An Expert's Guide to No Load Loss Test for Transformers Insights and Best Practices
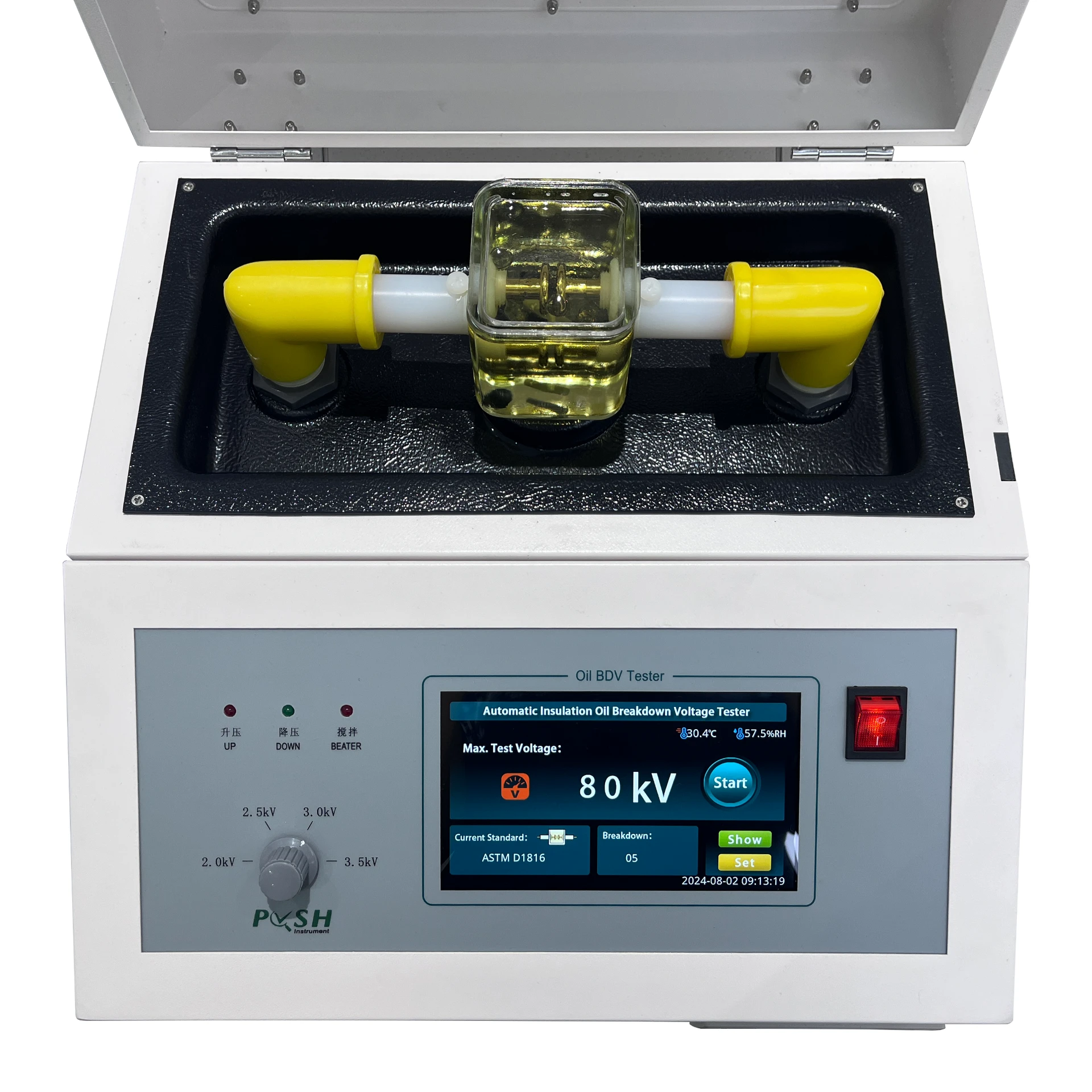
In the realm of electrical engineering, the precision and efficiency of a transformer are paramount for optimal performance. A critical aspect influencing these parameters is the transformer's no load loss, which reflects the energy expended when the transformer is energized but not supplying load. Thus, understanding and conducting an accurate no load loss test is vital for engineers and manufacturers. This article aims to guide you through a comprehensive understanding of this test, encompassing its relevance, methodology, and expert insights for enhanced product excellence.
The importance of the no load loss test in transformers cannot be overstated. Essentially, this test measures the core loss—consisting of hysteresis and eddy current losses—when the transformer operates at its rated voltage but without load. The no load loss test serves as a litmus test for the core material quality and manufacturing precision. Given the rising global energy costs and an increasing focus on sustainability, minimizing these losses translates to significant operational efficiency and cost savings over the transformer's lifecycle.
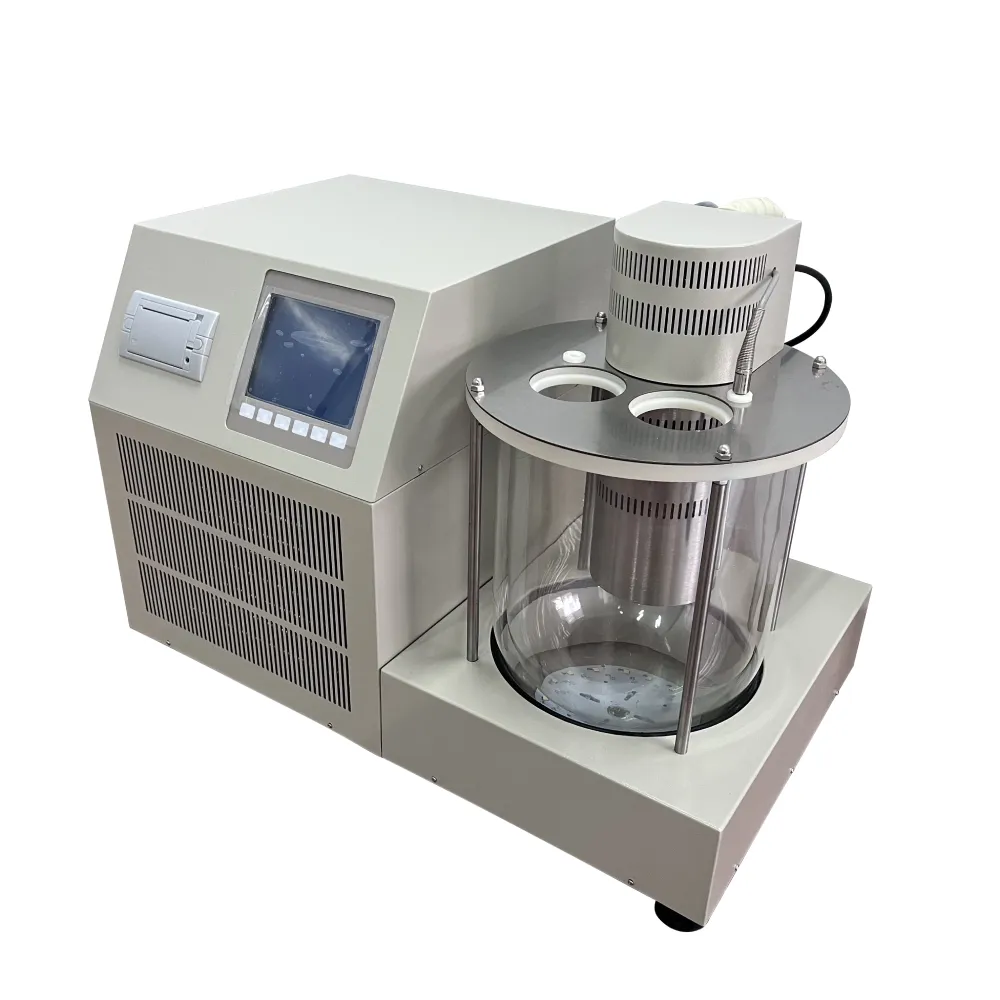
The procedure for conducting a no load loss test involves several key steps, necessitating precision and expertise. The transformer under test is connected to a power source, with the primary winding linked to a variable AC supply, ensuring it operates at the specified rated voltage without any load. Measuring devices are connected to capture the total power input to the transformer. The no load current, along with the voltage and power, is recorded. It is crucial that the testing environment is controlled, and the equipment is calibrated to ensure the validity of the results.
no load loss test of transformer
Expertise in interpreting the results of a no load loss test is equally essential. Engineers must analyze the data collected to ascertain the transformer’s efficiency and to pinpoint any anomalies that may signal potential defects or inefficiencies in the core laminations. Consistently high no load losses may indicate issues such as improper core material, incorrect assembly, or even manufacturing defects. By identifying and addressing these issues early, companies can enhance the longevity and reliability of their transformers, sparking customer trust and brand credibility.
From an authoritative standpoint, adherence to international standards such as IEEE C57.12.90 and IEC 60076-1 is imperative. These standards prescribe the methodologies and acceptable values for no load losses, ensuring that products meet global quality benchmarks. Compliance not only demonstrates a commitment to excellence but also elevates a company's stature in competitive markets.
The credibility of a no load loss test and its results hinges on the trustworthiness of the testing process and personnel. Engaging skilled technicians and employing state-of-the-art testing apparatus form the backbone of a reliable no load loss testing regime. Additionally, establishing robust internal quality control procedures further assures consumers of the product’s integrity and the company's dedication to perfection.
In conclusion, the no load loss test of transformers is a fundamental component of product lifecycle management in the electrical industry. An adept understanding of its intricacies not only aids in enhancing product efficiency and longevity but also cultivates market confidence. As sustainability becomes a pivotal consideration in electrical infrastructure, the role of precise and authoritative no load loss assessments will continue to gain prominence, paving the way for efficient and responsible energy consumption.