The inductor saturation tester is a critical tool for anyone involved in the design or maintenance of electronic circuits, particularly those utilizing inductors in power electronics, RF applications, or filter design. Understanding its importance and functionality can significantly enhance both performance and reliability in various electrical applications.
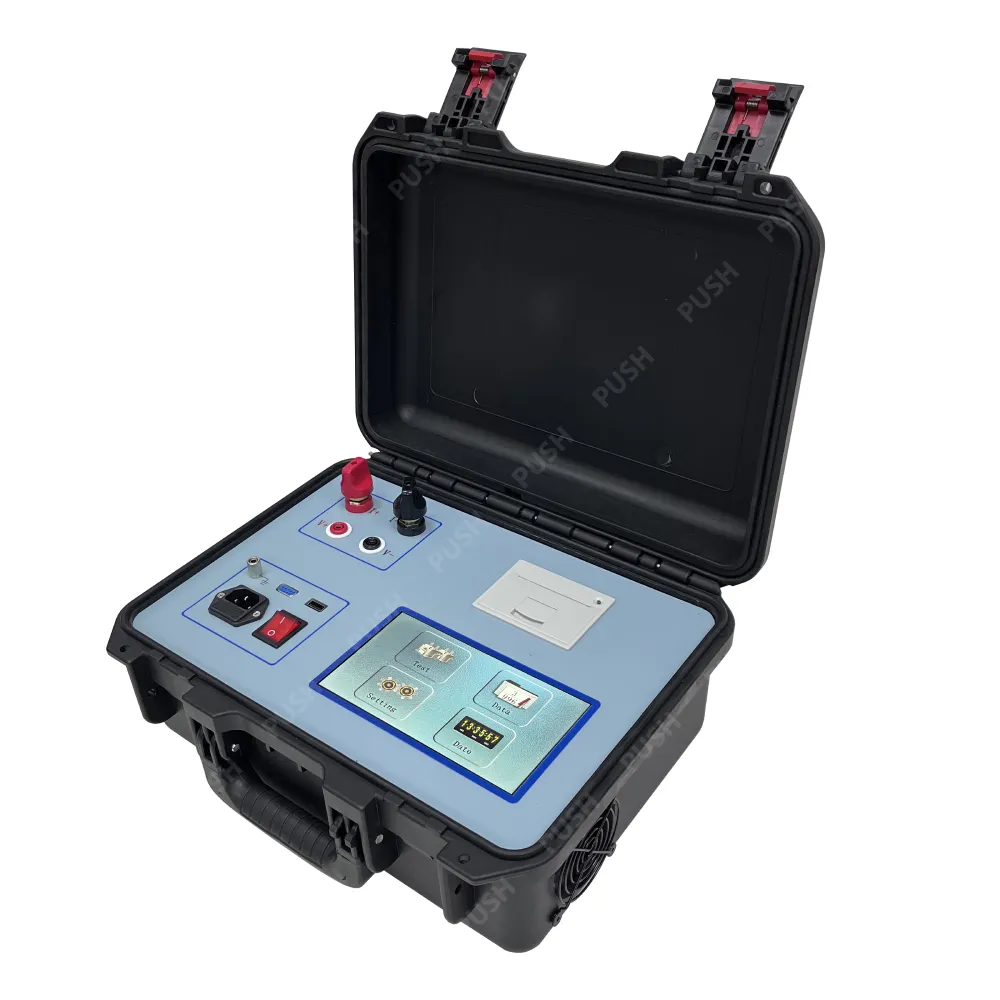
Inductors, key components in many electronic devices, are often used to store energy and filter signals. However, these components are prone to a phenomenon known as saturation, where they no longer behave linearly. Beyond this point, their ability to store energy diminishes, causing inefficiencies and potential circuit failure. An inductor saturation tester is designed to address this precise challenge, allowing for precise characterization and optimization of inductors.
In practice, employing an inductor saturation tester unveils the limits of an inductor’s performance under different conditions. By simulating operating environments and testing inductors to saturation, engineers can determine the maximum current an inductor can handle before it saturates. This data is invaluable for tailoring design specifications to ensure components operate within safe margins, thereby boosting the circuit's robustness and efficiency.
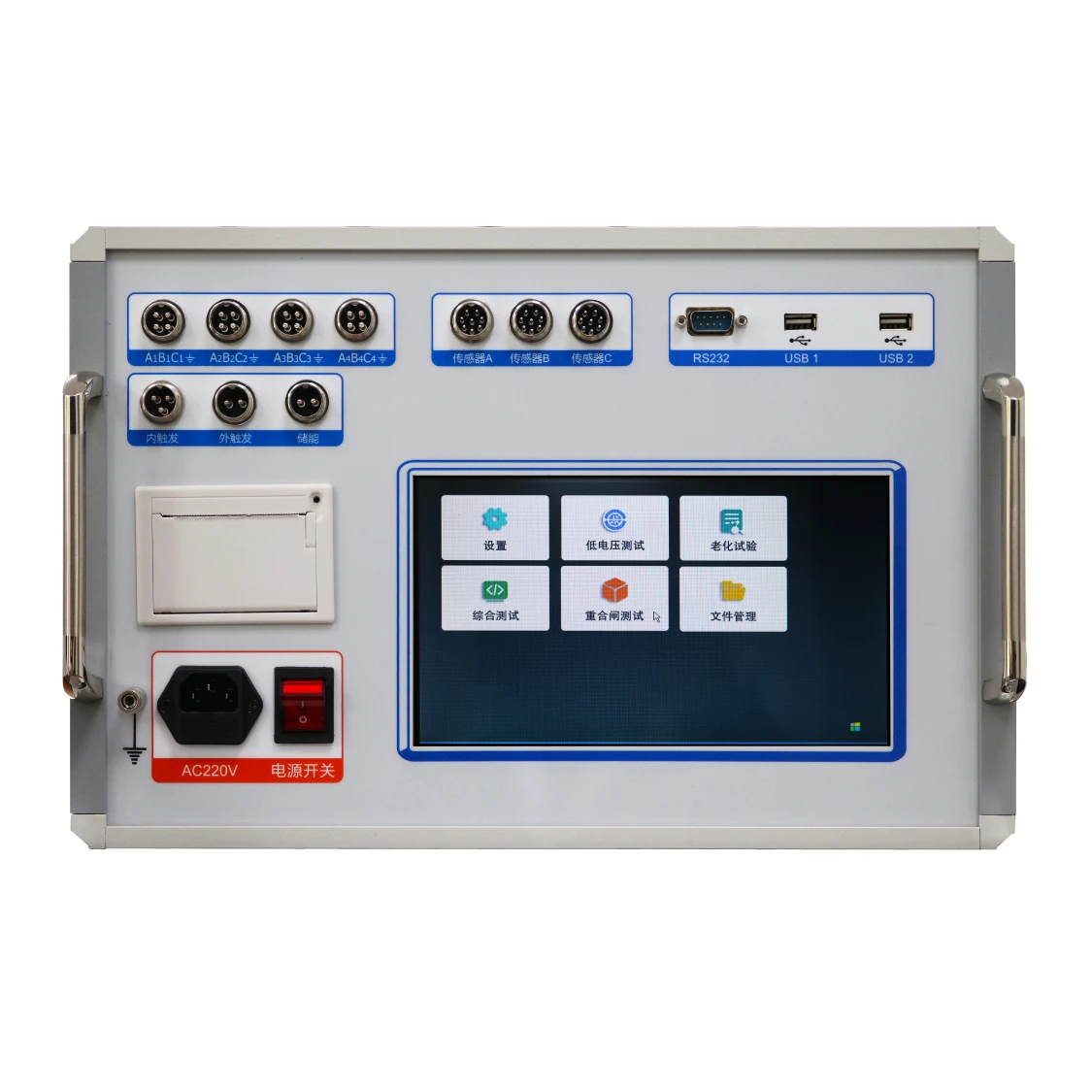
Experts in electronic design understand that selecting the correct inductor involves balancing various parameters such as inductance, current rating, and core material type. An inductor saturation tester furthers this by providing insights into how these parameters interact under duress. Its readings can inform decisions on whether to upgrade to a different core material or model to mitigate saturation risks, a crucial step for optimizing performance in high-power applications.
A reliable inductor saturation tester can distinguish between inductors crafted from different core materials like ferrite, powdered iron, or amorphous cores. Each material has distinct properties, with varying susceptibility to saturation.
For instance, ferrite cores might saturate more quickly than powdered iron at certain frequency ranges. Utilizing data from saturation testing guides engineers in selecting the appropriate materials and designs, preventing suboptimal performance in the final application.
inductor saturation tester
From a professional standpoint, leveraging an inductor saturation tester is illustrative of expertise in electrical engineering. It demonstrates a commitment to quality control and deep understanding of circuit dynamics. By preemptively identifying potential failures, engineers not only adhere to industry standards but also cultivate trust with stakeholders, knowing that all components have been rigorously tested and validated.
In terms of authority, manufacturers and product developers who incorporate saturation testing into their quality assurance protocols position themselves as leaders in innovation and reliability. Detailed performance knowledge allows them to differentiate products, offering superior solutions that promise endurance and efficiency.
Trustworthiness is inherent in transparency with stakeholders about the performance limits identified through saturation testing. By clarifying the parameters under which devices operate optimally, businesses can set realistic expectations, reducing returns and boosting customer satisfaction.
In summary, the role of an inductor saturation tester extends beyond basic testing into realms of enhanced design efficacy and reliability assurance. Its use underscores a comprehensive understanding of electronic components, enabling the creation of safer, more efficient circuits. Through data-driven decisions powered by saturation testing, electronic design achieves superior standards, driving industry innovation and trust.