Laboratory distillation units play a crucial role in various scientific and industrial processes, ranging from chemical research to essential oil extraction. Understanding their operation, structure, and purpose is fundamental for professionals aiming to leverage their capabilities effectively. These units facilitate purification, separation, and analysis of chemical substances, proving indispensable in both academic and commercial settings.

A distillation unit operates on the principle of heating a liquid mixture to selectively evaporate and then condense its components at different temperatures. This essential process requires a combination of heat sources, condensers, and receiving equipment, which are standard components of any laboratory distillation unit. Mastery of each component’s function contributes to the overall efficiency of the process, ensuring high-purity results.
There are various types of distillation, such as simple, fractional, and vacuum distillation. Each type serves a specific purpose depending on the complexity and nature of the mixtures involved. Simple distillation is suitable for substances with significantly different boiling points, while fractional distillation is employed when the differences are narrower. Vacuum distillation is used for mixtures containing components with very high boiling points to prevent decomposition, making it essential for delicate compounds.
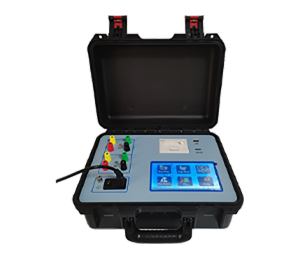
Selecting the right distillation unit involves considering factors such as purpose, scale, and precision requirements. It's important to choose a reputable supplier who adheres to industry standards for manufacturing and quality assurance. A lab’s specific applications will dictate the features necessary in a distillation unit. Many prefer modular units that allow customization of components based on current projects, providing flexibility and cost-efficiency.
Experience highlights key challenges in laboratory distillation operations, like managing heat sources and avoiding contamination. Precise temperature control is vital to prevent degradation of sensitive compounds. Utilizing modern units equipped with digital interfaces and thermostatic control can enhance accuracy and repeatability. Additionally, maintaining cleanliness and preventing cross-contamination by adhering to proper cleaning procedures and using high-quality materials can significantly impact outcomes. Glass components should be handled with care, given their susceptibility to damage and contamination.
distillation unit in laboratory
Expert knowledge of the distillation process encompasses an understanding of the thermodynamic principles and intricacies involved in phase transition operations. These include an in-depth comprehension of boiling points, temperature gradients, and material properties. Being equipped with this expertise ensures adept handling of complex mixtures, achieving desired separations without compromising integrity. Partnering with experts or undergoing specialized training can help operators advance their proficiency and ensure efficient process handling.
Authority in the field of laboratory distillation arises from evidence-backed methodologies and standards. Regulatory compliance with established industry standards such as ASTM or ISO guarantees reliability and safety in distillation procedures. These standards guide users in tuning their setups to effectively handle diverse chemical mixtures. Publications, patents, and certifications serve as credible validations of a practitioner’s skill in leveraging distillation units for optimized results.
Trust in distillation procedures is garnered through consistent, predictable outcomes derived from rigorous testing and peer-reviewed studies. Utilizing high-quality components and adhering to well-documented procedures cultivates trust in both the equipment and the expertise of the operators. Maintaining detailed operation logs and conducting regular audits further bolster transparency and facilitate troubleshooting should discrepancies occur.
Investing in a high-quality laboratory distillation unit is an investment in enhanced productivity and precision. It not only optimizes current processes but also unlocks new applications and research fields. As technology advances, integrating automation and digital monitoring into distillation units is increasingly feasible, providing benefits that extend to efficiency and scalability. Engaging with communities of practice and continuous professional development ensures that operators remain at the forefront of technological advancements, ready to capitalize on emerging opportunities in distillation science.