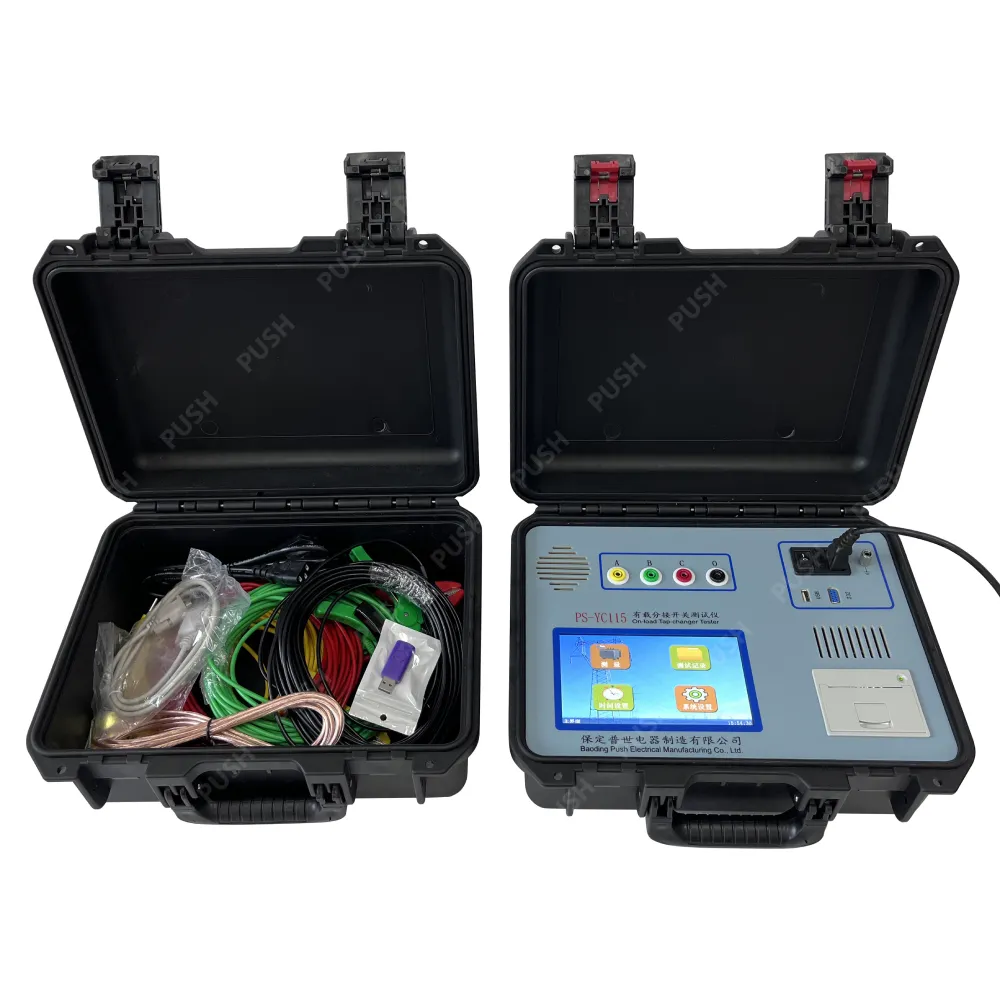
Transformer oil serves numerous purposes. It acts as a dielectric material, which helps in insulating the transformer's windings, preventing electrical faults and overheating. Moreover, it dissipates the heat generated within the transformer. Low oil levels can compromise the transformer's performance and may lead to severe technical failures, posing significant risks.
Historically, transformer maintenance required manual checks, but advancements in technology have introduced innovative ways to monitor oil levels more conveniently. Experienced professionals recommend a combination of traditional and modern methods to ensure reliability and efficiency. Regular inspections involve visual examinations and more sophisticated approaches utilize sensors and diagnostics software that provide real-time data and analytics.
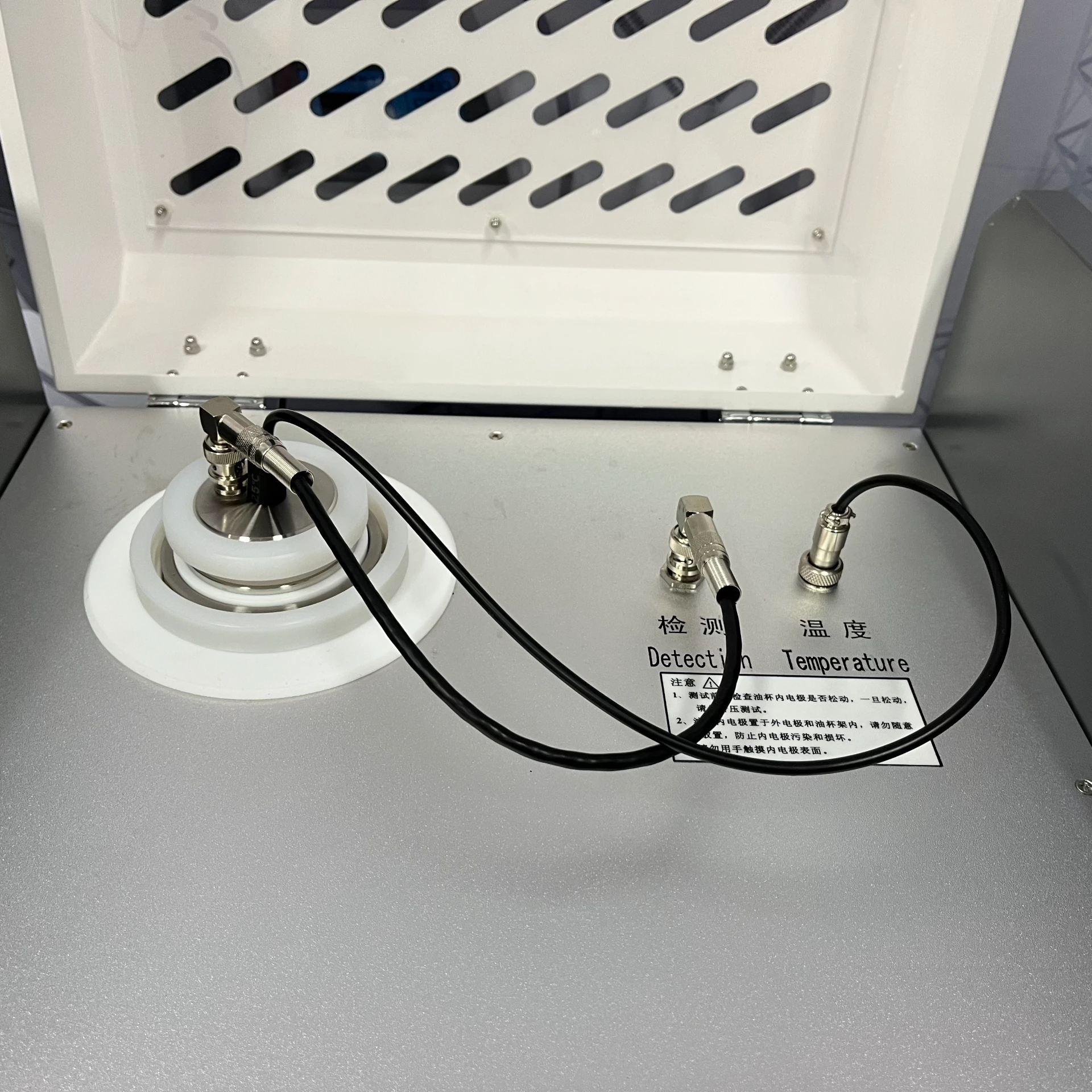
During visual inspections, always ensure safety protocols are strictly followed. Start by examining the conservator tank where the oil resides when it's not circulating. This tank is typically fitted with a gauge indicating the oil level. Changes in ambient temperature can impact readings, so it's advisable to check the oil level under standard conditions to ensure accuracy.
For enhanced accuracy and preventive care, utilizing digital sensors has become best practice. These sensors are installed within the transformer to continuously monitor oil levels and detect significant shifts or trends that could indicate leaks. The data is then analyzed using diagnostic software, which offers predictive maintenance suggestions based on historical and current operating data. This method not only optimizes the oil's performance but also significantly reduces the likelihood of unexpected equipment failure.
transformer oil level check
Transformer oil testing should also be conducted at regular intervals to detect contaminants or degradation of oil quality. Expert testing involves measuring the dielectric strength, moisture content, and acidity of the oil. High moisture levels, for instance, are a common cause of transformer inefficiency and can lead to insulation failures. Likewise, checking acidity levels reveals whether the oil has started to degrade, potentially corroding internal components.
Moreover, professionals emphasize the importance of thermographic analysis in oil level management, providing a non-invasive method to detect anomalies in temperature distribution. This supports identifying regions where low oil levels might cause excessive heat build-up.
For organizations managing large fleets of transformers, investments in data analytics and IoT technology have proven beneficial. An integrated monitoring system enables operators to manage numerous units from a centralized control point. Such systems feed real-time data into cloud-based platforms, facilitating prompt decision-making that enhances operational reliability and reduces maintenance costs.
It is crucial to have certified personnel conduct these assessments, as their expertise contributes significantly to the veracity of the evaluations and the applicability of the solutions rendered. Recognition from reputed electrical industry bodies serves as a useful benchmark for selecting qualified professionals.
In summary, maintaining appropriate transformer oil levels is not just about extending the lifespan of the equipment but also about ensuring operational safety and efficiency. Combining traditional inspection methods with innovative technology and skilled expertise manifests into a comprehensive maintenance strategy that preemptively resolves issues, thus supporting a robust electrical infrastructure. Prioritizing this aspect of transformer care highlights a commitment to advanced problem-solving and a proactive approach to equipment management, reinforcing trust and authority in the industry.