Transformer coil resistance plays a pivotal role in the electrical efficiency and operational reliability of transformers. As an expert in the field with years of hands-on experience, I have seen how this critical parameter affects transformer performance across varied applications. Understanding and optimizing transformer coil resistance could be the differentiator in achieving peak performance and energy efficiency for your projects.
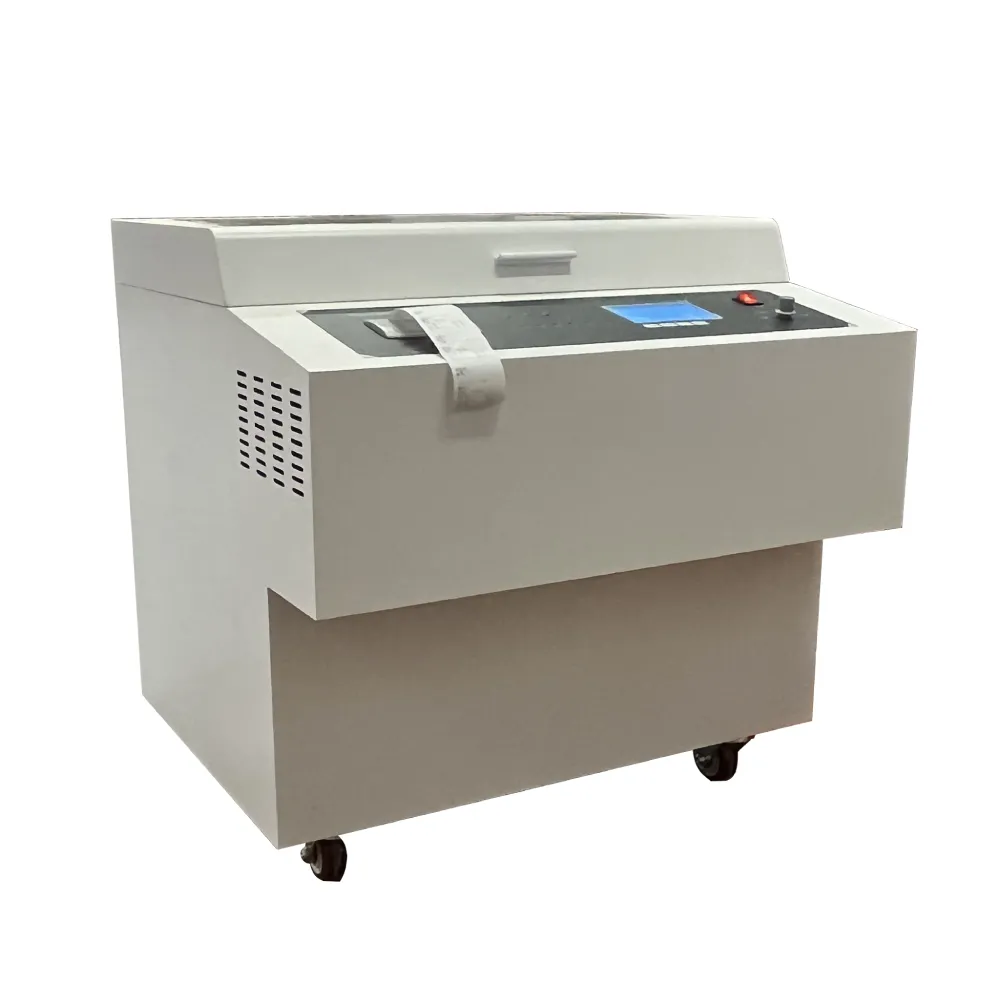
Transformer coils, primarily made of copper or aluminum, take on the fundamental task of transferring energy across different voltage levels. The electrical resistance of these coils is inherently linked to material properties, coil geometry, and operational temperatures. To explore this, we must delve into a few critical aspects.
Firstly, the choice of conductor material Copper and aluminum are the most common materials. Copper has a lower resistivity compared to aluminum, meaning copper transformer coils usually exhibit lower resistance. This lower resistance translates into less power loss and better efficiency, which is why copper is often preferred despite its higher cost and weight. From a reliability and cost effectiveness perspective, selecting the right material aligns directly with product life cycle considerations.
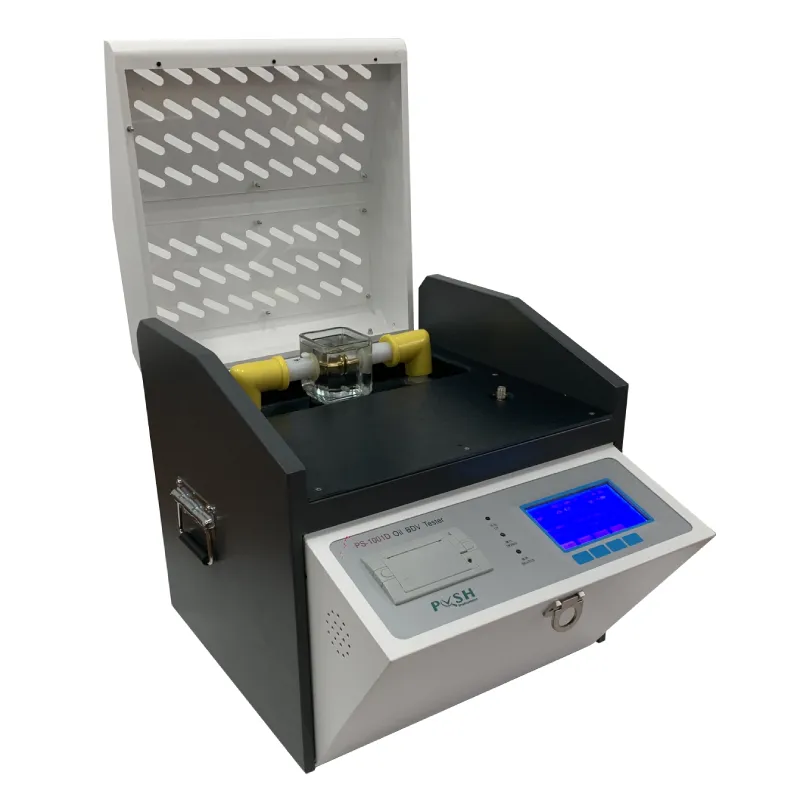
Moreover, the design of the coil is another crucial factor. A well-engineered coil optimizes the balance between turns and spacing to minimize resistance. This is not merely an engineering challenge but an art that combines electrical performance with thermal management. Heat dissipation is crucial for maintaining performance over the long term. Engineers optimize the winding techniques to ensure that the temperature distribution within the coil remains uniform, which aids in attaining a consistent resistance value under operational conditions.
Beyond materials and design, let us not overlook the real-world implications of temperature.
As the transformer operates, the temperature influences resistance. Typically, resistance increases with the temperature, which can impact efficiency and power loss. The choice of cooling methods and thermal management strategies can have substantial effects on minimizing this issue. By implementing advanced cooling techniques, such as oil or air cooling systems, we can effectively manage resistance levels within the transformer coils.
transformer coil resistance
Maintenance is another critical aspect that significantly impacts coil resistance. Regular inspections and monitoring can help in identifying early signs of wear and resistance build-up. Utilizing modern predictive maintenance technologies, such as infrared thermography and ultrasonic detection, allows for non-invasive monitoring of resistance issues, preventing potential failures before they occur. This proactive approach can not only extend the lifespan of transformers but also ensures uninterrupted service, which is essential for power-critical applications.
In the pursuit of optimizing transformer coil resistance, modern technologies play a vital role. Integrating smart sensors and IoT-based solutions provide real-time resistance data, enabling a comprehensive understanding of transformer performance under operational stress. This data-driven insight allows for adaptive maintenance schedules and performance tuning, essential for systems where efficiency and uptime are paramount.
On an authoritative note, industry standards and compliance guidelines often dictate the acceptable ranges of coil resistance. Conformance to these standards ensures that transformers operate safely and efficiently within the electrical grid. As we advance into an era of smart grids and renewable energy sources, adherence to these guidelines becomes even more critical. Collaborating with certification bodies and staying updated with the latest industry research enhances the credibility and reliability of transformer designs.
In conclusion, transformer coil resistance is more than a static property; it is a dynamic characteristic that influences and is influenced by many factors. Expertise in selecting materials, designing coils, managing heat, and conducting maintenance is crucial. Adhering to industry standards ensures system integrity and reliability. As an authority in this field, leveraging technology for continuous monitoring and adopting a proactive approach in managing transformer coil resistance will position you ahead in achieving operational excellence and energy efficiency.