When embarking on the installation of a transformer, various complexities and stringent protocols outline the procedure. Amidst these processes, certain tests might remain overlooked, often due to time constraints, budgetary limits, or the assumption that they don't critically impact functionality. However, understanding these tests, even the ones not performed, is paramount for ensuring operational excellence and longevity of the transformer. Prospective challenges, technical insights, and recommendations form the crux of our exploration into transformer installation procedures.
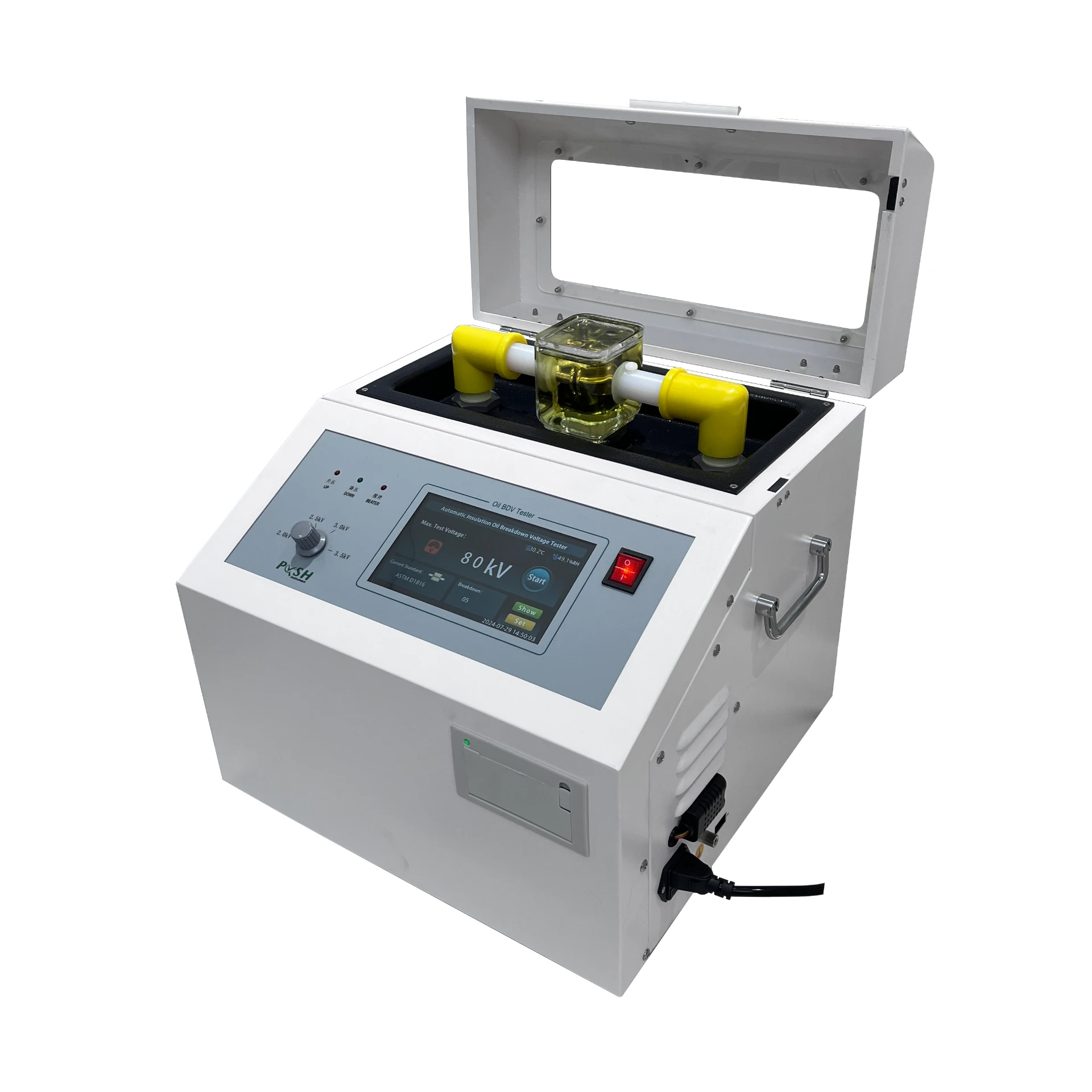
Foremost among the omitted assessments is the core loss measurement test. Often bypassed, this test evaluates the electrical losses incurred in the transformer's core due to the alternating magnetic field. Though typically conducted during the manufacturing phase, neglecting this test during installation can obscure potential efficiency issues. A transformer operating with heightened core losses may experience diminished performance and increased operational costs over time.
Another significant test that frequently remains undone is the vector group test. This assessment verifies the phase displacement and correct vector grouping of the transformer windings. While manufacturers commonly perform this test, installers may presume it unnecessary to retest post-shipping and installation. However, misalignment in phase angles or incorrect vector groups can lead to operational anomalies, such as circulating currents and unwanted harmonics, potentially damaging connected systems.
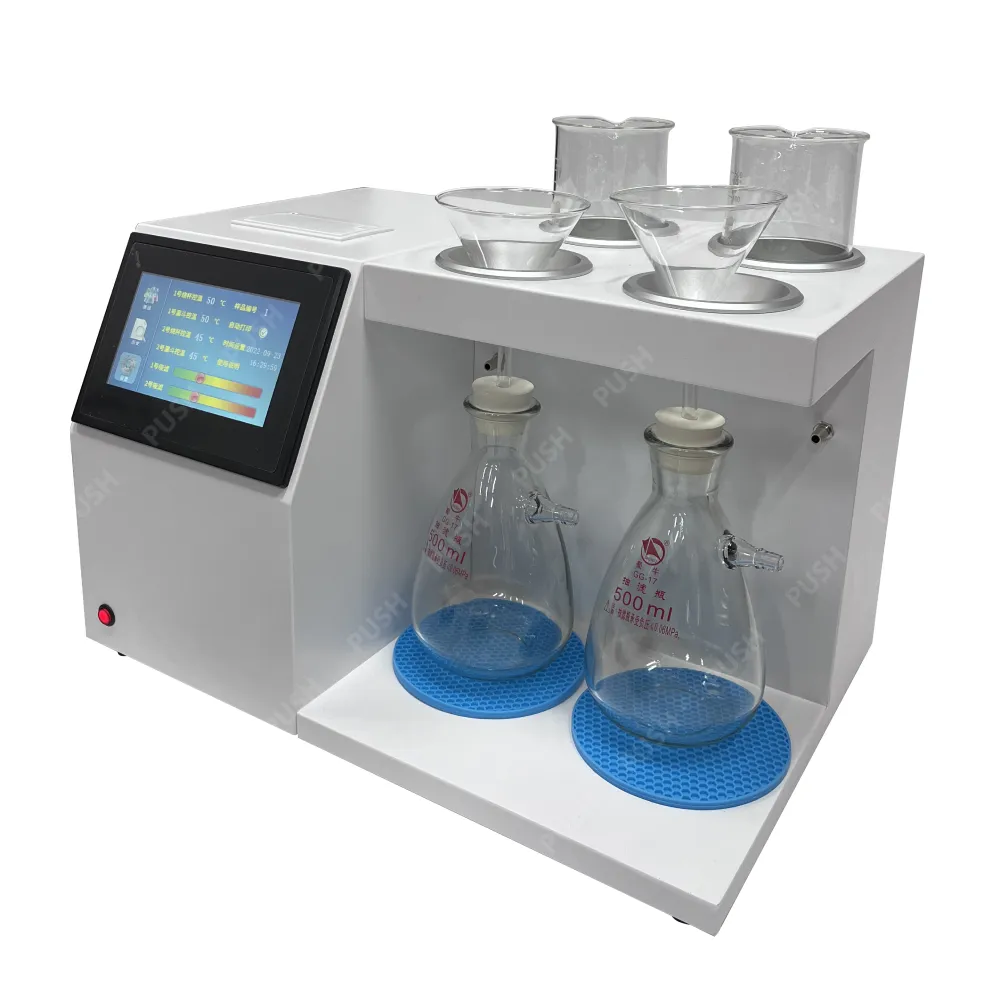
Power factor and dissipation factor tests, which ascertain the integrity of the insulation system, also often fall by the wayside during installation. Despite their criticality in identifying deteriorating insulation, time-pressed installation routines may skip these evaluations, inadvertently risking insulation failures. Even slightly elevated dissipation factors can forewarn insulation weaknesses that, if left unaddressed, could accelerate an eventual breakdown.
Moreover, the contact resistance test, crucial for assessing the quality of electrical junctions within the transformer’s circuitry, sometimes sees omission. Failing to measure this resistance can conceal loose or corroded connections, which may lead to overheating, arcing, and possible system failures down the line. For installations in environments where weathering or moisture is a factor, overlooking this test could compromise the transformer's seamless operation.
while installing transformer which tests are not performed
In many cases, installers may not perform the frequency response analysis (FRA). FRA helps in identifying mechanical displacements in the transformer windings and assessing core integrity post-transportation. This omission, despite arising often from a lack of specialized equipment or expertise onsite, jeopardizes the detection of mechanical issues that could manifest into significant operational disturbances.
Exciting current tests are another set of analyses occasionally disregarded. These tests are designed to check for abnormalities in the core, such as shorted turns or delaminating. They provide foundational data to compare against future maintenance tests. Overlooking such tests could miss early indicators of internal core problems that might exacerbate with time.
Finally, despite its importance, the winding resistance test may be omitted due to the urgency to commission the transformer quickly. This test assesses the condition of windings and connections, offering insights into potential problems like poor contacts and winding failures. Neglecting this evaluation risks overlooking latent issues that could lead to unpredicted downtimes and costly maintenance interventions.
In conclusion, while the immediate pressure to commission a transformer may tempt stakeholders to condense the range of tests, understanding the implications of non-performed tests is crucial. Ensuring these assessments are not just conducted, but are part of the standard operational checklist, reinforces a culture of meticulousness. Such thoroughness not only fortifies the transformer's functional reliability but also enhances the credibility of the engineers and organizations involved, rooting their reputation firmly in the foundations of expertise and trustworthiness. Prioritizing these tests can make the difference between a robust, long-serving asset and a transformer plagued with unforeseen issues.