In the contemporary industrial landscape, the effective testing and commissioning of transformers are pivotal activities that ensure the reliability and safety of electrical systems. This article delves into the nuances of transformer testing and commissioning, emphasizing its crucial role in maintaining the integrity of power transmission networks and electrical installations.
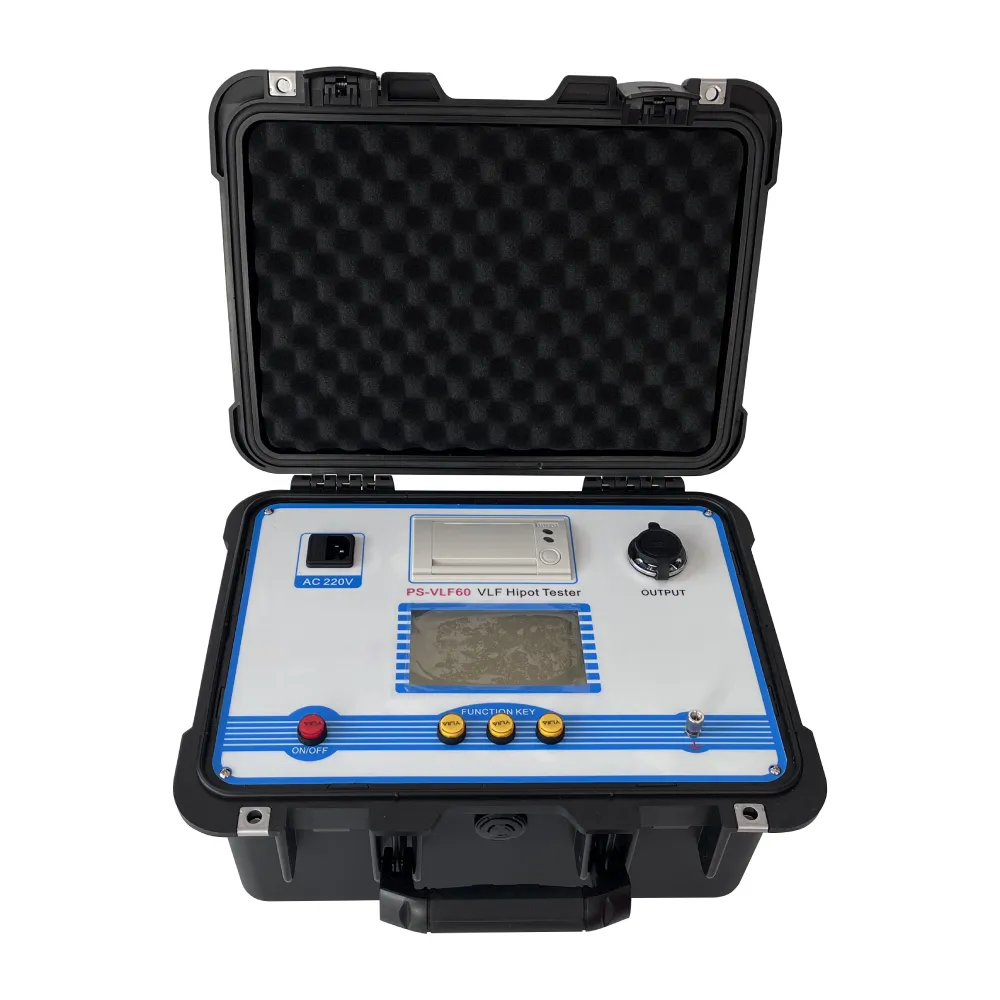
Transformers are essential components in electrical distribution and transmission systems, enabling the efficient transfer of electrical energy between circuits through inductively coupled conductors. Testing and commissioning these critical components involve comprehensive procedures that validate their operational readiness, ensuring they meet the specific needs and safety requirements of the installation environment.
Effective transformer testing begins with the comprehension of its design specifications, and it involves various types of tests that ensure the equipment will function correctly under the anticipated conditions. These include factory tests conducted by the manufacturer and site acceptance tests performed after installation. Factory tests are primarily aimed at validating the manufacture's implementation of design specifications, whereas site tests focus on verifying the transformer's performance in situ.
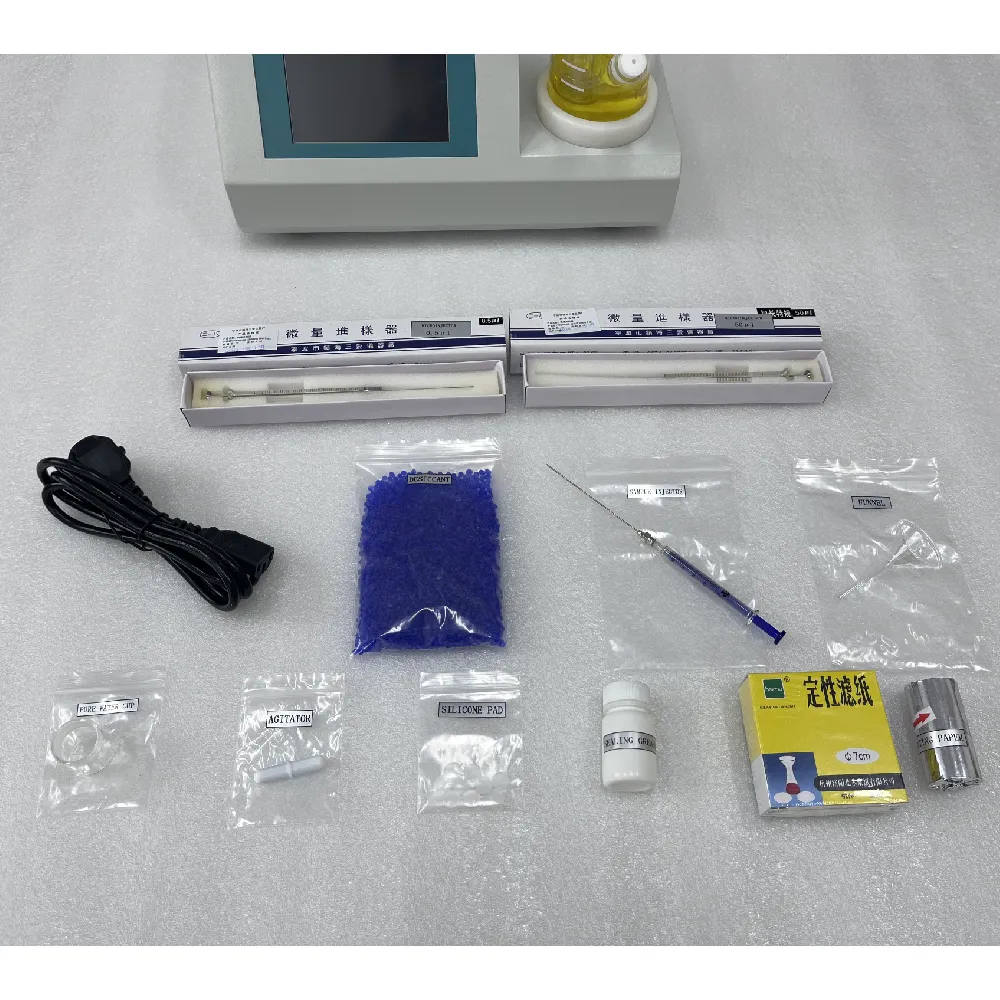
Key tests included in transformer commissioning typically encompass
1. Insulation Resistance Testing This assesses the quality of the insulation materials used in the transformer. By applying voltage and measuring the resultant current leakage, the integrity of the insulation can be evaluated. Consistent insulation resistance indicates that the transformer is free from moisture and physical damage, crucial for long-term operational reliability.
2. Turns Ratio Tests These verify the transformer's ability to convert voltages between high and low voltage systems effectively. Variations from the expected ratio could indicate shorted turns or issues with the windings, which could impact the transformer's efficiency and safety.
3. Oil Dielectric Tests For oil-filled transformers, oil quality is tested to ensure its effectiveness as an insulating medium. Poor dielectric properties in oil can lead to electrical discharge, posing a significant risk of failure.
4. Winding Resistance Tests Conducted to identify potential issues such as loose connections, poor contacts, and uneven conductor aging. Accurate winding resistance measurements ensure efficient thermal performance and longevity of the transformer.
transformer testing and commissioning pdf
5. Temperature and Thermal Tests These assess the transformer's thermal performance under load. Excessive temperature rise can compromise insulation and lead to premature aging.
6. Load Tests These are conducted to observe the transformer's performance under full load conditions, ensuring stable voltage regulation and performance efficiency.
Commissioning activities extend beyond testing, incorporating rigorous inspections and meticulous documentation. During commissioning, technicians and engineers must ensure all protective devices are correctly configured and functional, and they must verify that all connections are secure and appropriately labeled.
The importance of experienced professionals in the commissioning process cannot be overstated. Expertise in interpreting test results, identifying potential issues, and understanding the complex interplays in transformer operations is critical. Professionals with a deep understanding of electrical engineering principles, as well as a familiarity with the latest industry standards and best practices, provide assurance that the commissioning process is thorough and reliable.
Additionally, utilizing advanced tools and technologies, such as digital testing instruments and diagnostic software, enhances the accuracy of tests and the reliability of the commissioning process. These tools allow for real-time monitoring and analysis, facilitating prompt corrective actions when necessary.
Ultimately, transformer testing and commissioning are not mere formalities but essential operations that underpin the delivery of safe and continuous power. The responsibility accompanying these processes rests heavily on trust and credibility, demanding a stringent adherence to internationally recognized quality standards and safety protocols.
By engaging reputable and certified professionals, leveraging state-of-the-art technology, and fostering a culture of meticulous documentation and adherence to best practices, organizations can ensure that their transformers operate at optimal capacity, thereby safeguarding both their assets and their personnel. This proactive approach not only reduces the risk of operational interruptions but also extends the lifespan of critical infrastructure, contributing to the overall stability and reliability of power systems globally.