In the realm of electrical engineering, the winding resistance test of a transformer stands as a crucial procedure to evaluate the transformer's health and performance. This test is indispensable for maintenance professionals and plays a pivotal role in ensuring the longevity and reliability of transformers, thereby ensuring minimal operational disruptions.
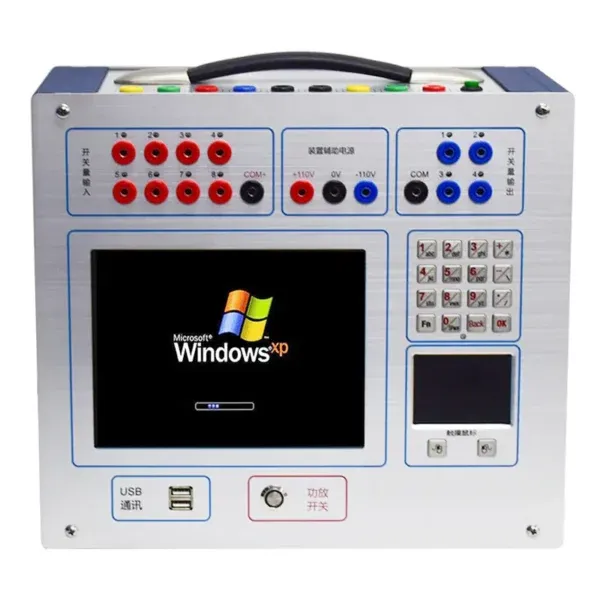
Notably, transformers are the backbone of electrical power systems, stepping voltage levels up or down at distribution stations efficiently. Within this context, winding resistance tests emerge as an instrumental diagnostic tool owing to the valuable data they provide. The primary aim of this test is to measure the resistance of the winding in the transformer's coils, thus unveiling issues like shorted turns, open circuits, or potential hotspots.
Conducting a winding resistance test requires adherence to precision and expertise. First, it is critical to ensure that the transformer is powered down and fully de-energized to prevent hazardous conditions. Once guaranteed, industry-standard instruments, such as micro-ohm meters or other precision ohmmeters, are employed to achieve accurate readings. The test meticulously measures the resistance at each coil, and these results are then compared to baseline data provided by the manufacturer.

For an accurate winding resistance test, maintaining a consistent ambient temperature is paramount. Resistance varies with temperature, necessitating a conversion of resistance values to a reference temperature, usually 20°C, to ensure comparisons are valid. Any deviations from the expected resistance values can signify deteriorating insulation, oxidation, or physical damage to winding components — all red flags that warrant further investigation.
The expertise required in executing winding resistance tests cannot be understated. Professionals must interpret the results adeptly and correlate them with supplementary tests like the insulation resistance test or SFRA (Sweep Frequency Response Analysis) to ensure comprehensive diagnostics. Anomalies detected early can avert catastrophic transformer failures, save on costly repairs, and prolong the operational life of the machinery.
winding resistance test of transformer pdf
Trustworthiness in these procedures emanates from utilizing accurately calibrated tools and adhering to established testing protocols. Furthermore, maintaining detailed records of each test and routinely comparing them against historical data create a robust database for predictive maintenance strategies.
Additionally, the authoritativeness of conducting such tests comes from relying on standardized methods and proven practices updated through rigorous training programs and international standards like the IEEE and IEC guidelines. For institutions and professionals alike, staying abreast with the latest developments in transformer testing technologies is vital. Engaging in continual professional development and certification further enhances credibility and effectiveness in the field.
Product-wise, companies dealing in transformers or those providing maintenance services significantly benefit from conducting regular winding resistance tests. Clients are assured of the quality and reliability of their equipment, while businesses can bolster their reputation through the delivery of consistent, reliable service.
To sum up,
the winding resistance test is far more than a routine check. It stands at the intersection of electrical engineering expertise and operational reliability. Execution of this test with excellent precision not only guarantees better lifecycle management of transformers but also reinforces safety and efficiency across electrical systems. As the industry advances, the role of such diagnostic tests will continue to be pivotal, underscoring the importance of expertise, authority, and trust in their execution.