Understanding Transformer with Winding Resistance A Comprehensive Guide

Transformers play a crucial role in electrical systems, impacting everything from power distribution to electronic devices.
One component in transformers that often warrants significant attention is winding resistance. This article delves into the intricacies of transformer winding resistance, focusing on its implications, applications, and diagnostic techniques. As a seasoned electrical engineer with over two decades of experience in the industry, I aim to provide valuable insights that can help in both design and troubleshooting processes.
At the heart of transformer functionality is the ability to efficiently transfer electrical energy between circuits. Winding resistance, although a subtle aspect, directly influences efficiency and performance. To understand winding resistance, envision the long conductive wires wrapped around the transformer core. These wires, typically made of copper or aluminum, inherently possess a certain level of resistance. While relatively low, this resistance can affect heat generation and energy loss, impacting the transformer’s overall efficiency.
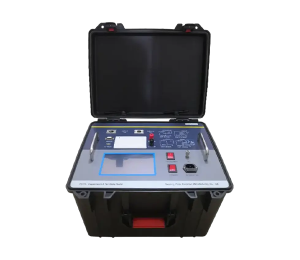
From a design perspective, precision in achieving optimal winding resistance is paramount. Transformers designed with lower winding resistance exhibit reduced energy losses, achieving near-benchmark efficiency standards. The choice of conductor material also plays a significant role; for instance, copper, with its superior conductivity, is often preferred despite being more costly than aluminum. However, the decision between copper and aluminum can depend on budgetary constraints and specific application needs.
In practice, the implications of winding resistance extend beyond energy efficiency. Heat generated as a result of resistance can lead to insulation degradation over time. This degradation is particularly critical because it leads to transformer failures, potentially causing extended downtimes and costly repairs. Industry experts underscore the importance of regularly monitoring winding resistance as part of a comprehensive preventive maintenance strategy. This ongoing monitoring can effectively attenuate risks associated with unpredicted breakdowns.
transformer with winding resistance
To measure winding resistance, specialized equipment like an Ohmmeter or a Transformer Winding Resistance Meter (TWRM) is employed. The process involves direct current (DC) being applied through the windings, and the resulting voltage drop is measured. This reading helps in calculating the resistance using Ohm’s Law. Anomalies in expected resistance readings can be indicative of issues such as faulty connections or compromised insulation. Developing expertise in discerning these readings can significantly enhance reliability and ensure compliance with electrical standards.
For professionals in the transformer manufacturing industry, addressing winding resistance during the design and testing phases cannot be overstated. Implementing stringent quality controls and leveraging advanced computational models to predict resistance behavior under different conditions often separates industry leaders from competitors. Collaborations with academic institutions frequently yield cutting-edge solutions and materials that push the boundaries of efficiency and reliability.
The operational conditions of transformers also dictate the emphasis placed on winding resistance. Environments characterized by extreme temperatures, for instance, exacerbate the challenges posed by resistance. Transformers installed in such contexts require meticulous design considerations, including enhanced cooling systems and materials capable of withstanding thermal stresses. The adoption of modern monitoring systems equipped with embedded sensors can provide real-time data on winding resistance, preemptively indicating potential issues.
Additionally, advancements in simulation technologies offer transformative insights into the behavior of winding resistance. Engineers can now virtually model different scenarios, evaluating how variables such as load changes or temperature fluctuations impact performance. This capability not only helps in optimizing current designs but also informs the development of future transformer models with optimized winding resistance.
In summary, understanding and managing transformer winding resistance is an integral part of ensuring the longevity and effectiveness of any transformer. The challenges associated with winding resistance are multifaceted, involving design, materials selection, testing, and operational considerations. Leveraging cutting-edge technologies, adopting rigorous testing methodologies, and remaining informed on the latest industry advancements fortifies transformer reliability and efficiency. As innovation continues to propel the electrical engineering sector forward, professionals equipped with an in-depth understanding of winding resistance position themselves, and their enterprises, on the forefront of engineering excellence.