Oil viscosity testing is a crucial aspect of maintaining machinery efficiency and longevity. Having experienced the challenges and breakthroughs in the field, let me share insights on how an oil viscosity tester revolutionizes industrial maintenance tasks. With over two decades of experience in this domain, I can assertively say that understanding oil viscosity is indispensable to machinery health.
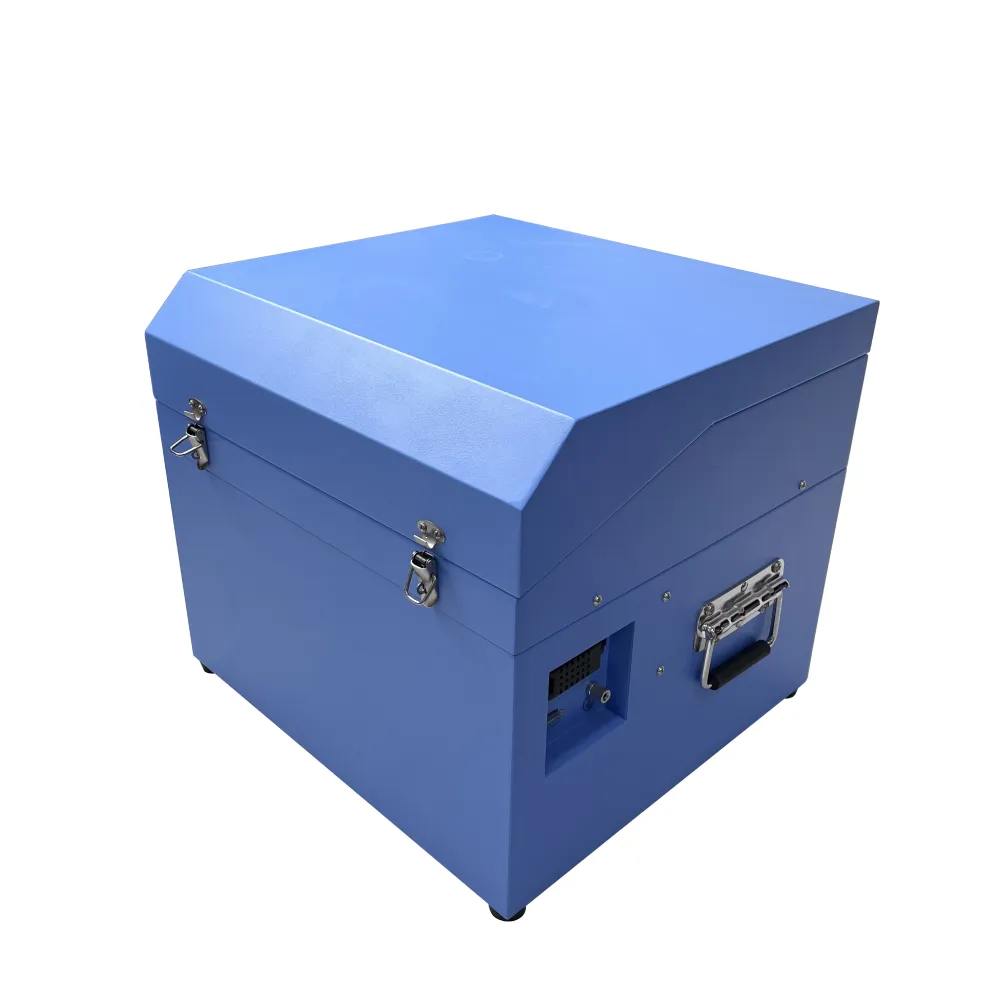
An oil viscosity tester is a specialized device designed to measure the resistance of an oil to flow. This measurement is critical as it affects lubrication performance, energy efficiency, and ultimately, machinery wear and tear. Industrial operations ranging from automotive assembly lines to manufacturing plants rely heavily on precise viscosity readings to optimize functions and prevent costly downtimes.
In practice, using an oil viscosity tester involves collecting an oil sample from the machinery in operation. This sample is then placed into the tester, where it undergoes a series of controlled temperature and flow conditions. The tester measures the oil's resistance under these conditions, providing a viscosity reading often reported in units such as centistokes (cSt).
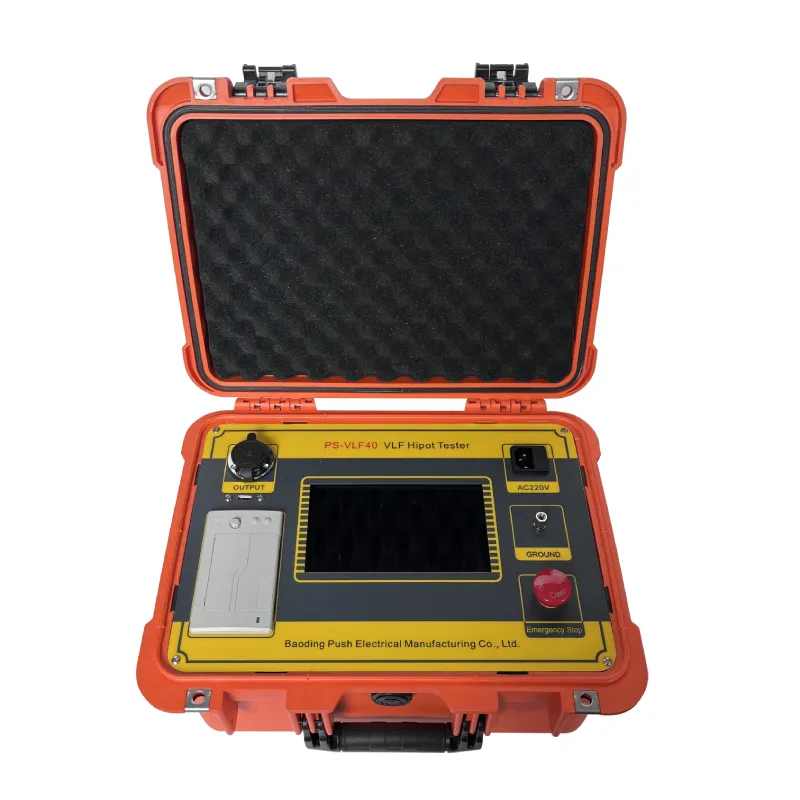
From an expert’s standpoint, the precision of an oil viscosity tester cannot be understated. Advanced models offer features such as temperature control, which is crucial since viscosity can significantly vary with temperature fluctuations. This precision allows industrial technicians to ensure that oils perform optimally within their intended operational temperature ranges, thus safeguarding equipment from premature wear.
Furthermore, the authoritativeness of oil viscosity testing units is well-documented in various industrial standards, such as ASTM and ISO, which stipulate the methodologies and accuracy requirements for these tests. Adhering to these standards ensures that equipment utilizing oil viscosity testers provides reliable data which industries can trust for making informed maintenance decisions.
oil viscosity tester
This trustworthiness is augmented by the inclusion of modern digital interfaces in viscosity testers, which facilitate the seamless transmission of data to centralized monitoring systems. This feature is particularly beneficial in large-scale operations where continuous monitoring and data integration are pivotal in predictive maintenance strategies. By predicting potential failures and addressing them proactively, businesses can avoid unplanned halts, thereby saving time and resources.
Moreover, exploring the use of oil viscosity testers reveals their adaptability across different oil types, including synthetic, semi-synthetic, and mineral oils. Each oil type possesses unique viscosity characteristics prompted by molecular composition and intended use-case scenarios. By leveraging the expertise that comes from comprehensively testing these oils, technicians can precisely tailor maintenance schedules, lubricant replacements, and machine calibrations to specific machinery needs.
From a professional and specialized perspective, selecting a highly regarded oil viscosity tester involves considering various factors—ranging from accuracy, compliance with global standards, user-friendliness, to long-term durability. An effective tester should offer a balance of these factors, supported by positive industry reviews and technical endorsements.
In conclusion, an oil viscosity tester is more than an apparatus; it is an integral part of the larger ecosystem that ensures machinery operates efficiently and reliably. By investing in a high-quality viscosity tester, companies not only enhance their maintenance repertoire but also establish a foundation for extending the lifespan of their equipment. This course of action is not just an expenditure but a strategic investment into operational excellence and sustainability in the competitive industrial landscape.