No load testing of transformers is a crucial process that ensures the performance and efficiency of a transformer before it is put into full operation. This testing primarily examines the transformer's core, which is central to its functionality and accounts for most of its losses even when not under load. By understanding the nuances of no load testing, businesses can enhance their operational prowess, ensuring longevity and reliability in their electrical distribution systems.
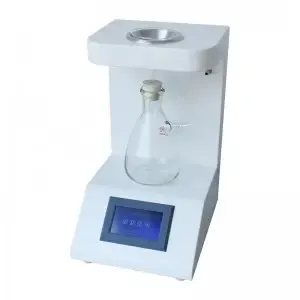
No load testing, sometimes termed open-circuit testing, involves examining the transformer by measuring the excitation current and core losses at rated voltage with no load connected. The objective is to determine two key parameters the core loss and the magnetizing current. These parameters are essential as they directly affect the efficiency and operational cost of the transformer in the long term.
Conducting a no load test provides several invaluable insights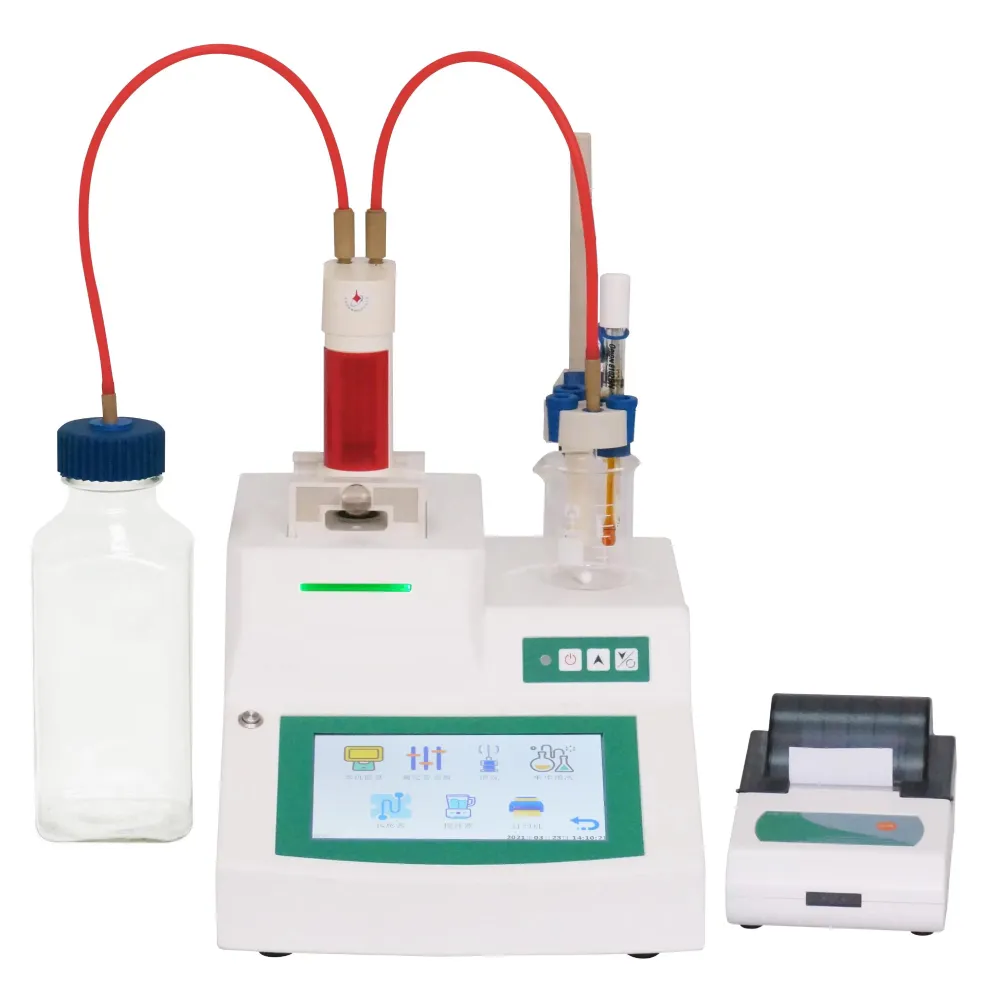
1. Core Loss Evaluation Core loss, also known as iron loss, consists of hysteresis and eddy current losses. It represents the power dissipated in the transformer's core and must be minimized to ensure efficient operation. The no load test measures these losses under standard operating conditions, allowing manufacturers and engineers to identify potential inefficiencies.
2. Magnetizing Current Measurement The magnetizing current is crucial as it reflects the amount of current required to establish the magnetic field in the transformer's core. Lower magnetizing current implies higher efficiency, which is always desirable in reducing operational costs.
3. Verification of Design Specifications By comparing test results against design specifications, manufacturers can verify the quality and performance standard of the transformer. This serves as an assurance that the transformer will perform as expected throughout its operational life.
4. Preventing Overheating and Damage Anomalies detected during no load testing can indicate potential issues in core construction or material quality. Identifying and rectifying these issues early prevents long-term overheating damage, which can lead to premature failures and costly outages.
no load test of transformer
The procedure of conducting a no load test is straightforward yet demands precision. The primary winding of the transformer is connected to an AC supply at rated frequency and voltage, with the secondary winding left open. Instruments such as ammeters, wattmeters, and voltmeters are connected across the primary winding to measure the requisite parameters.
Despite its apparent simplicity, no load testing requires specialized expertise to interpret the results accurately. Parameters such as stray losses and the influence of ambient conditions may distort readings. Therefore, skilled technicians and engineers must use their expertise to adjust for these factors, ensuring accurate results.
To capitalize on the benefits of no load testing, businesses should partner with reputable transformer manufacturers and service providers. This ensures access to advanced testing facilities and experienced professionals who can provide authoritative insights.
Moreover, embracing digital technology by integrating smart sensors and IoT devices allows for real-time monitoring and predictive maintenance of transformers. Such innovations transform conventional no load testing from a periodic process to a continuous, dynamic evaluation.
For organizations aiming to bolster their energy management strategies, investing in comprehensive no load testing is non-negotiable. It directly aligns with the principles of sustainability by optimizing resource utilization and reducing waste. By ensuring transformers operate at peak efficiency, companies not only save on energy costs but also credibly contribute to global efforts in reducing carbon footprints.
As the electrical landscape continues to evolve, adherence to stringent testing protocols like the no load test becomes indispensable. It's not merely about meeting regulatory standards but about establishing a framework of trustworthiness among stakeholders. When transformers perform optimally, operational confidence soars, propelling enterprises toward their goals with unwavering assurance.
By aligning with industry best practices and continuously investing in expertise and technology, companies can ensure that their transformers, and by extension, their entire electrical systems, stand resilient against the challenges of tomorrow.